Koenig & Bauer attaches extraordinarily high importance to its responsibility and its tradition spanning more than 200 years. As a pioneer of in-company social policies, we have always taken our responsibility towards our employees seriously. Indeed, it is firmly anchored in our corporate values. We are committed to the preservation and conservation of the environment through our initiatives for emission-reduced and resource-saving products and manufacturing processes along the entire value chain. As a sustainability enabler, we embrace our responsibility towards our customers. Corporate social responsibility by means of donations and sponsoring is also part of Koenig & Bauer’s corporate identity. Integrity in our business activities and respect for human rights are core elements of our corporate governance practices. With our strategic sustainability goals, we seek to address our social, ecological, social and ethical responsibilities even more firmly and develop our Company sustainably.
As part of our strategic process, we have redefined goals for the sustainable development of our Group and adopted a detailed roadmap for our ESG activities. As a provider of solutions, we want to be our customers’ sustainability enabler and support them as a technology partner in reducing their ecological footprint. Various eco-components and innovative technical solutions that we have developed help to reduce carbon emissions by lowering energy consumption, waste and the use of other resources such as inks and varnishes. Ecodesign criteria are taken into account in the Group’s new and further developments. By applying detailed sustainability profiles, we want to highlight energy consumption and the potential for saving energy, waste and other resources by means of various eco-components and innovative technical solutions in a clear form. We are working on algorithms and software solutions to individually calculate the product carbon footprint (PCF) as an additional feature in the sale of carbon-neutral presses. The printing press is awarded the carbon-neutral ecological seal through offsets for the residual carbon footprint in the form of certified climate action projects. We are aiming to reduce the carbon emissions (Scope 1 and 2) of our production plants by 75% over 2019 by 2025 and to achieve carbon neutrality from 2030 onwards. On the basis of the results of the Scope 3 carbon emission measurements, we want to define measures and corresponding targets for reducing these emissions in a timely manner. Another key objective is to promote the health of our employees, to prevent work-related hazards and to minimise the number of accidents at work as far as possible. In addition, we want to further increase the degree of diversity already achieved in terms of gender, age, international background and experience. One priority in this regard is the “Level Playing Field Women” project, which is currently being stepped up. In addition to diversity as an element of our corporate culture, we want to make use of additional activities to take a stand against racism and discrimination. And finally, we are committed to the preservation and conservation of the environment through the integration of sustainability in the procurement process and the fulfilment of comprehensive due diligence obligations. At the Koenig Bauer & Group, we accept our responsibility towards the community.
As a UN Global Compact participant, Koenig & Bauer is actively supporting the implementation of the United Nations’ 17 Sustainable Development Goals (SDGs), which define the framework for responsible business in economic, ecological and social terms. The UN Global Compact is the world’s largest sustainability initiative for sustainable and responsible corporate governance with a global network of over 18,700 participating companies and organisations from 170 countries. The participants have undertaken to support the ten principles of the UN Global Compact in the fields of human rights, labour standards, environmental protection and the fight against corruption, to promote the 17 SDGs within their respective spheres of influence and to report annually on the progress achieved. Koenig & Bauer has identified seven of these SDGs as priorities and is addressing them with strategic sustainability initiatives. In particular, the Group’s diverse sustainability activities are targeted at the following SDGs: “3 – Good health and well-being”, “4 – Quality education”, “5 – Gender equality”, “8 – Decent work and economic growth”, “12 – Responsible consumption and production”, “13 – Climate action” and “17 – Partnerships for the goals”. We see our scope for influence and for making a difference in these goals.
In summer 2021, we joined the Blue Competence sustainability initiative. Blue Competence is an initiative launched by German industry association VDMA to promote sustainability in mechanical and plant engineering as well as to further sustainable solutions in this industry. Furthermore, we became the first printing press manufacturer to join the Healthy Printing Initiative in July 2021. The basic idea underlying the initiative is to advance the implementation of the Cradle-to-Cradle (C2C) design approach in the printing industry. Accordingly, the initiative aims to promote the use of environmentally friendly substrates, inks, varnishes and auxiliaries in the printing of paper, corrugated board and cardboard products, plastics and other substrates and ultimately to enable efficient recycling systems. Koenig & Bauer is also a member of the 4evergreen alliance, which networks paper and board manufacturers, folding carton manufacturers, producers and retailers of brand-name products and suppliers of technology and materials as well as the collecting, sorting and recycling industry. The alliance aims to communicate more effectively the benefits of fibre-based packaging materials as alternatives and to promote EU-wide harmonised product design guidelines that facilitate recyclability and support the optimisation of collection systems as well as appropriate recycling infrastructures and technologies. Finally, as a member of the Holy Grail 2.0 initiative, we are working towards finding a common solution for intelligent packaging recycling. Under the auspices of the European Brands Association (AIM), more than 120 companies and organisations along the packaging value chain are pooling their expertise. Stamp-sized digital watermarks that can be printed on the surface of packaging and function as a “digital recycling passport” are a promising approach for an efficient circular economy.
