Koenig & Bauer attaches extraordinarily high importance to its responsibility, which is firmly anchored in its corporate values. As a pioneer of in-company social policies, we have taken our responsibility towards our employees seriously ever since our Company was first established 205 years ago. With our diverse initiatives for emission-reduced and resource-saving products and production processes along the entire value chain, we are committed to the preservation and conservation of the environment. As a sustainability enabler, we want to support our customers around the world in their sustainability efforts. Corporate social responsibility by means of donations and sponsoring is also part of Koenig & Bauer’s corporate identity. Integrity in our business activities and respect for human rights are core elements of our corporate governance practices. With our strategic sustainability goals, we seek to address our social, ecological, social and ethical responsibilities and develop our Company sustainably.
The sustainable further development of our Group is one of the pillars of our “Exceeding Print” corporate strategy, which includes a wide range of activities targeted at environmental, social and governance (ESG) concerns. As a provider of solutions and a technology partner to our customers, we want to support them in reducing their ecological footprint. Various eco-components and innovative technical solutions that we have developed help to reduce carbon emissions by lowering energy consumption, waste and the use of other resources such as paints and varnishes. Ecodesign criteria are taken into account in the Group’s new and further developments. By applying detailed sustainability profiles, we want to highlight energy consumption and the potential for saving energy, waste and other resources by means of various eco-components and innovative technical solutions. We are working on algorithms and software solutions to individually calculate the product carbon footprint (PCF) as an additional feature in the sale of carbon-neutral presses. The carbon footprint calculated can be offset by means of certified climate protection projects, while a carbon-neutral printing press is available to customers. We are aiming to reduce by 2025 the carbon emissions (Scope 1 and 2) of our production plants by 75% compared with 2019 and to achieve carbon neutrality from 2030 onwards. Following an analysis of the current Scope 3 carbon emissions, we want to define measures and corresponding targets for reducing these emissions in a timely manner. Another key objective is to promote the health of our employees, to prevent work-related hazards and to minimise the number of accidents at work as far as possible. In addition, we want to further increase the degree of diversity already achieved in terms of gender, age, international background and experience. One priority in this regard is the “Level Playing Field Women” project, which is currently being stepped up. In addition to diversity as an element of our corporate culture, we want to make use of various activities to take a stand against racism and discrimination. And, finally, we are committed to the preservation and conservation of the environment along our supply chain through the integration of sustainability in the procurement process and the fulfilment of comprehensive due diligence obligations. At the Koenig Bauer & Group, we accept our responsibility towards the community.
As a UN Global Compact participant, Koenig & Bauer is actively supporting the implementation of the United Nations’ 17 Sustainable Development Goals (SDGs), which define the framework for responsible business in economic, ecological and social terms. The UN Global Compact is the world’s largest sustainability initiative for sustainable and responsible corporate governance. The participants have undertaken to support the ten principles of the UN Global Compact in the fields of human rights, labour standards, environmental protection and the fight against corruption, to promote the 17 SDGs within their respective spheres of influence and to report annually on the progress achieved. Koenig & Bauer has identified seven of these SDGs as priorities and is addressing them with strategic sustainability initiatives. In particular, the Group’s diverse sustainability activities are targeted at the following SDGs: “3 – Good health and well-being”, “4 – Quality education”, “5 – Gender equality”, “8 – Decent work and economic growth”, “12 – Responsible consumption and production”, “13 – Climate action” and “17 – Partnerships for the goals”. We see our scope for influence and for making a difference in these goals.
We have also joined the Blue Competence sustainability initiative. Blue Competence is an initiative launched by German industry association VDMA to promote sustainability in mechanical and plant engineering as well as to further sustainable solutions in this industry. Furthermore, we became the first printing press manufacturer to join the Healthy Printing Initiative in July 2021. The basic idea underlying the initiative is to advance the implementation of the cradle-to-cradle design approach in the printing industry. Accordingly, the initiative aims to promote the use of environmentally friendly substrates, inks, varnishes and auxiliaries in the printing of paper, corrugated board and cardboard products, plastics and other substrates and ultimately to enable efficient recycling systems. Koenig & Bauer is also a member of the 4evergreen alliance, which networks paper and board manufacturers, folding carton manufacturers, producers and retailers of brand-name products and suppliers of technology and materials as well as the collecting, sorting and recycling industry. The alliance aims to communicate more effectively the benefits of fibre-based packaging materials as alternative solutions and to achieve a recycling rate of 90% for them by 2030. Finally, as a member of the Holy Grail 2.0 initiative, we are working towards finding a common solution for intelligent packaging recycling. Under the auspices of the European Brands Association (AIM), numerous companies and organisations along the packaging value chain are pooling their expertise. Stamp-sized digital watermarks that can be printed on the surface of packaging and function as a “digital recycling passport” are a promising approach for an efficient circular economy. Since 2022, Koenig & Bauer has been a member of the innovation network for “climate-neutral companies”, which under the direction of the Fraunhofer Institute for Industrial Engineering in Stuttgart promotes the cross-sector transfer of knowledge in the areas of climate protection and sustainability. The focus is on energy supplies, company mobility, digital/hybrid forms of work, strategy and governance as well as employee awareness.
Disclosure option selected
Koenig & Bauer publishes the non-financial disclosures required under section 315c in connection with sections 289c to 289e of the German Commercial Code and the disclosures required under Regulation (EU) 2020/852 of the European Parliament and of the Council of 18 June 2020 on the establishment of a framework to facilitate sustainable investment and amending Regulation (EU) 2019/2088 (hereinafter referred to as the EU Taxonomy Regulation) in this separate non-financial Group report, which is published outside the combined management report. References to disclosures outside the Group’s non-financial report constitute further information and are therefore not part of the report. The two separate reports are published in Bundesanzeiger together with the independent auditor’s opinion; they are also published on the Company’s website at https://investors.koenig-bauer.com/en/publications/financial-reports-and-statements/.
Business model, non-financial risk report and materiality analysis
The Koenig & Bauer Group’s business model is presented in the combined management report (see pages 16 onwards of the 2022 annual report). Koenig & Bauer’s Management Board is responsible for sustainability, including non-financial reporting on the environmental, employee and social aspects defined by law, the observance of human rights and anti-bribery and anti-corruption precautions. Under the Management Board’s business allocation plan, the Chief Executive Officer is responsible for corporate responsibility (ESG) and, hence, for all reported non-financial aspects. Sustainability has been established as a new area of responsibility with direct reporting lines to the Chief Executive Officer. Individual ESG objectives are a component of the Management Board’s remuneration as an element of the short-term incentive (STI), see the comments in the remuneration report on pages 117 onwards. Under a resolution passed by the Supervisory Board on 20 September 2022, the Audit Committee assumed responsibility for sustainability/ESG from the Personnel Committee. At an extraordinary meeting held on 20 October 2022, the Audit Committee completed a comprehensive onboarding process covering all ESG-related matters. In addition to regular updates for the Audit Committee in the future, the entire Supervisory Board is briefed by the Management Board on the progress of ESG activities at the annual strategy day. Within the scope of its statutory duty of supervision, the Supervisory Board has engaged PricewaterhouseCoopers GmbH Wirtschaftsprüfungsgesellschaft to audit this separate non-financial consolidated report to obtain limited assurance (see the audit report on pages 170 onwards of the annual report).
A materiality analysis was conducted to define the main aspects of the non-financial Group report. In accordance with the CSR Directive Implementation Act (sections 315c/289c of the German Commercial Code), the analysis is composed of the following elements: environmental, employee and social matters, observance of human rights and anti-bribery and anti-corruption precautions. In a preliminary step, a comprehensive list of non-financial matters potentially of relevance for customers, employees, investors and business partners was prepared with respect to these five aspects in accordance with the German Commercial Code. On the basis of this list, a workshop was held at the end of 2018 to identify the non-financial issues that are of material importance for our business activities and relationships, products and services within the five main aspects identified in accordance with the German Commercial Code. A short list was then prepared setting out all the matters which on a scale from 0 (not material or relevant) to 10 (highly material or relevant) had an average materiality score of at least 5 for the main issue in question and its business relevance. These material non-financial items were included in the non-financial Group reports for 2018 and 2019, as well as in the non-financial Group report for 2020 after a review of the materiality analysis.
To review and, if necessary, supplement the non-financial aspects reported on so far, we again performed a comprehensive materiality analysis at the end of 2021 with external and internal stakeholders on the basis of an online questionnaire. This was aligned to the 2016 version of the Sustainability Reporting Standards of the Global Reporting Initiative (GRI). The internal respondents were managers and experts from operations management, production, service, personnel management, personnel development, quality management, product management and innovation, construction, development & process technology, safety/health/environment, facility management, compliance & internal auditing & risk management, corporate strategy, business/corporate development, marketing and communications. All business units and, in particular, employee representatives across the Group were involved. In addition to industry representatives from other components industries, the external stakeholders questioned primarily included customers and producers of brand-name articles as well as their customers together with banks, scientific experts and students. A response rate of 57% was achieved for the online questionnaires. On a scale from 0 (not material) to 10 (highly material), the participants assessed the non-financial matters on which the Company had previously reported in two re- spects, namely their influence on the applicable non-financial aspects and their business relevance for the Company. The participants did not propose any additional material non-financial aspects in the materiality analysis. The points mentioned had already been covered by earlier reports. All non-financial matters with an average score of at least 5 for both aspects were included in the materiality matrix. The following materiality matrix summarises the results:
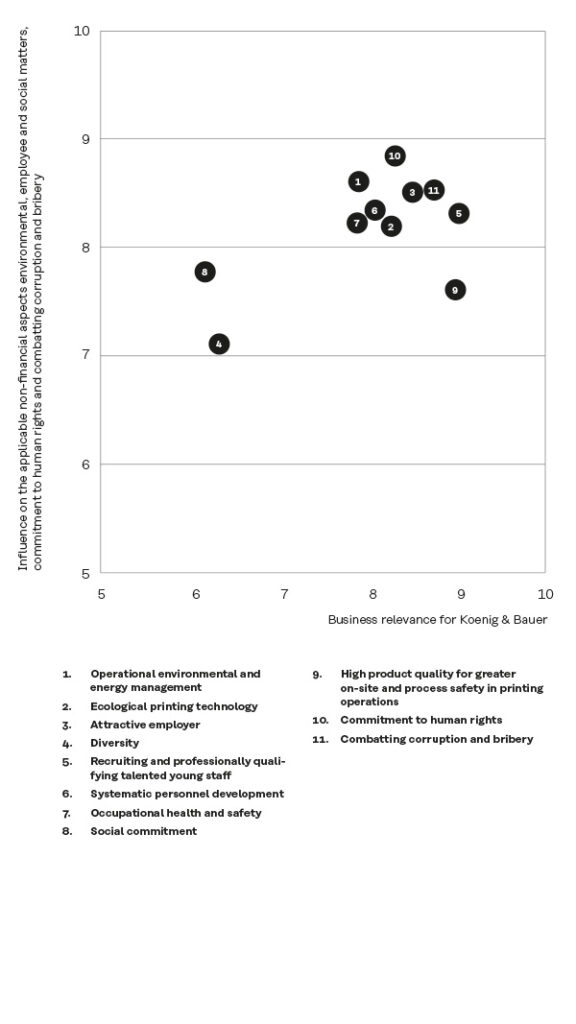
The facts and issues presented in this materiality matrix are also to be included in the non-financial Group report for 2022. In addition to approval by the Chief Executive Officer, the Audit Committee of the Supervisory Board also took note of this procedure at its extraordinary meeting on 2 February 2023. Accordingly, the sections below describe the following main non-financial issues: Environmental aspects entail the Company’s environmental and energy management as well as ecological printing technology. In addition to our appeal as an employer and the need for diversity, the key employee-related aspects include recruiting and training junior specialists and managers, systematic personnel development as well as health and safety. With respect to social aspects, social responsibility and high product quality in the interests of greater work and process safety in printing operations have been defined as material. This is followed by the aspects of the Company’s commitment to human rights and as well as anti-corruption and anti-bribery precautions.