Disclosure option selected
Koenig & Bauer publishes the non-financial disclosures required under section 315c in connection with sections 289c to 289e of the German Commercial Code and the disclosures required under Regulation (EU) 2020/852 of the European Parliament and of the Council of 18 June 2020 on the establishment of a framework to facilitate sustainable investment and amending Regulation (EU) 2019/2088 (hereinafter referred to as the EU Taxonomy Regulation) in this separate non-financial Group report, which is published outside the combined management report. References to disclosures outside the Group’s non-financial report constitute further information and are therefore not part of the report. The two separate reports are published in Bundesanzeiger together with the auditor’s opinion; they are also published on the Company’s website at https://www.koenig-bauer.com/en/investor-relations/financial-reports/.
Business model, non-financial risk report and materiality analysis
In order to identify the reportable non-financial topics of the past financial year, we conducted a materiality analysis based on the 2016 version of the Sustainability Reporting Standards of the Global Reporting Initiative (GRI). The Koenig & Bauer Group’s business model is presented in the combined management report (see page 16 of the 2021 annual report). Koenig & Bauer’s Management Board is responsible for sustainability, including non-financial reporting on the environmental, employee and social aspects defined by law, the observance of human rights and anti-bribery and anti-corruption precautions. Under the Management Board’s business allocation plan, the Chief Executive Officer is responsible for corporate responsibility (ESG) and, hence, for all reported non-financial aspects. Sustainability has been established as a new area of responsibility with direct reporting lines to the Chief Executive Officer. It is currently in the process of being built up. On the Supervisory Board, the Personnel Committee is responsible for sustainability/ESG. In addition to regular updates for the Personnel Committee, the entire Supervisory Board is briefed by the Management Board on the progress of the ESG roadmap during the annual strategy day. Within the scope of its statutory duty of supervision, the Supervisory Board has engaged PricewaterhouseCoopers GmbH Wirtschaftsprüfungsgesellschaft to audit this separate non-financial consolidated report to obtain limited assurance (see the audit report on pages 152 onwards of the annual report).
The risk inventory conducted at the end of 2021 did not identify any material, reportable non-financial risks resulting from business activities, business relationships, products or services that have an adverse impact on the non-financial aspects mentioned. Risks that affect the Company externally are presented as part of the risk report in the combined management report (see pages 36 et seq. of the 2021 annual report).
A materiality analysis was conducted to define the main aspects of the non-financial Group report. In accordance with the CSR Directive Implementation Act (sections 315c/289c of the German Commercial Code), the analysis is composed of the following elements: environmental, employee and social matters, observance of human rights and anti-bribery and anti-corruption precautions. In a preliminary step, a comprehensive list of non-financial matters potentially of relevance for customers, employees, investors and business partners was prepared within these five aspects in accordance with the German Commercial Code. On the basis of this list, a workshop was held at the end of 2018 to identify the non-financial issues that are of material importance for our business activities and relationships, products and services within the five main aspects identified in accordance with the German Commercial Code. A short list was then prepared setting out all the matters which on a scale from 0 (not material or relevant) to 10 (highly material or relevant) had an average materiality score of at least 5 for the main issue in question and its business relevance. These material non-financial items were included in the non-financial Group reports for 2018 and 2019, as well as in the non-financial Group report for 2020 after a review of the materiality analysis.
At the end of 2021, a new, comprehensive materiality analysis involving external and internal stakeholders was performed on the basis of an online questionnaire. The internal respondents were managers and experts from operations management, production, service, personnel management, personnel development, quality management, product management and innovation, construction, development & process technology, safety/health/ environment, facility management, compliance & internal auditing & risk management, corporate strategy, business/corporate development, marketing and communications. All business units and, in particular, employee representatives across the Group were involved. In addition to industry representatives from other components industries, the external stakeholders questioned primarily included customers and brandowners as their customers together with banks, scientific experts and students. A response rate of 57% was achieved for the online questionnaires. On a scale from 0 (not material) to 10 (highly material), the participants assessed the non-financial matters on which the Company had previously reported in two respects, namely their influence on the applicable non-financial aspects and their business relevance for the Company. The participants did not propose any additional material non-financial aspects in the materiality analysis. The points mentioned had already been covered by earlier reports. All non-financial matters with an average score of at least 5 for both aspects were included in the materiality matrix. The following materiality matrix summarises the results authorised by the Chief Executive Officer:
The sections below describe the following material non-financial issues on the basis of these results: Environmental aspects entail the Company’s environmental and energy management as well as ecological printing technology. In addition to our appeal as an employer and the need for diversity, the key employee-related aspects include recruiting and training junior specialists and managers, systematic personnel development as well as health and safety. With respect to social aspects, social responsibility and high product quality in the interests of greater work and process safety in printing operations have been defined as material. This is followed by a presentation of the aspects of the Company’s commitment to human rights and high labour standards as well as anti-corruption and bribery precautions.