The risk inventory conducted at the end of 2022 did not identify any material, reportable non-financial risks resulting from business activities, business relationships, products or services that have an adverse impact on the non-financial aspects mentioned. Risks that affect the Company externally are presented in the risk report in the combined management report (see pages 35 et seq. of the annual report 2022).
Environmental aspects
At Koenig & Bauer, environmental aspects and the observance of high quality and safety standards are taken into account as far as possible along the entire value chain, from the product idea and purchasing to production and the start-up of the printing presses. Right from the start of the development and design stage, attention is paid to energy and resource efficiency in the assembly and operation of printing presses and finishing equipment. A further focus is placed on minimising noise, dust, odour and carbon emissions during the production and utilisation of our presses as well as the use of environment-friendly substrates and consumables in the printing, finishing and postpress phases. There are different management approaches for the two thematic complexes of corporate environmental and energy management as well as ecological printing technology for customers.
Operational environmental and energy management
Effective environmental and climate protection in the plants as well as the responsible use of resources are priorities for Koenig & Bauer. The production plants in Radebeul, Würzburg and Dobruška hold DIN EN ISO 9001:2015 and DIN EN ISO 14001:2015 quality and environment certification. In addition, our foundry in Würzburg operates an energy management system that has been certified in accordance with DIN EN ISO 50001:2018. A permanent focus of our work is on minimising the consumption of energy and resources in production as well as on reducing workplace emissions. We are consistently investing in efficient technologies and equipment to this end. As every reduction in the consumption of energy and resources is reflected in lower carbon emissions, Koenig & Bauer is also contributing to climate protection in this way. To protect and restore biodiversity and ecosystems, we have planted flowering and bee meadows at various Group sites, such as in Radebeul and Löhne. Further areas for flower and bee meadows, particularly at the Group site in Würzburg, are planned.
With regard to our ecological responsibility, we want to proactively drive forward and achieve the defined goal of carbon neutrality by 2030 at our production plants. In addition to the financial indicators and ROI calculations used ahead of capital expenditure decisions, we revised the Group Capex Framework Directive in the year under review to consistently monitor the sustainability impact of capital expenditure. Alongside the mandatory assessment of all capital expenditure plans in the Group based on an environmental score tool used by the requester of the capital expenditure, information from the Corporate Responsibility department on the sustainability impact of the planned capital expenditure is also required from a threshold of 20 thousand euros or more. The tool for calculating the environmental score of planned capital expenditure was developed on the basis of a idea developed by the Tapasuna (“take part, sustain nature”) project group within the the Junior Management Programme (JuMP). With the environmental score tool provided on the intranet together with an instruction and FAQ document, capital expenditure projects can be evaluated on a group-wide basis in a standardised, comparable and efficient manner to determine their contribution to improving sustainability. The environmental score calculated with the tool equals the value of the capital expenditure in thousands of euros per total tons of carbon saved. Together with the numerical environmental score for the capital expenditure under consideration, the tool implemented from 2023 onwards also categorises the capital expenditure according to classes A to G. Class A carbon savings achieved through the planned capital expenditure are the highest and the quotient the lowest. By contrast, class G capital expenditure projects are less energy-efficient relative to the capital invested. If, as is the case with new capital expenditure plans, no energy or resource reference data is available to calculate the carbon savings potential, a check using soft facts based on the ESG (environmental, social and governance) criteria is required at a minimum.
We are also working on improving the carbon footprint in our plants by adopting a green energy policy, which also includes measures to boost energy efficiency. Since the beginning of 2021, we have been sourcing solely green electricity produced from hydroelectric power in Norway for our main Group sites in Würzburg and Radebeul as well as at some subsidiaries. The Radebeul site is to switch to largely carbon-neutral district heating supplies using green energy before the onset of the 2023/2024 heating season. Our supplier GETEC mainly relies on biomass from wood pellets and also on solar thermal energy for the provision of district heating. In 2022, we installed three photovoltaic systems with an annual output of around 600,000 kWh at our Würzburg site to expand our own power production facilities. As well as this, three solar thermal systems for hot water supplies went into operation and can save around 50,000 kWh of electricity per year. At the Würzburg, Radebeul, Löhne, Mödling and Dobruška sites, further capital expenditure projects for photovoltaic systems have been initiated to enhance energy self-sufficiency by generating more electricity internally. At the Lausanne site, preparations are underway for the installation by the property owner of a photovoltaic system on top of the building roof. Scheduled to go into operation in October 2023, it will cover 18% of the Swiss subsidiary’s total electricity requirements. Alongside the internal production and use of green energy, conservation and energy efficiency at our plants from another important pillar of our green energy policy. In addition to the replacement of transformer stations and ventilation technology, this is being aided by the modernisation of production and distribution systems for electricity, compressed air and heat at the Group sites. Another component in our efforts to reduce electricity consumption while simultaneously improving working conditions is the accelerated replacement of lighting systems with highly efficient, automatically controlled LED technology at our sites. The corresponding investments and expenses are included in the taxonomy-eligible Category C capital expenditure and operating expenses (see the section on the EU taxonomy).
At the foundry in Würzburg another major step towards greater sustainability is being planned with the installation of a new melting plant. When the two new medium-frequency melting furnaces featuring the latest technology go into operation in summer 2023, only a fraction of the previous melting time will be required, thus significantly improving the energy efficiency of the melting process. The new foundry melting furnaces consume 30% less electricity. As well as this, significant quantities of energy can be fed into the plant’s internal heating network thanks to the optimised utilisation of waste heat. This means that the amount of gas required for heating the buildings at the Würzburg site can be cut by 8%. In absolute terms, this translates into an annual reduction in electricity consumption of around 3 GWh and in gas consumption of around 1 GWh. Moreover, the closed-end water cycle can lower annual water consumption by over 9,000m3 and reduce the chemical substances required.
At the Würzburg site, sustainable heat sources such as geothermal energy, river water and ground collectors are being tested for use in connection with large heat pumps. In spring 2023, a thermal response test will be performed at the Würzburg site to test the potential use of brine groundsource heat pumps.
Dedusting, extraction and solvent distillation plants as well as improved sound insulation in the production and assembly halls reduce workplace emissions such as noise, dust and odour. Supply air systems ensure fresh air at a controlled temperature directly at the workplace. Responsible use of resources also includes sustainable waste management. We avoid waste as far as possible, while waste that cannot be avoided is disposed of or recycled appropriately in accordance with the legal requirements. With disposal activities, a distinction is drawn between hazardous and non-hazardous materials and between waste recycling and removal. The remeltable metal waste generated in metal-cutting activities in Würzburg is an important raw material in foundry operations. Our waste statistics provide detailed information about the type and quantity of waste produced, broken down according to hazardous and non-hazardous waste. The padding used for the worldwide shipment of alphaJET models by Koenig & Bauer Coding in proven wooden crates was replaced by recycled material in the year under review. The new substrate consists of 80% regenerated material and lowers the carbon emissions for the padding material by 70%.
The following table provides an overview of electricity, natural gas, district heating, water consumption and waste in 2022 compared with the previous year.
2021 | Würzburg | Radebeul | Total |
Electricity | 21,445,986 kWh | 13,205,058 kWh | 34,651,044 kWh |
Natural gas | 13,059,762 kWh | – | 13,059,762 kWh |
District heating | – | 12,171,600 kWh | 12,171,600 kWh |
Water | 26,895 m3 | 16,059 m3 | 42,954 m3 |
Amount of waste | 4,657 t | 5,313 t | 9,970 t |
2022 | Würzburg | Radebeul | Total |
Electricity | 22,948,789 kWh | 13,011,905 kWh | 35,960,694 kWh |
Natural gas | 10,789,041 kWh | – | 10,789,041 kWh |
District heating | – | 9,402,600 kWh | 9,402,600 kWh |
Water | 30,855 m3 | 15,671 m3 | 46,526 m3 |
Amount of waste | 4,459 t | 4,838 t | 9,297 t |
On the basis of these consumption figures, Scope 1 CO2e emissions at the main sites in Radebeul and Würzburg came to 3,407.3 t in 2022, down from 3,803.4 t in the previous year. This reduction was underpinned by significantly lower gas consumption. The location-based Scope 2 CO2e emissions amounted to 16,351.7 t, compared with 15,248.7 t in the previous year. This increase was particularly due to the emission factors for the German electricity mix, which rose from 380 g/kWh in the previous year to 410 g/kWh. The calculations for location-based Scope 2 CO2e emissions are derived from the provisional average emission factors for the German electricity mix published by Bundesverband der Energie- und Wasserwirtschaft (Federal Association of Energy and Water Management). The increase in specific emissions from electricity production in Germany resulted primarily from the greater volume of electricity produced at lignite- and hard coal-fired power plants. The rise in carbon emissions due to increased electricity production from renewable energies had a dampening effect. By contrast, the market-based Scope 2 CO2e emissions were again reduced from the previous year’s figure of 4,727.3 t to 3,651.9 t, particularly as a result of the significantly lower consumption of district heating.
After an initial rough analysis of the Scope 3 carbon emissions in the previous year, a new calculation was carried out for 2022 with external assistance using a larger number of product archetypes in the business units together with higher granularity in the emission factors. All 15 Scope 3 categories of the Greenhouse Gas Protocol were included in the analysis and the emissions calculation is based on the categories relevant to the Koenig & Bauer Group. The Scope 3 carbon emissions for the previous year were also adjusted on the basis of this more precise analysis. This resulted in Scope 3 CO2e emissions of 2,303 kt for 2022 (2021: 2,684 kt). At over 99%, Scope 3 CO2e emissions again account for the largest share of Koenig & Bauer’s carbon footprint. Accounting for roughly 93% of the total, downstream product usage is the largest driver of Scope 3 emissions. Accordingly, top priority is being given to lowering the energy consumption of products by improving their energy efficiency, expanding digital services such as artificial intelligence for optimum press utilisation and offering the “climate-neutral print production” service. On the upstream side, the strategic orientation in purchasing activities in favour of materials with the lowest possible carbon footprint and the more responsible transportation of materials, finished products and service parts provide further levers for reducing Scope 3 carbon emissions. A reduction in carbon emissions can also be achieved through targeted incentives directed at employees’ commutes to work. In addition to the public transport season ticket offered, the planned expansion of the e-charging infrastructure at the employee car parks should contribute to this.
The following table provides an overview of the Scope 1, 2 (Radebeul and Würzburg sites) and 3 (Group) CO2e emissions in t and the CO2e intensity in t per 1 million euros of revenue:
2021 | 2022 | |
CO2e emissions (tons) | ||
Scope 1 (gas and vehicle fleet) | 3,803.4 | 3,407.3 |
Scope 2 (electricity and district heating) – location-based | 15,248.7 | 16,351.7 |
Scope 2 (electricity and district heating) – market-based | 4,727.3 | 3,651.9 |
Scope 3 (indirect emissions upstream and downstream) | 2,684,000.0 | 2,303,000.0 |
CO2e intensity (tonnes per 1 million euros of revenue) | ||
Scope 1 (gas and vehicle fleet) | 3.4 | 2.9 |
Scope 2 (electricity and district heating) – location-based | 13.7 | 13.8 |
Scope 2 (electricity and district heating) – market-based | 4.2 | 3.1 |
Scope 3 (indirect emissions upstream and downstream) | 2,405.4 | 1,942.3 |
Another direct contribution to climate protection can be achieved through sustainable travel management. Restrictions in business travel to a limited number of participants and important occasions is a significant sustainability lever. In addition, the carbon footprint of every business trip can be significantly improved by means of targeted travel planning including the selection of the method of transport. Koenig & Bauer has modified the Group Policy on Company Travel to reflect this strong commitment to more sustainable business trips.
Ecological printing technology
We view sustainability and climate protection as part of our responsibility
towards future generations, especially with regard to our products. Specifically, this is already opening up a wide range of opportunities for placing
new products, equipment options and services on the market and for
standing apart from the competition. Accordingly, we pay attention to energy and resource efficiency in the production process and in the operation
of the presses and equipment when developing and designing our products. A further focus is placed on minimising noise, dust, odour and carbon emissions during the production and utilisation of our presses as well as the use
of environment-friendly substrates and consumables in the printing, finishing and postpress processes. When considering the environmental impact
of our products, we also take account of the recyclability of the equipment.
The main components such as steel and grey cast iron are fully recyclable.
We incorporate energy-saving technologies in our new and enhanced products to lower carbon emissions in industrial printing. Koenig & Bauer offers a range of energy-saving alternatives for the drying process, which is one of the most energy-intensive functions in printing operations. The VariDryBlue drying system that we have developed in the sheetfed sector is an energy-efficient solution. Energy requirements for drying water-based dispersion coating can be reduced by 22%. This is done by using the hot air twice in the drier modules. HR and LED dryer modules for interim and final drying are powerful but more efficient alternatives to conventional UV dryers. Waste can be saved and makeready times shortened by means of various quality measurement and control systems, inspection systems, preset functions and other equipment options. This allows customers to significantly increase the resource efficiency of their printing operations. In the year under review, a new technology was developed for the dryers of the AirTronic collectors fitted to sheetfed offset medium-format presses, which can reduce the component’s energy consumption by up to 40%. By increasing the number of hot air nozzles and optimising them by means of integrated IR emitters and improved exhaust air routing via the sides instead of upwards, superior heating performance and a higher overall temperature level is achieved, which, in addition to boosting energy efficiency, improves the drying process and, thus, the drying result.
In the metal printing presses built by Koenig & Bauer MetalPrint, the HighEcon dryer, which has won the METPACK Innovation Award, cuts gas costs by up to 70% compared to older models thanks to the newly developed high-efficiency KXB burner. With the EcoTNV dryer, the solvent-laden air is fed into the thermal afterburner during drying. In integrated systems such as the HighEcon or EcoTNV dryers, the exhaust air is generally not only cleaned but also produces the heat for the dryer. The solvents in the exhaust air are used to save energy. Thus, if the solvent concentration in the exhaust air is sufficient, gas consumption can be kept to a minimum.
In banknote printing, we have developed a system for reducing the carbon emissions of intaglio presses by lowering power requirements. Intaglio presses require a wiping solution which must be pre-heated before use. On the other hand, some parts must be cooled by means of thermoregulation. In order to conserve and reuse energy, a power-saving unit has been developed to harness the synergistic effects between thermoregulation and the provision of a preheated wiping solution. This solution in combination with compressed air saves approximately 83 kW per hour during operation of the intaglio printing press. If all intaglio presses in operation were to use this system, the carbon footprint of banknote printing could be reduced by around 45,000 tonnes of carbon dioxide per year.
Banknote printing presses are as a rule equipped with conventional UV lamps for curing the inks during or at the end of the printing process. As an alternative to this, Koenig & Bauer offers UV-LED systems. This does away with the need for air extraction and lowers energy consumption by roughly 45% per press. In addition, UV LED lamps have a far longer service life, do not contain any mercury and do not give off any ozone. If all of Koenig & Bauer’s banknote customers were to use this new LED technology, carbon emissions could be reduced by around 10,000 tonnes a year.
Further innovative solutions in banknote printing permit greater resource efficiency through lower waste and a reduction of up to 25% in ink consumption on the intaglio printing presses. Ink consumption is optimised by aligning the paper to the length and position of the printing plate. The size of the stencil, which has a direct bearing on ink consumption, can be reduced significantly without impairing the print quality. If all intaglio banknote printing machines were equipped with this technology, around 2,500 tonnes of ink would be saved annually, while 5,000 tonnes of waste and the associated carbon emissions would be avoided. A current project is also making it possible to apply ink in the printing process only where it is needed. This reduces ink consumption by a further 25% to up to 50%.
Koenig & Bauer offers customers the VisuEnergy X management system to further improve energy and resource efficiency in their printing operations and throughout the entire company. As a trusted advisor in the field of sustainability, we provide customers with comprehensive support ranging from system and requirements analysis to energy consulting covering energy technology, efficiency and procurement strategies and their orientation as climate-neutral companies. This extends from the planning phase of a printing press investment to efficient production and greater economic viability. VisuEnergy X permits end-to-end digitalisation of the company, helps to record environmental data and supports an energy management system that has been certified under DIN EN ISO 50001:2018. Additional tools and services for reducing carbon emissions are also offered.
A further example of our active environmental policies is water-based and migration-harmless ink for food packaging. The food-safe water-based inks used by Koenig & Bauer Durst for digital printing meet the lifecycle-based environmental performance criteria set out in UL ECOLOGO Standard 2801 – 2012 (Standard for Sustainability for Printing Inks). UL ECOLOGO certification was achieved after the assessment of various criteria such as energy use, waste disposal and the reduction of toxic ingredients throughout the entire product lifecycle.
Koenig & Bauer provides its customers with the services of Climate-Partner for climate-neutral printing. With the frontprint manager on ClimatePartner’s online portal, it is possible to calculate in detail carbon emissions from printing and, at click of a button, to neutralise them by funding climate protection projects. Numerous certified climate protection projects meeting various internationally acknowledged standards such as Gold Standard, VCS and Social Carbon are available. The participating printing companies can utilise the “climate-neutral printing” label as a competitive differentiator.
Employee aspects
Companies are strengthened on a sustained basis by a committed, experienced, highly qualified, loyal and healthy workforce. With their ability to develop bespoke premium-quality high-tech printing presses and to provide comprehensive services, our employees generate sustained value for Koenig & Bauer. Against the backdrop of global trends such as demographic change and a significant increase in the need for successors to replace retiring employees in the coming years, as well as the digital transformation and greater worldwide networking, the current challenge is to find, recruit and retain the next generation of skill employees and people with broad and in-depth expertise in all aspects of old and new professions, especially since the activities in question call for a high degree of flexibility and willingness to travel in many cases. In addition to the further promotion of diversity, the main focus of our human resources activities in the year under review was placed on attracting the next generation of specialists and managers as well as on professional and personal development and motivating and retaining our employees. Particular attention was paid to expanding training capacities. To position our Company in the employment market, we use different forms of advertising, such as banners on Dresden trams, radio and nationwide poster advertising and participation in city festivals. With the Koenig & Bauer Academy and the Koenig & Bauer Campus learning management system, our employees can benefit from an extensive array of training opportunities and learn autonomously and flexibly in line with their needs. In the competition for talent, Koenig & Bauer comes to the fore as a globally active and innovative company with its pronounced orientation to values that are firmly entrenched in its corporate culture. A variety of measures, such as the early involvement of young management talent in projects and various training opportunities assist employees in unleashing their full potential. The Company suggestion scheme actively integrates employees in improvement processes on an ongoing basis. In the 2022 special campaign for the in-company suggestion scheme on sustainability matters, employees were invited to submit their suggestions for improving the energy efficiency of our products. Various prizes such as an e-bike were offered for the three best proposals in addition to the bonuses provided for in the company agreement.
The Group provides good working conditions for employees offering high standards of occupational health and safety. Koenig & Bauer takes care to offer equal opportunities to all employees. We want to additionally consolidate equal opportunities as the basis for personnel decisions in the Group. Respectful and responsible interaction with each other and the prevention of all forms of discrimination are an integral part of our corporate culture. We want to ensure discrimination-free workplaces for employees regardless of gender, age, disability, religion, origin or sexual orientation and promote inclusiveness. People with restricted mobility also have a place in Koenig & Bauer’s regular workforce. Similarly, employing people with special needs is a major priority for us. Some of the companies at the Würzburg and Radebeul sites significantly exceed the quota for employees with special needs stipulated in the German Social Code. At the foundry company, this quota stood at 9.3% at the end of 2022.