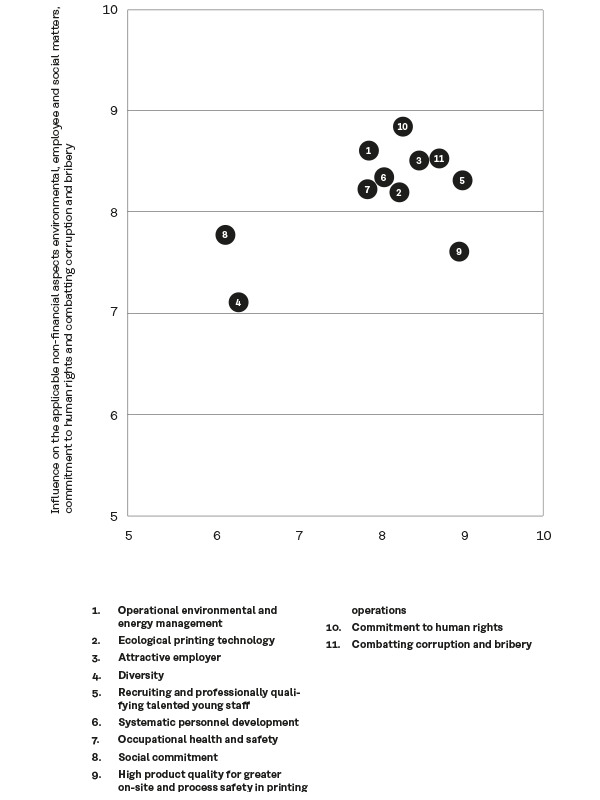
Disclosures on the EU taxonomy
The Taxonomy Regulation is a key component of the European Commission’s action plan to redirect capital flows towards a more sustainable economy. It represents an important step towards achieving carbon neutrality by 2050 in line with EU goals as the Taxonomy is a classification system for environmentally sustainable economic activities. For implementation, the EU Commission published the delegated act on Article 8 of the EU Taxonomy Regulation on 6 July 2021, the first part of the FAQs on 20 December 2021, which was supplemented on 31 January 2022, and the second part of the FAQs on the implementation of the taxonomy reporting obligations on 2 February 2022.
In the year of first application of the EU Taxonomy Regulation, we make use of the simplification rules set out in Article 10 Paragraph 1 of the delegated act on Article 8 of the EU Taxonomy Regulation. Accordingly, only the share of taxonomy-eligible economic activities as well as those that are not taxonomy-eligible in total revenue, in capital expenditure and in operating expenses and only the qualitative information relevant to such disclosures, as referred to in section 1.2 of annex I to the delegated act, are disclosed in this Group non-financial report 2021. All figures in this section are based on 2021. No capital expenditure and operating expenses coming within category b of the taxonomy arose during this period.
When identifying potential taxonomy-eligible activities, we first classified our economic activities according to the NACE codes. As Koenig & Bauer’s business activities match NACE codes 28.29 and 28.99, we followed the requirements of the category “3.6. Manufacture of other low carbon technologies”. In terms of the environmental goal of climate protection, we have classified revenue of products or product groups as taxonomy-eligible where the printing presses and systems also aim to significantly reduce CO2 emissions for customers due to the technology in use and contribute to considerable savings in CO2 emissions over the entire life cycle compared to alternative products on the market. Under environmental matters in the chapter “Ecological printing technology” we present some of our technologies for reducing CO2 emissions in print production. In addition to internal calculations of the energy and resource requirements of the products or product groups in the usage phase at our customers, we have also used publications from competitors obtained from requests for tenders as a basis for identifying taxonomy-eligible revenue. We then aggregated the revenue determined in the accounting departments of the Group or the respective business units for each product or product group classified as taxonomy-eligible. In order to derive the taxonomy-eligible proportion of total revenue, the revenue thus calculated is compared with the Group revenue reported in accordance with IFRS. For more details on our accounting policies for our consolidated revenue, please refer to page 87 of our 2021 Annual Report. Our consolidated net revenues are presented in the consolidated financial statements on page 73 of the 2021 Annual Report within the Revenue line.
R&D expenses, maintenance and servicing costs in production, sales and administration as well as expenses for short-term and low-value leases determined by Group accounting are used as the denominator to identify the proportion of taxonomy-eligible operating expenses. The consolidated income statement on page 73 of the annual report includes the non-capitalised R&D expenses and the other cost items mentioned in cost of sales, distribution costs and administrative expenses. The expenses incurred for measures for reducing energy consumption or increasing energy efficiency at the factory buildings form a partial value in the numerator for identifying the taxonomy-eligible proportion of operating expenses. These expenses, which fall under category 7.3 „Installation, maintenance and repair of energy efficiency equipment“, are classified as taxonomy-eligible operating expenses in accordance with section 1.1.2.2. (c) of Annex I of the delegated act on Article 8 of the EU Taxonomy Regulation. As the remaining part of the total operating expenses arises for taxonomy-eligible and non-taxonomy-eligible economic activities at the Group locations and a more precise breakdown is not possible on the system side, this difference is determined on the basis of the percentage of taxonomy-eligible revenue in the entire product portfolio in order to calculate the taxonomy-eligible operating expenses of category a. The sum total of the taxonomy-eligible category a and category c operating expenses is used as the numerator for calculating the taxonomy-eligible share of operating expenses and to avoid double inclusion.
In order to identify the taxonomy-eligible proportion of capital expenditure, the investments determined by Group accounting in accordance with IFRS are placed in the denominator. These comprise additions to property, plant and equipment and intangible assets during the financial year before depreciation and revaluation, including those resulting from revaluation and impairment for the financial year 2021 and excluding changes in fair value. The denominator includes additions to property, plant and equipment (IAS 16), intangible assets (IAS 38) and right-of-use assets (IFRS 16). For more details on our accounting policies in relation to our investments, please see the accounting policies section of the notes to our 2021 Annual Report. The total investments are shown in the consolidated statement of changes in intangible assets, property, plant and equipment on page 90 of the 2021 Annual Report in the additions column. The first partial value of the numerator for determining the taxonomy-eligible share of capital expenditure includes the investments for a photovoltaic system at the Radebeul site and for energy efficiency measures at the Mödling site. These investments falling under categories 7.2 “Renovation of existing buildings” and 7.3 “Installation, maintenance and repair of energy efficiency equipment” are classified as taxonomy-eligible capital expenditures according to section 1.1.2.2. (c) of Annex I of the delegated act on Article 8 of the EU Taxonomy Regulation. The second partial value of the numerator includes the capitalised development costs for the taxonomy-eligible products or product groups that are allocated to category a of taxonomy-eligible capital expenditure. As the for general corporate investments adjusted remainder of the total capital expenditure arises for taxonomy-eligible and non-taxonomy-eligible economic activities at the Group locations, e.g. for new production centres, this difference is determined on the basis of the percentage of taxonomy-eligible revenue in the entire product portfolio in order to calculate the taxonomy-eligible proportion of capital expenditure. The taxonomy-eligible capital expenditure determined on this basis is also assigned to category a. The combined total of the three partial amounts calculated in this way is used as the numerator for determining the taxonomy-eligible proportion of capital expenditure and also avoids double inclusion.
In summary, the percentage of taxonomy-eligible and non-taxonomy-eligible activities at Koenig & Bauer in 2021 in revenue, operating expenses and capital expenditure relative to the Group’s total activities is as follows:
Total in €m | Share of taxonomy-eligible economic activities in % | Share of not taxonomy-eligible economic activities in % | |
Revenue | 1,115.8 | 32.1 | 67.9 |
Capital expenditure | 36.5 | 38.4 | 61.6 |
Operating expenses | 55.5 | 33.1 | 66.9 |
Environmental matters
At Koenig & Bauer, environmental aspects and the observance of high quality and safety standards are taken into account as far as possible along the entire value chain, from the product idea and purchasing to production and the commissioning of the printing presses. Right from the start of the development and design stage, attention is paid to energy and resource efficiency in the assembly and operation of printing presses and finishing equipment. In addition to carbon emissions, a further focus is placed on minimising noise, dust and odour emissions during the production and utilisation of our presses as well as the use of environment-friendly substrates and consumables in the printing, finishing and postpress phases. There are different management processes for the two divergent environmental priorities – corporate environmental and energy management on the one hand and ecological printing technology for the customers on the other – and comprehensive reporting processes and policies are currently being developed for these.
Operational environmental and energy management
Effective environmental and climate protection in the plants as well as the responsible use of resources are priorities for Koenig & Bauer. A permanent focus of our work is on minimising the consumption of energy and resources in production as well as on reducing workplace emissions. We are consistently investing in efficient technologies and equipment to this end. As every reduction in the consumption of energy and resources is reflected in lower carbon emissions, Koenig & Bauer is also contributing to climate protection in this way. Procuring green primary energies is also an important aspect. The production plants in Radebeul and Würzburg hold DIN EN ISO 9001:2015 and DIN EN ISO 14001:2015 quality and environment certification. In addition, our foundry in Würzburg operates an energy management system that has been certified in accordance with DIN EN ISO 50001:2018.