Attractive employer
Koenig & Bauer offers its employees modern working conditions including
flexitime and working time accounts as well as mobile working as far as
this is viable in the light of their duties. In principle, mobile workplaces are
set up for these groups of employees, allowing them to perform their work
outside the Company via mobile terminals. Mobile working offers advantages, especially for employees with children, helping them to achieve a
balance between the need to take care of ill children and their availability
to the Company. To additionally strengthen Koenig & Bauer’s profile as
an attractive employer, we are breaking new ground and implemented or
launched many measures in the year under review – from bicycle leasing
and season tickets for public transport to the further flexibilisation of
working hours, e.g. in the form of the new morning-tea break scheme for
part-time staff and new IT apprenticeships. In a survey, employees expressed great interest in bicycle-leasing.
Employees are assisted in finding a viable work-life balance by means of special offers such as flexible working hours, temporary or permanent part-time models, mobile working, childcare services and special leave, such as family leave and sabbaticals. The proportion of part-time employees in the Group widened to 4.5% (previous year: 3.8%). In a model project, we have created two extra part-time positions for women in production with a new morning-tea break arrangement, which will be expanded following its successful launch. Furthermore, Koenig & Bauer offers various child and holiday care services at its sites. During the summer holidays, the vacation programme available to the children of employees at the Würzburg site was again held over two weeks on two different farms. Thanks to the advantages they offer, these activities have also been included in the nationwide company childcare guide as a practical example of one of four organisational models and are thus setting an example across the country. The concept is to be offered at other Group locations in the future as well. At the Radebeul site, the availability of childcare during the summer holidays was announced at the beginning of February 2023. The children’s and youth day held in 2022 again at the Würzburg plant on the Day of Repentance and Prayer, which is a school holiday, was well attended after the previous year’s pandemic-induced cancellation. The existing day-care centre at the Radebeul site adjacent to the company premises is used by employees because the availability of care is aligned to their working hours. The provision of in-company childcare is being planned at the Würzburg site. Koenig & Bauer has been a member of the Family and Work Alliance in the Würzburg region since 2006.
Alongside a low fluctuation rate of 2% (previous year: 1%), the average length of service of 19.2 years (previous year: 20.2 years) and the large number of long-service anniversaries each year at our Radebeul and Würzburg sites testify to the high staff retention achieved at Koenig & Bauer. In 2022, 129 milestone career anniversaries (previous year: 92) were celebrated at the two main Group sites. 42 employees were able to look back on 40 years of service, while 85 had been with the Company for 25 years. At the anniversary celebrations, which took place again after the pandemic-related interruption, two employees were also honoured for 50 years of service. A summer party was organised for all employees at the Würzburg site and proved very popular. A family day with a comprehensive programme was held at the Radebeul site, attended by around 3,500 visitors.
Diversity
Koenig & Bauer attaches particular importance to the diversity of its workforce. Our diversity policy aims to encourage diversity in terms of gender,
internationality or ethnicity, age, religion and world view as well as in terms
of experience. In terms of internationality, we have already achieved a high degree of diversity through cross-site cooperation between employees of
different nationalities working at our numerous global locations. We want
to harness the potential arising from heterogeneous teams in the interests of sustained corporate development. As with many other mechanical
engineering companies, Koenig & Bauer has a relatively small proportion
of women (14.8%) employed in the Group compared with other sectors,
although there was an improvement over the previous year (13.7%). Various
activities are being initiated to widen the proportion of female employees, including appropriately worded job advertisements with job-sharing
possibilities, a “girls day”, career fairs, internships and school visits. In
addition to the general efforts to promote female representation at our
Company, such as the establishment of two part-time jobs for female
employees as described above, a diversity initiative has been launched
comprising a comprehensive package of measures such as special training
and female mentoring programmes to increase the proportion of female
employees in management positions. In a programme currently underway
with the Bavarian Metalworkers’ Association (bayme), we are encouraging
skilled female workers with development potential to take on management
tasks. At the end of 2022, female representation at the first and second
management levels below the Management Board at the holding company
Koenig & Bauer AG stood at 33.3% and 11.1%, respectively. These ratios had
been 25.0% and 12.5%, respectively, one year prior to this. The two major
Group locations have the following age structure: Of the 3,087 employees
in Radebeul and Würzburg, 24.2% are younger than 35 years, 50.1% aged
between 35 and 55 and 25.7% are over 55.
Recruitment of and professional training for the next generation of skilled workers
In-house training ensures Koenig & Bauer is able to meet its high demand
for qualified specialists in development, design, production, commissioning
and service. The dual vocational training model has a long tradition at the
Company. The Company’s own state-recognised vocational training centre
in Würzburg trains specialists by closely interlinking theory and practice.
In the 154th year of its existence, it continues to enable modern learning
and working. For this purpose, all trainees were provided with tablets. Via
an internal website, they can use the tablet to access interactive operating
instructions, e-learning, training documents, video tutorials and technical
drawings. All the information they need for their activities in the learning workshop is thus always just a few clicks away. By scanning the QR codes,
which are displayed on all machines, devices and containers in the vocational training centre, the trainees can view safety instructions and further
information on operation and handling directly on their tablet. The internal
website also offers instructional videos that the trainees have produced
themselves after receiving professional input from the trainers during German lessons.
In view of recent developments in the labour market, it is also becoming increasingly challenging for Koenig & Bauer to fill all apprenticeship positions – especially in the technical professions. Accordingly, we are recruiting the next generation of skilled workers from all types of schools and consciously give opportunities to those with lower grades. At career, vocational and job fairs as well as our own events such as the career information day in Radebeul and the information week with an open training day in Würzburg we are committed, with active support of our current apprentices, to interesting more people in the prospect of working at Koenig & Bauer. The vocational training department in Radebeul works with numerous schools in the region to inform them at an early stage of the training available at the plant. Community events at local schools provide information about training opportunities and professions at the Radebeul plant early on. At an information week including an open training day held in July 2022, more than 400 interested young people from schools in the region visited the vocational training centre in Würzburg to find out about training opportunities at Koenig & Bauer. Apart from these proven instruments, we are also relying on new methods, including the use of social media, to recruit junior staff. In this way, school-leavers can gain insight into what a traineeship with the Company entails together with the training syllabus and methods. In addition to the various opportunities for learning more about apprenticeships at Koenig & Bauer, work placements for school students offer a good basis for early career orientation for when they leave school. All internships are structured in such a way that the school students can try things out for themselves and acquaint themselves with the apprenticeship professions at the Company. A number of undergraduates are completing their theses at Koenig & Bauer or attending internships or practical semesters at Koenig & Bauer. In addition, the Company offers placements for undergraduates in almost all parts of the Group to acquaint them with the world of Koenig & Bauer printing presses.
As of 31 December 2022, the number of apprentices and interns stood at 331, up on the previous year’s figure of 315. The Group-wide apprenticeship ratio widened to 6% (2021: 5.8%). The apprenticeships range from mechatronics engineers to industrial mechanics and from machining mechanics to industrial business management assistants. In the IT sector, we train IT specialists for process and data analysis and, in 2022, expanded the range of apprenticeships to include electronics technicians for automation technology. From 2023, we will also be training technical product designers again. Trainees also include students enrolled in dual-studies courses, who are completing their practical phase at the Group sites in addition to attending university. Regular top rankings as top, second- or third-best performers and good to very good results in the final examinations testify to the acknowledged high quality of the Group-wide training centres. At the Dresden district Chamber of Industry and Commerce (IHK), an industrial mechanic from the Radebeul plant ranked the highest in his profession in the 2022 final examinations. A mechatronics technician from the Radebeul plant received an award as top performer in the additional English course offered by the Chamber of Industry and Commerce. The Radebeul vocational training department was given an honorary certificate from the Dresden Chamber of Industry and Commerce after previously receiving the title of “Excellent Training Company” for the 20th time. Upon successful completion of their apprenticeships, the future specialists face good career prospects with the possibility of permanent employment at the Group’s main sites in Würzburg and Radebeul.
Systematic personnel development
In the interests of the Group-wide advancement of employees, we have
installed a modular personnel development programme that defines target-oriented methods for various hierarchical levels and helps to identify
talents at an early stage and to promote them in a targeted manner. The
personnel development initiatives have a strong international focus and
incorporate all Group companies, including the global sales and service
companies. To additionally intensify Group-wide training and personnel
development activities, we established the global Group-wide Koenig &
Bauer Academy in the year under review. By pooling training activities at
the Group level and providing global, cross-BU personnel development
services, in addition to the promotion of a global leadership and learning
culture and the achievement of synergy effects, we are creating a digitalised, target group-oriented learning world that is available to all Koenig &
Bauer employees. An attractive training catalogue helps employees to plan
their individual career paths in conjunction with Koenig & Bauer. In addition
to all the locations worldwide, the virtual campus is also part of the Koenig
& Bauer Academy. Through the joint activities of all those involved in the
Academy network, we ensure that experts from all disciplines shape and
develop the range of training offered by the Koenig & Bauer Academy and
provide employees worldwide with new and important know-how. Information about the comprehensive range of training offered by the Academy is
included in a newsletter, the Academy magazine, its own website as well as
at events, training courses and in personal discussions.
The Koenig & Bauer Academy and the Koenig & Bauer Campus learning management system, which was rolled out a few years ago, provide the Group with an effective framework and modern tools for in-company training and development. All employees worldwide have access to the online catalogue via a personal profile, in which they can view all the training courses available to them. In addition to traditional face-to-face training on campus, the catalogue also includes live online sessions and e-learning by GoodHabitz in all relevant fields in order to encourage decentralised virtual learning. One example of live online training is the session known as “Conducting employee appraisal talks in a motivating way”. A proven personnel instrument, the annual appraisal interview is to be additionally reinforced through interactive training and individual attention to the requirements and questions of the participants. A positive aspect of this personnel instrument is the scope it offers for direct feedback in both directions, with employees and line managers able to jointly discuss their current views and goals. In addition to the comprehensive training catalogue for all employees, training is offered for managers on various topics such as leadership and employee motivation, team building and conflict management. Mandatory training on matters such as export control, compliance or occupational safety is allocated to employees directly in their individual training plans at the campus to ensure attendance. Each employee can apply for voluntary training courses from the online catalogue. Line managers can confirm the request for training directly in the system with a click of the mouse. The system documents each employee’s education history and issues reminders for upcoming training. As well as this, line managers are instructed to register employees for training measures. In addition to 522 face-to-face training sessions (2021: 876), 25,132 e-learning sessions, including the 169 GoodHabitz online courses, were held in the year under review. This is a significant increase over the previous year’s figure of 16,860 e-learning sessions. Compliance was a key topic covered by e-learning, with 11,248 online sessions held (2021: 7,541). Moreover, there is a large number of technical and other training and further education courses as well as specialised training, such as for forklift driving licences, first aid etc. On top of this, we support the in-service further training of our employees, allowing them to qualify as technicians, specialists and business economists, and, if desired, also offer them master training.