Special priority is being given to reducing carbon emissions at our plants. Following a change of supplier at the beginning of 2020, the proportion of electricity from renewable energies has increased significantly, contributing to the substantial cut in carbon emissions. Since the beginning of 2021, the share of green electricity at the main Group sites has been 100%. We are working on further projects to improve our carbon footprint. From 2024, we will be switching to largely carbon-neutral district heating using green energy at our Radebeul site. Our supplier GETEC mainly relies on biomass from wood pellets and also on solar thermal energy for the provision of district heating. In addition to the photovoltaic systems installed at the sites in Radebeul and Mödling, we are also exploring further photovoltaic projects in order to expand our in-house power generation capabilities. At the Lausanne site, there are plans to cover around 20% of the base-load electricity requirements via a photovoltaic system installed on the roof by the owner of the building. In Würzburg, the possibility for the site to cover its own electricity requirements by means of photovoltaic systems or a combined heat and power plant (CHP) is being considered. Energy savings at our plants are a further important pillar of our sustainability activities. In addition to replacing transformer stations and ventilation technology, this is being aided by the modernisation of production and distribution systems for electricity, compressed air and heat at the Würzburg and Radebeul sites. Another component in our efforts to reduce electricity consumption while simultaneously improving working conditions is the accelerated replacement of lighting systems with highly efficient, automatically controlled LED technology at our sites. The corresponding investments and expenses are included in the taxonomy-eligible category c capital expenditure and operating expenses (see the section on the EU taxonomy).
Dedusting, extraction and solvent distillation plants as well as improved sound insulation in the production and assembly halls reduce workplace emissions such as noise, dust and odour. Supply air systems ensure fresh air at a controlled temperature directly at the workplace. Responsible use of resources also includes sustainable waste management. We avoid waste as far as possible, while waste that cannot be avoided is disposed of correctly in accordance with the legal requirements. With disposal activities, a distinction is drawn between hazardous and non-hazardous materials and between waste recycling and removal. The remeltable metal waste generated in metal-cutting activities in Würzburg is an important raw material in foundry operations. Our waste statistics provide detailed information about the type and quantity of waste produced, broken down according to hazardous and non-hazardous waste.
The following table provides an overview of electricity, natural gas, district heating, water consumption and waste in 2021 compared with the previous year.
2020 | Würzburg | Radebeul | Total |
Electricity | 18,624,871 kWh | 12,245,318 kWh | 30,870,189 kWh |
Gas | 10,757,000 kWh | – | 10,757,000 kW/h |
District heat | – | 10,502,740 kWh | 10,502,740 kWh |
Water | 26,284 m3 | 12,728 m3 | 39,012 m3 |
Waste | 3,633 t | 4,590 t | 8,223 t |
2021 | Würzburg | Radebeul | Total |
Electricity | 21,445,986 kWh | 13,205,058 kWh | 34,651,044 kWh |
Gas | 13,059,762 kWh | – | 13,059,762 kWh |
District heat | – | 12,171,600 kWh | 12,171,600 kWh |
Water | 26,895 m3 | 16,059 m3 | 42,954 m3 |
Waste | 4,047 t | 5,332 t | 9,379 t |
On the basis of these consumption figures, Scope 1 CO2e emissions at the large plants in Radebeul and Würzburg in 2021 were 3,803.4 t CO2e above the previous year (3,165.8 t CO2e), which had been influenced to a greater extent by short-time work and Covid-19 travel restrictions. In addition to the gas consumption figures, the fuel consumption of the predominantly leased vehicle fleet was taken into account for the first time in both reporting years. The site-based Scope 2 CO 2e emissions amounted to 15,248.7 t CO2e, up from 12,621.5 t CO2e in the previous year. In addition to higher capacity utilisation, the emission factors for the German electricity mix, which climbed from 350 g/kWh in the previous year to 380 g/kWh, contributed to this increase. The calculations for located-based Scope 2 CO 2e emissions are derived from the provisional average emission factors for the German electricity mix published by Federal Association of Energy and Water Management. Among other things, the increase in specific emissions from electricity production in Germany was caused by the greater demand for electricity in connection with a decline in wind energy output. On the other hand, the market-based Scope 2 CO2e emissions were reduced significantly from the previous year’s figure of 10,314.9 t CO2e to 4,727.3 t CO2e due to the full procurement of electricity from renewable energy sources.
In order to estimate the Scope 3 CO2e emissions, an initial analysis was carried out with external support and the following results obtained. Scope 3 CO2 emissions of 1,755 kt were measured for 2021, making these the largest part of Koenig & Bauer’s carbon footprint at a figure of around 99%. Accounting for roughly 90% of the total, downstream product usage is the largest driver of Scope 3 emissions. Accordingly, top priority is being given to lowering the energy consumption of products by improving their energy efficiency, expanding digital services such as artificial intelligence for optimum press utilisation and offering the “climate-neutral print production” service. On the upstream side, the strategic orientation in purchasing activities in favour of materials with the lowest possible carbon footprint and the more responsible transportation of materials, finished products and service parts provide further levers for reducing Scope 3 CO2 emissions. A reduction in carbon emissions can also be achieved through targeted incentives directed at employees’ commutes to work. One aspect of this is the planned expansion of the e-charging infrastructure at the employee car parks.