Another component of our human resources development activities entails development assessments, in which management and junior staff are evaluated externally. This is followed by an internal process in which the immediate line managers draw up competence profiles on the basis of the results gained. In an ensuing step, the managing directors and department heads evaluate the executives and junior staff from their business units in calibration workshops to gain a more differentiated view. A comprehensive competence matrix is available in a database for the group undergoing assessment. Within this group, high potentials are identified in the subsequent coordination rounds for each business unit attended by members of the Management Board and executive staff on the basis of criteria such as age, language skills, international profile, leadership capabilities, expertise (technical/commercial skills), career background, mobility/willingness to change and skills/potential. Thereupon, individual development plans with further training measures are drawn up. The goal is to fill management positions from the Company’s own ranks. We want to strengthen our appeal as an employer by means of this systematic career development. Moreover, systematic talent management addresses the expectations of career-oriented high performers and thus also helps the Company to retain qualified employees.
In addition, the one-year junior management programme (JuMP) with participants aged between the early 20s and 30s aims to systematically prepare junior staff for management tasks. 22 young professionals participated in the programme, which was launched in 2021. In addition to the technical learning modules, junior managers work on practical projects from everyday business life. This encourages international networking and allows them to develop innovative problem-solving approaches for business challenges.
A further indication of the strong employee involvement is the “Campus of Experts” training series, which consistently addresses topics of current interest. Another component of the human resources development portfolio is consulting services for organisational development at the team, departmental and divisional level including corresponding workshops. In addition, professional and personal coaching is available for all target groups in the Company. New employees complete the digital onboarding process, which helps them to find their way around the Company and familiarises them with the corporate culture. Professional provider management for purchasing and coordination as well as quality assurance for external service providers such as trainers and coaches is a further aspect of human resources development.
Health and safety
The health and safety standards at the production plants in Würzburg, Radebeul and Dobruška are certified in accordance with DIN ISO
45001:2018. Various measures are being taken to achieve further improvements in safety and ergonomics. Regular checks and consultations are held
to monitor compliance with health and safety regulations and to make recommendations for optimising work processes. By avoiding non-ergonomic
movements and heavy lifting, it is possible to minimise illness and accidents. The hazard assessments are updated regularly. Regular instruction
and training seek to raise employees’ awareness of any hazards that may
arise. In addition to the detailed personal instructions given to the apprentices at the vocational school by the instructors, they can download safety
instructions for the operation and handling of all machines, equipment and
containers directly onto their tablet by scanning the QR code displayed.
This assistance contributes to the achievement of our strategic ESG target
of minimising occupational accidents.
15.7 accidents per 1m hours worked (previous year: 15) with lost working time of one day or more for the core workforce were registered in the year under review at workplaces in the Würzburg and Radebeul plants. Extensive analyses of these incidents are performed as a basis for defining preventive measures for reducing workplace accidents. At the same time, the monthly report on accident frequency rates by business unit and department facilitates the development of targeted responses. Potential hazards are addressed and highlighted in special monthly campaigns.
Workplace health promotion and prevention as well as comprehensive health management also enjoy high priority at Koenig & Bauer. The various programmes are managed and implemented by human resources management and by the Koenig & Bauer in-company health insurance fund (Koenig & Bauer BKK), which is organised as an autonomous public-law entity. In a personal letter, human resources management at various business units offers employees who have been on sick leave for more than 30 days in the past year the opportunity of attending a confidential meeting to discuss possible measures to overcome or prevent incapacity for work and to maintain workplace performance. A health team was established at the Radebeul site under the motto “Promoting health together”. Top priority is being given to workplace ergonomics and the prevention of musculoskeletal disorders as well as regeneration management. The building blocks for achieving this include improvements to conditions in recreation rooms and spaces as well as the installation of additional outdoor seating. Further health teams are to be established step by step throughout the Group.
In addition to the diverse activities and offers including health courses, special health days and vaccinations, counselling and training are another focus with which health skills are taught, while employees are encouraged to work in a health-conscious and ergonomic manner and to prevent stress. As in earlier years, courses were held for the apprentices under a health promotion programme tailored to their needs to raise awareness of such concerns as hearing loss caused by high noise levels, addiction prevention and the avoidance of muscle/skeletal diseases. In addition, Koenig & Bauer BKK launched the analogue/digital You!Mind service, which aims to strengthen the mental health of trainees and teachers. The active weeks in selected health resorts are a special type of preventive health promotion with individual programmes to maintain or restore performance and well-being. Skin screening was personally offered on site at the Frankenthal, Radebeul and Würzburg plants in the year under review. Regardless of where they live, employees suffering from mental illnesses receive a qualified initial diagnosis within 14 days through the in-company health insurance fund’s ProPsych programme. If the initial diagnosis indicates the need for a medical response, the employee concerned receives psychotherapeutic treatment within a further 14 days. Special behavioural therapy for sustainable weight loss in the event of obesity is also offered under this programme. The aim of the “BGM-innovativ” programme held at the Würzburg and Radebeul sites is to provide coordinated care for at-risk and ill employees suffering from musculoskeletal disorders in order to avert illness or to prevent it from becoming chronic, to shorten the duration of the illness and absences and to maintain working capacity permanently. In response to an employee survey, a full-body training programme featuring CrossFit and high intensity interval training was launched for the first time in November 2022. The Koenig & Bauer BKK programme also includes yoga classes, which take place in hybrid form, i.e. both face-to-face at the plant and online. For tinnitus patients, the Tinnitracks app is available to mitigate the intensity of the whistling sound in their ears. The new health and fitness app provides members of the Koenig & Bauer health insurance fund with useful tips on healthy eating, living more consciously and moving correctly and effectively. This year’s “apple campaign” held at the canteens in Würzburg and Radebeul proved very popular. Good health and team spirit are encouraged by means of company sports festivals and by inviting employees to participate in company runs.
Social aspects
Koenig & Bauer is a pioneer in employee welfare as well as a supporter of social projects. Even before social security was introduced in Germany, the Company had already established the predecessor of an in-company health insurance fund in 1855. Founded in 1873, the fund for disability, widow and orphan benefits continues to exist to this very day. We are committed to our responsibility to society and sponsor social and cultural projects along- side initiatives for preserving and protecting the environment.
Social commitment
At Koenig & Bauer, social and community involvement includes comprehensive sponsoring and donation activities. The Group sponsoring and
donations policy governs its basic approach to these matters and defines
a consistent process throughout the Group, including approval rules. On
the Koenig & Bauer sustainability website, a new section is to be added to
list the current sponsorship and donation activities and to provide a central
point of contact at the e-mail address engagement(at)koenig-bauer.com
for all requests relating to sponsorship and donations.
In addition to the annual support for the Africa Festival in Würzburg, Koenig & Bauer provides financial resources all over the world for social projects and the activities of charitable and non-profit organisations and institutions such as foundations or associations. In the year under review, donations were made to “Liebe im Karton”, the Nicolaidis Young Wings Foundation, refugees from Ukraine and the Homburg am Main Summer Academy. Apart from this support for social institutions and cultural initiatives, a special focus was placed on ecology in 2022. Koenig & Bauer is supporting a rainforest project in Ghana as part of the Baobab Project. The preservation of the rainforest benefits the agricultural training project of the Baobab Children Foundation, which is also being sponsored, via a more stable local climate, serving as a mosaic stone in global climate action. The aim of the Baobab Children Foundation is to enable young people between the ages of 13 and 18 years to complete vocational training by sitting for a state examination after four years of schooling and one practical year. In addition, Koenig & Bauer is supporting the Bakita Girls Community Centre in Tanzania, which is based on a micro- and macro-sustainability model and provides school education for young mothers and orphans in particular by providing additional vocational training resources. Koenig & Bauer MetalPrint organises an annual fundraising campaign in the form of an employee raffle, with the proceeds going to a children’s and young people’s hospice in Stuttgart, with the Company doubling the amount donated.
It is also providing funding for the sustainability programme initiated by Banco de la Republica in Colombia, which aims to issue only banknotes with zero carbon emissions. The banknote printing plant’s emission neutrality is to be achieved through the BioBanknote reforestation project, in which trees are planted in selected regions of Colombia.
In a festive event held during an Executive Summit on 30 September in Würzburg, Koenig & Bauer presented for the first time the Green Dot Award 2022, which was specially created by the Company. In this way, Koenig & Bauer wants to honour a visionary leader with outstanding ideas who has made innovative contributions to sustainable printing in a special way. The Green Dot Award winner received prize money of 10,000 euros. Koenig & Bauer donated a further 10,000 euros for a sustainability project selected by the award winner’s. The Green Dot Award 2022 winner selected the Estonian initiative “Let’s Do It World”, which organises a variety of actions for a waste-free world such as the World Cleanup Day. “Let’s Do It World” is an accredited member of the United Nations Environment Programme and received an award from UN Habitat in 2021 for holding consecutive World Cleanup Days. The donation is to be used to organise the next World Cleanup Day on 16 September 2023. Sponsored by Koenig & Bauer, the Print & Media Award for the environmentally oriented company of the year also recognises printing companies’ ecological commitment.
With their extensive voluntary activities at the Chambers of Industry and Commerce and the Chambers of Crafts, as honorary judges at the labour and social courts, in emergency-assistance organisations such as the Federal Agency for Technical Relief, the fire brigade and the rescue service, as well as in city and municipal councils, the executives and employees make a great contribution to the community. In many cases, employees are given time off to engage in the wide range of voluntary activities undertaken by Koenig & Bauer. Earth Day is celebrated each year on 22 April and aims to strengthen appreciation for the environment and encourage people to rethink their consumer behaviour. Over 175 countries participate with various events and activities. Under the TICCIT (Trees Into Cartons, Cartons Into Trees) initiative, executives from the US subsidiary visited the German International School in Dallas in spring 2022 to arouse students’ interest in a more sustainable future and the importance of recycling.