Another direct contribution to climate protection can be achieved through sustainable travel management. Restrictions in business travel to a limited number of participants and important occasions is a significant sustainability lever. In addition, the carbon footprint of every business trip can be significantly improved by means of targeted travel planning including the selection of the method of transport. Koenig & Bauer has modified the Group Policy on Company Travel to reflect this strong commitment to more sustainable business trips.
Ecological printing technology
We view sustainability and climate protection as part of our responsibility towards future generations, especially with regard to our products. Specifically, this is already opening up a wide range of opportunities for placing new products, equipment options and services on the market and for standing apart from the competition. Accordingly, we pay attention to energy and resource efficiency in the production process and in the operation of the presses and equipment when developing and designing our products. A further focus is placed on minimising noise, dust, odour and carbon emissions during the production and utilisation of our presses as well as the use of environment-friendly substrates and consumables in the printing, finishing and postpress processes. When considering the environmental impact of our products, we also take account of the recyclability of the equipment. The components made of steel and grey cast iron are fully recyclable.
We incorporate energy-saving technologies in our new and enhanced products to lower carbon emissions in industrial printing. Koenig & Bauer offers a range of energy-saving alternatives for the drying process, which is one of the most energy-intensive functions in printing operations. The VariDryBlue drying system that we have developed for sheetfed presses is an energy-efficient solution. Energy requirements for drying water-based dispersion coating can be reduced by 22%. This is done by using the hot air twice in the dryer modules. HR and LED dryer modules for interim and final drying are powerful but more efficient alternatives to conventional UV dryers. Waste can be saved and make-ready times shortened by means of various quality measurement and control systems, inspection systems, preset functions and other equipment options. This allows customers to significantly increase the resource efficiency of their printing operations.
In banknote printing, we have developed a system for reducing the carbon emissions of intaglio presses by lowering power requirements. Intaglio presses require a wiping solution which must be pre-heated before use. On the other hand, some parts must be cooled by means of thermoregulation. In order to conserve and reuse energy, a power-saving unit has been developed to harness the synergistic effects between thermoregulation and the provision of a preheated wiping solution. This solution in combination with compressed air saves approximately 83 kW per hour during operation of the intaglio printing press. If all intaglio presses in operation were to use this system, the carbon footprint of banknote printing could be reduced by around 45,000 tonnes of carbon dioxide per year.
Banknote printing presses are as a rule equipped with conventional UV lamps for curing the inks during or at the end of the printing process. As an alternative to this, Koenig & Bauer offers UV-LED systems. This does away with the need for air extraction and lowers energy consumption by roughly 45% per press. In addition, UV LED lamps have a far longer service life, do not contain any mercury and do not give off any ozone. If all of Koenig & Bauer’s banknote customers were to use this new LED technology, carbon emissions could be reduced by around 10,000 tonnes a year.
Further innovative solutions in banknote printing permit greater resource efficiency through lower waste and a reduction of up to 25% in ink consumption on the intaglio printing presses. Ink consumption is optimised by aligning the paper to the length and position of the printing plate. The size of the stencil, which has a direct bearing on ink consumption, can be reduced significantly without impairing the print quality. If all intaglio banknote printing machines were equipped with this technology, around 2,500 tonnes of ink would be saved annually, while 5,000 tonnes of waste and the associated carbon emissions would be avoided. A current project is also making it possible to apply ink in the printing process only where it is needed. This reduces ink consumption by a further 25% to up to 50%.
Koenig & Bauer offers customers the VisuEnergy X management system to further improve energy and resource efficiency in their printing operations and throughout the entire company. As a trusted advisor in the field of sustainability, we provide customers with comprehensive support ranging from system and requirements analysis to energy consulting covering energy technology, efficiency and procurement strategies and their orientation as climate-neutral companies. This extends from the planning phase of a printing press investment to efficient production and greater economic viability. VisuEnergy X permits end-to-end digitalisation of the company, helps to record environmental data and supports an energy management system that has been certified under DIN EN ISO 50001:2018. Additional tools and services for reducing carbon emissions are also offered.
In addition to technical solutions and systems for energy and resource efficiency, the focus is on minimising further emissions. Examples include low-alcohol or alcohol-free offset printing, reduced powder use, biodegradable fount solution additives and the minimisation of noise, dust, odour and carbon emissions. Product users can select various equipment options to achieve these goals. Roll covers permit low-alcohol printing or the use of alcohol substitutes for conventional, UV and mixed inks to avoid unpleasant odours at the printing company. The emission extraction system is additionally available for UV printing and finishing. Unpleasant odours are prevented and dust simultaneously removed at the press operator’s main place of work, i.e. the press delivery point. In the case of UV printing, suction of the inking units can also help to minimise ink mist. It is no coincidence that in 2000 our apida press was the world’s first sheetfed offset press to be awarded the “Emission checked” ecological certificate by the German industrial compensation society for the printing and paper processing industry.