As a globally active printing press manufacturer, Koenig & Bauer has always stood for cosmopolitanism and tolerance. At its Radebeul site it supports the “Wirtschaft für ein weltoffenes Sachsen” association (Business for a Cosmopolitan Saxony) by taking specific measures to assist and promote the integration of newcomers and immigrants in the local economy. After successfully completing secondary school, two refugees are completing a four-year vocational training programme in the dual-qualification programme “Mechatronics Technician with Abitur”. They are completing the practical part at Koenig & Bauer in Radebeul. For the theoretical part of their training, they are attending the vocational training centre for electrical engineering in Dresden. Two refugees began their vocational training at Koenig & Bauer back in 2015. They have successfully completed their apprenticeships as mechatronics engineers and have since been working in the assembly area for sheetfed offset presses. To arouse our employees’ interest in world affairs, we invited Niklas Frank, a contemporary witness from the National Socialist era, to our vocational school at the beginning of January 2023 to read to trainees, trainers and employees. This was followed by lively discussion. In his books, the son of a National Socialist ruler settles describes his father’s deeds.
High product quality for greater on-site and process safety
in printing operations
Koenig & Bauer attaches great importance to the quality of its products
and services. Reflecting this, the quality management system aims at
achieving ongoing compliance with the highest quality standards in the
production and assembly of the Company’s bespoke, innovative and complex products. The quality management systems at the major production
plants in Radebeul and Würzburg, at the Sheetfed business unit in Radebeul, at the Security business unit at the three sites in Würzburg, Lausanne
and Mödling and at the Coding business unit in Veitshöchheim are certified
in accordance with DIN EN ISO 9001:2015. Product development focuses
on work and process safety, reliability and user-friendliness.
Commitment to human rights
In its role as an employer as well as a supplier and buyer of products and services, Koenig & Bauer is committed to protecting human rights and views this as a core element of responsible corporate governance. One of the guiding principles of our corporate policy is the United Nations Framework on Business and Human Rights (“protect, respect and remedy”). With the incorporation of a duty to observe human rights in the terms and conditions of purchase and the systematic observance of these requirements in all material business activities, the Company makes sure that its business partners acknowledge and respect human rights in the same way that it does. By signing the purchasing conditions, suppliers particularly undertake to refrain from using child labour and forced labour and to avoid all forms of discrimination. The purchasing conditions impose on external business partners a duty to respect employee rights and to observe labour law. The code of conduct for suppliers included in the terms and conditions of purchase also stipulates the observance of statutory and contractual quality and safety standards as well as environmental requirements particularly in connection with the use and processing of hazardous substances. In addition to the standard contracts used as framework and purchasing agreements and the purchasing conditions including the Code of Conduct for Suppliers, there are quality assurance agreements in force with around 400 suppliers.
In particular, the Code of Conduct imposes on suppliers the duty to provide information on request on their compliance with human rights, the ban on child labour, minimum wages, business integrity, health and safety and sustainability, and to allow audits to be carried out. We have installed comprehensive processes to verify our suppliers’ compliance with the required principles initially and on an ongoing basis. A supplier qualification process must be completed whenever a supplier relationship is approved for the first time or re-established. This initial screening of potential suppliers during the selection process includes at least one self-assessment in the form of a questionnaire, in which they must also provide information on their practices for ensuring compliance with human rights and environmental standards at their companies (supplier qualification). Further measures are initiated on the basis of the results of the self-assessment and an internal risk assessment. These can include a request for certificates, evidence of the avoidance of human rights risks or environmental risks, audit procedures or an on-site audit. As part of the ongoing review of the partnership in the form of supplier audits, a random sample is taken from existing suppliers.
The Code of Business Conduct, which was rolled out in 2011 with binding effect throughout the Group, includes the relevant aspects of the law on corporate due diligence to prevent human rights violations in supply chains. These include fair competition by preventing corruption, fraud and cartels, occupational safety and health, environmental protection and equal treatment and anti-discrimination. Adherence to these principles is ensured by the compliance management system in the form of guidelines, processes, controls, training, standard contracts and other monitoring activities. Under a holistic approach, the measures directed at suppliers are backed by a sustainable and risk-averse purchasing strategy on the part of Koenig & Bauer, with priority given to sourcing from the German-speaking area. We believe that we had already created the legal and organisational foundations before the enactment of the Supply Chain Due Diligence Act to pass on, detect and enforce the requirements of the law along the supply chain.
Even though the legal obligations under the Supply Chain Due Diligence Act to prevent human rights violations in supply chains will not come into force until 2023 for Koenig & Bauer, the model for analysing and addressing corresponding risks was already developed in 2022 and a corresponding risk analysis carried out on a trial basis. The process for the annual risk analysis required under section 5 of the Supply Chain Due Diligence Act has been formalised. Central Purchasing, which is responsible for all procurement activities within the Group and is based at the holding company, evaluates the data on all suppliers once a year together with the Compliance and Corporate Responsibility departments. The first step is to identify the countries from which Koenig & Bauer sources goods or services directly. For each direct source country, a risk score is calculated on the basis of the legal interests to be protected in accordance with section 2 of the Supply Chain Due Diligence Act according to twelve publicly accessible indices published by NGOs. To achieve a systematic scaling of the country-specific risk potential, a risk score of between one and three is assigned to each country for all of the twelve indices in relation to the legal interests to be protected. A risk score of one indicates a low country risk, two a medium country risk and three a high country risk. If no index-specific score is available for a given country, a risk score of three is generally applied as the basis for further calculation. Once all country risks have been determined, an international risk score is calculated. All suppliers from critical countries whose risk score is up to 25% above the average international score undergo a separate audit. The risk analysis also includes information from employees and third parties on potential violations, dangers or grievances, the failure of business partners to comply with human rights and environmental protection requirements, which can also be reported anonymously via the whistleblower system. On the basis of the comprehensive risk assessment, a committee consisting of representatives from Central Purchasing, Corporate Responsibility, Compliance, Quality Management and the Human Rights Officer meets at least once a year – or on an ad hoc basis if any information is received – to analyse the results of the risk assessment and to define a plan of action with a sequence of audits for high-risk suppliers. Depending on the risks identified, the risk mitigation plan may include a self-assessment, a qualified self-assessment with internationally recognised documentary evidence or certificates, an on-site audit or an ad-hoc audit in response to a report received. Furthermore, the inspection committee determines the date by which the suppliers that are classified as problematic must be audited. Measures to reduce or eliminate identified risks may include further awareness-raising activities and a declaration of undertaking by suppliers to respect human rights and the environment, closer monitoring of suppliers, agreement with suppliers on concrete action plans to reduce risks and, in cases in which there is a persistent risk to the protected interests, a reduction in or the discontinuation of the relationship with the supplier in question. The Management Board appointed a Human Rights Officer at its meeting on 20 December 2022. The policy statement on implementing the requirements of the Supply Chain Due Diligence Act for preventing human rights violations in supply chains has been published on the Company’s website.
Anti-corruption and anti-bribery
Responsible and transparent corporate governance oriented to long-term value creation has high priority at Koenig & Bauer. Integrity and compliance with the law form the basis of global social and economic life and are therefore indispensable in avoiding detrimental economic, ecological and social impacts. Furthermore, they are the prerequisite for meeting the goals of our sustainability strategy, e.g. the protection of the environment and human rights as well as equal opportunities, together with the constantly growing expectations of our customers, investors and employees in this regard. For these reasons, we consider integrity and compliance with the law to be indispensable in business transactions and pursue a zero tolerance approach in this respect.
The Group-wide compliance management system (CMS) creates the basis for ensuring that business practices satisfy the highest compliance and integrity standards. The contents and activities of the compliance organisation are reviewed on the basis of a compliance plan adopted in consultation with the Management Board and the Supervisory Board’s Audit Committee at the beginning of each year. The compliance plan also defines measurable objectives (KPIs) of the CMS. The following KPIs are currently defined:
- Ratio of compliance training completed at the Koenig & Bauer Campus
- Ratio of compliance on-boarding for new employees as part of the Welcome Days
- Number of compliance reviews conducted at Koenig & Bauer subsidiaries
- Percentage acceptance of the Koenig & Bauer Business Principles by relevant suppliers
- Ratio of compliance undertakings signed by relevant employees
Decisions on the modification of KPIs or the inclusion of additional ones are made during annual compliance planning.
The CMS is designed to prevent violations of laws, standards or internal policies. A regular compliance risk analysis forms the basis for the organisation and processes. More detailed stakeholder and risk analyses are carried out to intensify the analysis of special risks, such as corruption prevention and money laundering. In addition to monitoring changes in the law and reported compliance risks, one component of the risk assessment entails the continuous sharing of information on the internal processes of the Koenig & Bauer Group companies. For this purpose, a compliance team has been set up and is composed of representatives from information technology, human resources, accounting, taxes, data protection as well as the local compliance officers. In 2021, all subsidiaries additionally submitted for the first time a standardised report on their compliance situation as part of the fixed agenda of the meetings of the relevant supervisory bodies (e.g. boards, shareholder assemblies, supervisory boards, governance bodies). Comprehensive guidelines have been issued and the necessary processes established on the basis of the results of the risk analysis to ensure compliance and integrity in all business activities. Any changes that are identified in the risk situation or requirements are addressed by duly modifying the internal guidelines. The corporate compliance manual issued across the entire Group combines our business code of conduct, compliance rules and the main Group policies in a single document. The latest version of the policies can be viewed in the policies portal on the Koenig & Bauer intranet.
The CMS attaches great importance to combating corruption and bribery. For this reason, the process for ISO 37001 anti-corruption management certification was initiated in 2022. The corresponding certification audit was completed in December 2022, with the ISO 37001 certificate issued at the end of January 2023. This also reflects Koenig & Bauer’s broad-based commitment to promoting fair competition.
The comprehensive compliance and integrity standards can only be fully effective if employees are aware of them and adhere to them. For this purpose, 13 online training sessions on the main aspects of compliance and the code of conduct are currently available throughout the Group. Available in several languages, they are mandatory for every new employee. The use of an IT process with the Koenig & Bauer Campus training management system, which is based on SuccessFactors, automatically ensures that training is held in cycles determined by risk criteria applicable to the employee’s specific position. Compliance with this requirement is monitored through regular reminders and escalation processes. Following the initial allocation of online training via the Koenig & Bauer Campus at the end of 2017, over 30,000 compliance training courses were completed by the end of 2022, including over 17,000 that were directly related to anti-corruption. The Koenig & Bauer Campus has since been rolled out across all 50 relevant subsidiaries, meaning that almost all employees in Europe, Asia, North and South America can attend compliance training via the Koenig & Bauer Campus.