A further example of our active environmental policies is the migration-harmless ink for food packaging. The food-safe water-based inks used by Koenig & Bauer Durst for digital printing meet the lifecycle-based environmental performance criteria set out in UL ECOLOGO Standard 2801 – 2012 (Standard for Sustainability for Printing Inks). UL ECOLOGO certification was achieved after the assessment of various criteria such as energy use, waste disposal and the reduction of toxic ingredients throughout the entire product life cycle.
Koenig & Bauer has in Climate-Partner a competent partner for climate-neutral printing at its side. With the front print manager on ClimatePartner’s online portal, it is possible to calculate in detail carbon dioxide emissions from printing and, at click of a button, to neutralise them by funding climate protection projects. Numerous certified climate protection projects meeting various internationally acknowledged standards such as Gold Standard, VCS and Social Carbon are available. The participating printing companies can utilise the “climate-neutral printing” label as a competitive differentiator.
Employee matters
A committed, experienced, highly qualified, loyal and healthy workforce permanently strengthens the Company. With their ability to develop bespoke premium-quality high-tech printing presses and to provide comprehensive services, our employees generate sustained value for our Company. In the competition for talent, Koenig & Bauer comes to the fore as a globally active and innovative company with its pronounced orientation to values that are firmly entrenched in its corporate culture. In addition to offering appealing jobs offering a favourable life/work balance, the Company’s human resources strategy concentrates on recruiting specialist and management staff and developing, motivating and retaining employees. A variety of measures, such as the early involvement of young management talent in projects and various training opportunities assist employees in unleashing their full potential. The Company suggestion scheme actively integrates employees in improvement processes on an ongoing basis. Employees receive 20% of the annual savings achieved from quantifiable improvement proposals.
Attractive employer
Koenig & Bauer offers its employees modern working conditions including mobile working, flexitime and working time accounts. Mobile working allows employees to perform duties outside the Company’s offices via mobile devices provided that this is compatible with the activities they are required to perform. Mobile workplaces are generally available for these groups of employees. The Group ensures good working conditions for employees offering high standards of occupational health and safety. By pushing new technologies such as digital printing and expanding into structurally growing packaging printing markets, the Company is enhancing its appeal as an employer by engaging in fields of activity offering potential for the future.
Employees are assisted in finding an appropriate work/life balance including special offers for working mothers and fathers as well as flexible working hours, temporary or permanent part-time working arrangements, mobile working arrangements, childcare and additional vacation leave as well as family breaks and sabbaticals. At 3.8%, the proportion of part-time employees in the Group was the same as in the previous year. Childcare facilities during the school holidays, including comprehensive holiday camps during the summer holidays, are constantly being expanded. The child-minding centre adjacent to the Company premises in Radebeul enjoys strong employee acceptance as it is aligned to their working hours. Koenig & Bauer has been a member of the Family and Work Alliance in the Würzburg region since 2006. Company childcare is also to be provided at the Würzburg site. Other activities and events such as excursions and swimming courses for employees’ children as well as the children’s and youth day held at the Würzburg plant on the school-free Day of Repentance and Prayer in recent years had to be cancelled due to the pandemic. This was also the case with the customary sports events, the annual children’s Christmas party in Radebeul organised in cooperation with the kindergarten as well as the Advent church service for all active and former employees followed by a Christmas party and a visit by Santa Claus for the little ones in Würzburg. We will be offering these events and activities again as soon as the underlying conditions permit this.
In addition to a low fluctuation rate of 1%, the average length of service of 20.2 years at the Company’s sites in Radebeul and Würzburg is a good indicator of employee loyalty at Koenig & Bauer. 92 long-service staff celebrated milestone career anniversaries in Radebeul and Würzburg in 2021. 37 were able to look back on 40 years of service, while 55 had been with the Company for 25 years.
Diversity
Koenig & Bauer attaches particular importance to the diversity of its workforce. A high degree of diversity has already been achieved in terms of ethnicity, age and religion or world view. Of the 2,989 employees in Radebeul and Würzburg, 20.1% are younger than 35 years, 48.5% aged between 35 and 55 and 31.4% are over 55. As with many other mechanical engineering companies, Koenig & Bauer has a relatively small proportion of women of 13.7% (previous year: 13.8%) in the Group compared with other sectors. Various activities are being initiated to widen the proportion of female employees, including correspondingly worded job advertisements, a “girls day”, career fairs, internships and school visits. In addition to the general efforts aimed at increasing the share of female employees at our Company, a diversity initiative with a comprehensive package of measures such as special training and female mentoring programmes to increase the proportion of women in management positions has been launched. Our diversity policy also aims at achieving a greater variety in terms of international background and experience. We want to use the potential arising from heterogeneous teams in the interests of sustained corporate development. At the end of 2021, the proportion of women stood at 25% at the first management level and at 12.5% at the second management level below the Management Board at Koenig & Bauer AG. These ratios had stood at 14.3% and 6.7%, respectively, one year prior to this.