The preventive CMS measures are complemented by a regular review of their effectiveness to identify potential for improvement. In addition to tracking the agreed KPIs for the CMS, internal and external compliance assessments in particular are carried out periodically at Koenig & Bauer AG and its subsidiaries for this purpose. The internal whistleblower system, which had been in place since 2017, was replaced in 2022 by a new online platform that will continue to ensure that potential compliance violations can be reported anonymously by employees and – in contrast to the previous system – additionally also by third parties. The whistleblowing system also includes a case management function, thereby ensuring full documentation of the actions taken to follow up on the tips received. As well as this, it contains a feedback channel to the whistleblower notifying him or her of the receipt of the report and the status and outcome of the inquiries. Moreover, the system allows for requests for further information or evidence to be made even if the whistleblower wishes to remain anonymous. Under the Group policy, all suspicions are followed up consistently and, if necessary, disciplinary or legal action taken. This applies equally to reports by the media or authorities of potential violations by Koenig & Bauer companies. In such cases, cooperation is sought to clarify the circumstances. Koenig & Bauer complies in full with any notification or cooperation duties.
Koenig & Bauer is also committed to fighting corruption and encouraging compliance beyond its own business activities. Since its foundation in 2013, the Banknote Ethics Initiative (BnEI) has established a strict code to prevent and combat corruption and anti-trust violations in the field of banknote printing and trading. The principles espoused are not only recognised among the members of the BnEI but are also adopted by a significant proportion of central banks and banknote printers worldwide and form part of their procurement processes. As a founding member of the BnEI, Koenig & Bauer Banknote Solutions has agreed to be bound by strict rules of conduct and transparency, compliance with which is verified under the accreditation to be renewed every three years on the basis of an audit programme developed by the BnEI. After the successful renewal of accreditation in 2020, the next audit is already planned for 2023.
The promotion of ethical behaviour, transparency and compliance forms the focus of our activities, particularly in the security and banknote printing industry. With the KBA-NotaSys Integrity Fund, which was founded in 2017, Koenig & Bauer finances international projects to enhance compliance processes and culture. By the end of 2022 a total of 42 projects initiated by universities, associations and institutions in Europe, South America and Africa had been funded. The project initiators include Transparency International, the German Institute for Compliance (DICO), the German Institute for Efficiency Testing (DIEP) and various Swiss and German universities. The results of the projects were published and presented to interested groups and also discussed at two meetings of the project managers organised by the Fund in 2020 and 2022. Total funding of 5 million euros was allocated. The Integrity Fund was formally closed on 31 December 2022. However, projects that have already been awarded will continue to run until the contractually agreed deadline of 2024 at the latest. Funds flowing back from projects that have not been fully completed can still be allocated to new projects in 2023.
Further details of the compliance management system can be found in the compliance section of Koenig & Bauer’s website.
The ongoing analysis of possible compliance risks is a decisive prerequisite for the Company’s ability to continue meeting the high standards of rule-compliant business conduct and integrity in the future. The analyses conducted in the individual business units in 2022 did not reveal any new compliance risks. One whistleblower report was received and addressed by taking appropriate measures, thus highlighting the functionality of the compliance management system.
Disclosures on the EU taxonomy
The EU Taxonomy Regulation is an integral part of the European Commission’s Action Plan on the Allocation of Capital Flows to Sustainable Economic Activities. As a classification system for environmentally sustainable economic activities, the EU taxonomy rules mark a significant step towards achieving the EU objective of climate neutrality by 2050. The taxonomy focuses on six objectives: climate change mitigation, climate change adaptation, sustainable use and protection of water and marine resources, transition to a circular economy, pollution prevention and control and protection and restoration of biodiversity and ecosystems.
The following information is based on Taxonomy Regulation (EU) 2020/852, which was published in July 2020. Furthermore, we have taken into account the delegated act on the first two environmental objectives, climate change mitigation and adaptation (Commission Delegated Regulation (EU) 2021 /2139 of 4 June 2021 on the technical assessment criteria under Articles 10 and 11 of the Taxonomy Regulation) and the delegated act on the reporting requirements under Article 8 of the Taxonomy Regulation (Commission Delegated Regulation (EU) 2021 /2178 of 6 July 2021), as well as various explanatory documents and FAQs on the implementation of the taxonomy reporting requirements. In accordance with these regulations, the proportion of taxonomy-eligible and non-taxonomy-eligible as well as taxonomy-aligned and non-taxonomy-aligned economic activities in 2022 in total revenue and capital and operating expenditures is disclosed. Since the analysis carried out did not identify any economic activity that makes a substantial contribution to the second EU environmental objective of climate change adaptation, the identification of potentially taxonomy-eligible activities is oriented to the first EU environmental objective of climate change mitigation. The details relevant for this disclosure in the non-financial Group report 2022 are published in section 1.2 of Annex I of the delegated act on reporting requirements under Article 8 of the Taxonomy Regulation. In order to avoid any duplication, taxonomy-eligible activities are disclosed only where the activity in question has not been included in another category.
Taxonomy-eligible revenue
In identifying potentially taxonomy-eligible activities, we first classified
our economic activities according to the NACE codes. As Koenig & Bauer’s business activities match NACE codes 28.29 and 28.99, we followed
the requirements of the category “3.6. Manufacture of other low carbon
technologies” in identifying potentially taxonomy-eligible revenue. With
regard to this environmental objective of climate change mitigation, we
have classified revenue derived from products or product groups as taxonomy-eligible if the printing presses and systems also aim to significantly
reduce carbon emissions for our customers in the printing and postprinting
industry on the basis of the technology used. Under environmental concerns in the chapter entitled “Ecological printing technology”, we present
in detail the technologies or printing presses developed to reduce carbon
emissions in the printing process. These include VariDryBlue drying and the
new dryer for the AirTronic delivery for sheetfed offset presses, the HighEcon and EcoTNV dryers for metal decorating presses and the PowerSave
unit, LED technology for curing inks in the press and targeted adjustment
of the stencil size for banknote presses. We then aggregated the revenue
determined in the accounting departments of the Group or the respective
business units for each product or product group classified as taxonomy-
eligible. In 2022, revenues of €366.4m were generated with banknote printing presses, with sheetfed offset presses fitted with the VariDryBlue drying
technology and with metal printing presses and components delivery with
TNV technology. Our consolidated net revenue of €1,185.7m is presented
in the consolidated financial statements on page 55 of the annual report
2022 in the line denoted “Revenue”. Further details of our accounting policies for calculating Group revenue can be found on page 69 f of our annual
report 2022.
Substantial contribution to climate change mitigation as a prerequisite
for taxonomy alignment
To identify taxonomy-aligned revenue, we first analysed the technologies
classified as taxonomy-eligible, or the corresponding products and product
groups, to determine whether they contribute to a significant saving of
greenhouse gas emissions during use of the product over the entire lifecycle of the press compared to the best-performing reference technology
available on the market. For this purpose, we systematically applied the
corresponding EU rules on Category 3.6 “Manufacture of other low-carbon technologies” with a focus on reducing greenhouse gas emissions in
the user industries and internationally accepted calculation standards. The
Greenhouse Gas Protocol was used as a basis for calculations as the internationally acknowledged standard is similar to the ISO Norm 14064-1:2018 required by the EU taxonomy. On the basis of the Greenhouse Gas Protocol
Standard, we calculated the carbon emissions of the Koenig & Bauer press
and reference product during the utilisation phase on our customers’ premises, applying the average total life of the products as a basis for this. The
energy measurements for our own products correspond to those underlying the Scope 3 carbon emissions calculated under the category “Product
use” (3.11). The lifecycle greenhouse gas calculations for the most efficient
alternative technology available on the market were based on requests for
tenders published on the internet with energy values confirmed by the sole
competitor in this printing press class. On the basis of these valid energy
consumption measurements, we were able to calculate the greenhouse gas
emissions of our printing press and those of our competitor and demonstrated savings of roughly 2% using the Koenig & Bauer technology. In
the special machinery business, we measured a roughly 2% higher energy
efficiency in the banknote printing presses compared with the competing
product and therefore consider this to be significant as efficiency improvements by means of product developments and enhancements are possible
only in small steps due to the nature of the technology. The internal carbon
emission calculations over the entire lifecycle were validated by an external
climate footprint expert.
No significant impairment of other environmental objectives as a
prerequisite for taxonomy alignment
In the course of the analysis, we subsequently determined whether the
achievement of the five other EU environmental objectives is significantly
impaired by Koenig & Bauer’s business activities (“Do no significant harm”
– DNSH). With regard to the EU environmental objective of climate change
adaptation, we did not identify any material impairment of the relevant
locations on the basis of climate scenario and vulnerability analyses. These
analyses were performed in 2022 on the basis of data from the Intergovernmental Panel on Climate Change (IPCC) available at the time of the
report. These analyses are based on the shared socioeconomic pathway
scenarios (SSP scenarios) SSP5-85 and encompass medium and long-term
threats to the climate. With respect to the third EU environmental objective “Sustainable use and protection of water and marine resources”, we
conducted a preliminary review ahead of an environmental impact assessment at our site in Würzburg which covers the requirements to water. The
long service life of our presses and systems, the services offered, such
as upgrades to extend their service life, their recyclability and the use of secondary materials in the production of core components all help to
meet the EU’s environmental objective of transition to a circular economy.
The criteria for the EU environmental objective “Pollution prevention and
control” primarily relate to legal and regulatory requirements, which we
are obliged to comply with. Compliance within the scope of our business
activities is monitored and ensured through various policies and measures.
Currently, we have no knowledge that our business activities contribute to
the production, marketing or use of substances classified as hazardous.
With regard to the EU environmental objective “Protection and restoration
of biodiversity and ecosystems”, we carry out environmental impact assessments or comparable assessments as part of our business activities, where
required. Our business activities are not located in or near biodiversity-sensitive areas. As a result, we have not identified any significant impairment
by Koenig & Bauer’s business activities of the achievement of the five other
EU environmental objectives.
Compliance with minimum protection as a prerequisite for
taxonomy alignment
With regard to companies’ compliance with minimum protection requirements, the EU Taxonomy Regulation calls for the OECD Guidelines, the
United Nations Guiding Principles, the International Human Rights Charta
and the ILO Core Labour Standards to be followed. In our business activities, we have verified compliance with these principles and standards with
regard to human and labour rights (including health and safety at work,
freedom of association, prohibition of child labour) and combating bribery
and corruption. In addition, fair competition and taxes are also considered.
We have come to the conclusion that the minimum protection required by
the EU Taxonomy Regulation is complied with throughout the Group. The
framework conditions and systems established throughout the Group along
the entire value chain, the applicable instructions and guidelines as well as
the whistleblowing system and various systems such as employee representation, ensure that minimum protection is assured and violations are
prevented, and that any violations that, contrary to expectations, do occur
can be identified and countermeasures initiated quickly.
Taxonomy-aligned revenue
Having determined the absence of any material impact on the achievement
of EU environmental objectives two to six (DNSH) and compliance with the minimum required protection in our business, we have classified as taxonomy-aligned those taxonomy-eligible activities and the revenue they produced
for which we have been able to demonstrate a substantial contribution to climate change mitigation through substantial savings in lifecycle greenhouse
gas emissions during the product-utilisation phase compared to the best
performing alternative technology available in the market through publicly
available energy data on the competing printing press. We report taxonomy-aligned revenue of €150.7m for 2022 from activities with banknote printing presses, equivalent to 12.7% of the Group revenue of €1,185.7m in 2022.
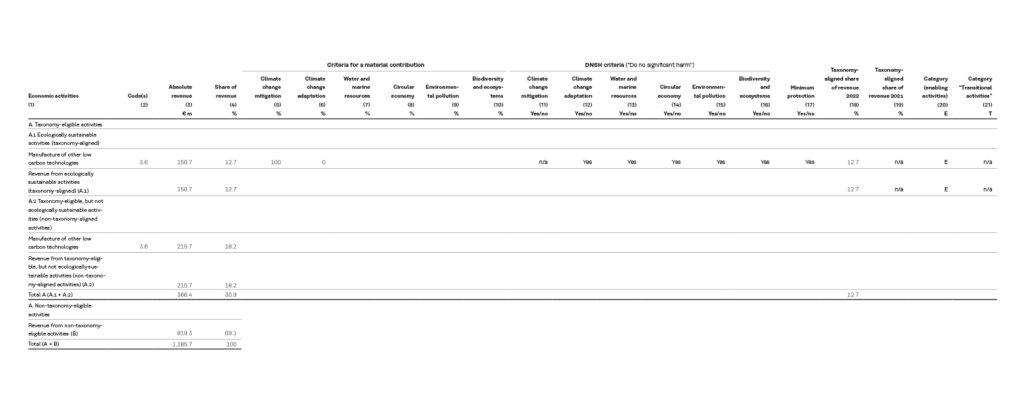
Image: Share of revenue from goods or services related to taxonomy-aligned economic activities
Taxonomy-eligible operating expenditure
Operating expenditure in the sense of the EU taxonomy includes non-capitalisable expenses, including for research and development, building refurbishment measures, short-term leases, maintenance and servicing. Non-capitalised R&D expenses, maintenance and servicing costs in production, sales
and administration as well as expenses for short-term and low-value leases
determined by Group accounting are used as the denominator to identify the proportion of taxonomy-eligible operating expenses. The consolidated
income statement on page 55 of the annual report 2022 includes the R&D
expenses that are not recognised on the balance sheet and the other cost
items included in production, selling and administrative expenses. The expenses incurred for measures for reducing energy consumption or increasing
energy efficiency at the factory buildings form a partial value in the numerator for identifying the taxonomy-eligible proportion of operating expenditure. These expenses, which essentially fall under category 7.3 “Installation,
maintenance and repair of energy efficiency equipment”, are classified as
taxonomy-eligible operating expenses in accordance with section 1.1.3.2.(c) of Annex I of the Delegated Act on Article 8 of the EU Taxonomy Regulation.
As the remainder of the total operating expenditure for taxonomy-eligible or
non-taxonomy-eligible economic activities arises at the Group locations and
a more accurate breakdown is not possible for system-related reasons, this
difference is disaggregated on the basis of the percentage of taxonomy-eligible revenue in the entire product portfolio in order to determine the taxonomy-eligible category A operating expenses. The sum total of the taxonomy-eligible category A and category C operating expenditure is used as the
numerator for calculating the taxonomy-eligible share of operating expenses
as no category B operating expenses arose in the year under review.
Taxonomy-aligned operating expenditure
It was not possible to report on taxonomy-aligned operating expenditure
coming within category 7.3 “Installation, maintenance and repair of energy
efficient equipment” during the year under review, as no DNSH evidence was
available for the individual types of taxonomy-aligned operating expenditure.
In the case of economic activities under category 3.6 “Manufacture of other
low-CO2 technologies”, it was possible to report on taxonomy-aligned operating expenditure as a result of the application of a revenue-based allocation
key. On balance, the total taxonomy-aligned operating expenditure coming
within category 3.6 amounted to €8.4m in 2022, equivalent to 12.6% of the
total operating expenditure of €66.5m in the year under review.
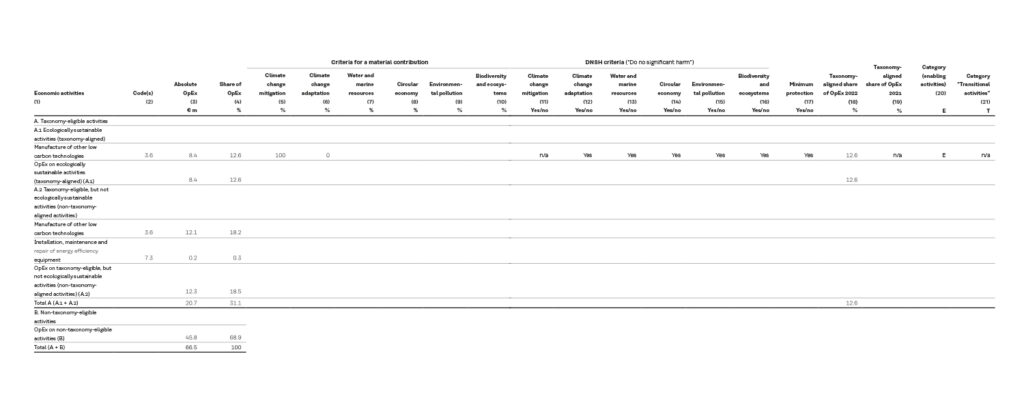
Image: Share of operating expenditure (“OpEx”) from goods or services related to taxonomy-aligned economic activities
Taxonomy-eligible capital expenditure
In order to identify the taxonomy-eligible proportion of capital expenditure, the investments determined by Group accounting in accordance with
IFRS are placed in the denominator. This amount can be derived from the
additions column in the consolidated statement of changes in assets on
page 72 of the Annual Report 2022. It includes additions to property, plant
and equipment and intangible assets during the year before depreciation
and remeasurements, including those resulting from remeasurements and
impairments for the 2022 financial year and excluding changes in fair value.
Apart from additions to non-current assets (IAS 16) and intangible assets (IAS 38), additions to right-of-use assets (IFRS 16) are also included. The
first partial value of the numerator for determining the taxonomy-eligible
share of capital expenditure includes investments in a photovoltaic and
solar thermal system at the Würzburg site. These investments, which fall
under categories 7.6 “Installation, maintenance and repair of renewable
energy technologies”, are classified as taxonomy-eligible capital expenditure in accordance with section 1.1.2.2.(c) of Annex I to the Delegated Act
on Article 8 of the EU Taxonomy Regulation. As the remainder of the total
capital expenditure for taxonomy-eligible or non-taxonomy-eligible economic activities, adjusted for corporate investments, arises at the Group sites, e.g. for new production centres, this difference is broken down on the
basis of the percentage of taxonomy-eligible revenue in order to determine the percentage of taxonomy-eligible capital expenditure in the total
product portfolio. The resulting taxonomy-eligible capital expenditure is
assigned to category A. The sum total of the taxonomy-eligible category A
and category C capital expenditure is used as the numerator for calculating
the taxonomy-eligible share of capital expenditure as no category B capital
expenditure arose in the year under review.
Taxonomy-aligned capital expenditure
It was not possible to report on taxonomy-aligned capital expenditure coming within category 7.6 “Installation, maintenance and repair of renewable
energy technologies” during the year under review, as no DNSH evidence
was available for the individual types of taxonomy-aligned capital expenditure. In the case of economic activities under category 3.6 “Manufacture of
other low-CO2 technologies”, it was possible to report on taxonomy-aligned
capital expenditure as a result of the application of a revenue-based allocation key. On balance, the total taxonomy-aligned capital expenditure coming within category 3.6 “Manufacture of other low carbon technologies” amounted to €7.7m in 2022, including €4.3m via the allocation key
and €3.5m via the capitalisation of development expenditure for taxonomy-aligned business activities. The total taxonomy-aligned investment expenditure is equivalent to 15.5% of the total capital expenditure of €49.8m
in the year under review.
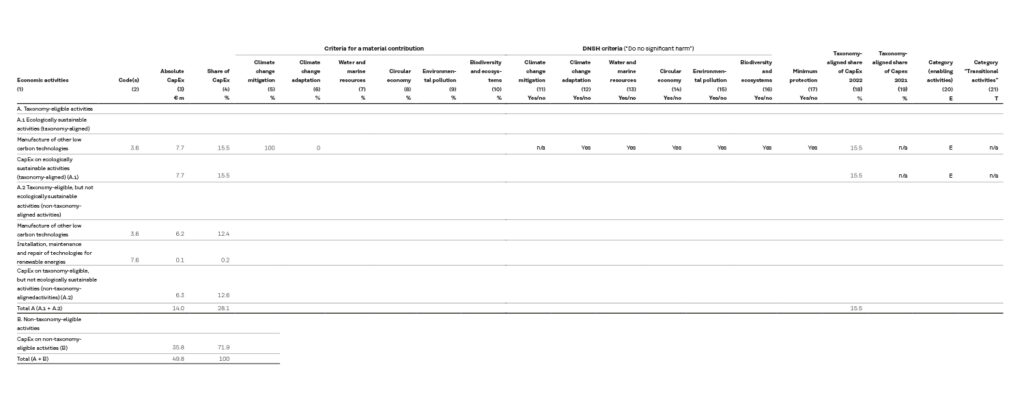