Recruiting and professionally qualifying talented young staff
In-house training ensures Koenig & Bauer is able to meet its high demand for qualified specialists in development, design, production, commissioning and service. The dual vocational training model has a long tradition at the Company. The Company’s own state-recognised vocational training centre in Würzburg has been qualifying specialists for over 150 years by closely interlinking theory and practice. In view of recent developments in the labour market, it is also becoming increasingly challenging for Koenig & Bauer to fill all apprenticeship positions – especially in the commercial and technical professions. In addition to tried and tested tools such as open training days, we also use social media to recruit junior staff. In this way, school-leavers can gain insight into what a traineeship with the Company entails together with the training syllabus and methods. The vocational training department in Radebeul works with numerous schools in the region to inform them at an early stage of the training available at the plant. The vocational training centre in Würzburg also makes use of its good contacts with schools in the region. In addition to the various opportunities for learning more about apprenticeships at Koenig & Bauer, work placements for school students offer a good basis for early career orientation for when they leave school. All internships are structured in such a way that the school students can try things out for themselves and acquaint themselves with the apprenticeship professions at the Company. A number of undergraduates are completing their theses at Koenig & Bauer or attending internships or practical semesters at Koenig & Bauer. In addition, the Company offers placements for undergraduates in almost all parts of the Company to acquaint them with the world of Koenig & Bauer printing presses.
At 315 as of 31 December 2021, the number of apprentices and interns was slightly down on the previous year’s figure of 333. Accordingly, the Groupwide apprenticeship ratio fell to 5.8% (2020: 6%). In the year under review, 71 young people embarked on their industrial/technical or commercial apprenticeships in 14 different professions at Group locations. The apprenticeships range from mechatronics technician to industrial mechanics and from machining mechanics to industrial business management assistants. As in earlier years, the 22 trainee mechatronics technicians accounted for the greatest proportion of apprentices. For the first time, we are training IT specialists in the field of process and data analysis. In 2022, we will be expanding our apprenticeships to include electronics technicians for automation technology. Career beginners at Koenig & Bauer also include students enrolled in dual-studies courses, who are completing their practical phase at the Company in addition to attending university. 63 apprentices at the two main plants in Radebeul and Würzburg successfully sat for their final exams at the chambers of industry and commerce. Regular top rankings as top, second- or third-best performers and good to very good results in the final examinations testify to the acknowledged high quality of the training centres. In 2021, the best young skilled workers in Saxony in the occupations of mechatronics technician and metalworking mechanic came from the Radebeul plant. Koenig & Bauer Radebeul was included for the 22nd time on the list of the top training companies in the Saxon metalworking and electrical industry and, thus, more frequently than any other member company. Upon successful completion of their apprenticeships, the future specialists face good career prospects with the possibility of permanent employment at the Group’s main sites in Würzburg and Radebeul.
Systematic personnel development
In the interest of the Group-wide advancement of employees, we have established a personnel development program as a modular system that defines target-oriented methods for various hierarchical levels. All personnel development initiatives have an international focus and incorporate all Group companies as well as the global sales and service units. The annual employee appraisals are a proven personnel management tool that give employees and their line managers the opportunity of providing direct feedback in both directions and discussing their current views and goals. In addition, executives also receive training in various areas such as leadership, team building and conflict management. Development assessments are used to appraise executives and junior staff externally. This is followed by an internal process in which the immediate line managers draw up competence profiles on the basis of the results gained. In an ensuing step, the managing directors and department heads evaluate the executives and junior staff from their business units in calibration workshops to gain a neutral view. A comprehensive competence matrix is available in a database for the group undergoing assessment. Within this group, high potentials are identified in the subsequent coordination rounds for each business unit attended by members of the Management Board and executive staff on the basis of criteria such as age, language skills, international profile, leadership capabilities, expertise (technical/commercial skills), career background, mobility/willingness to change and skills/potential. Thereupon, individual development plans with further training measures are drawn up. The goal is to fill management positions from the Company’s own ranks. We want to strengthen our appeal as an employer by means of this systematic career development. Moreover, systematic talent management addresses the expectations of career-oriented high performers and thus also helps the Company to retain qualified employees.
In addition, the one-year junior management programme (JuMP) with participants aged between the early 20s and 30s aims to systematically prepare junior staff for management tasks. It commenced in 2021 with 22 junior managers in two groups. In addition to the technical learning modules, junior managers work on practical projects from everyday business life. This encourages international networking and allows them to develop innovative problem-solving approaches for business challenges.
Another indication of the strong employee involvement is the “From Employees for Employees” training series, which consistently addresses topics of current interest. A total of 252 employees attended 14 lectures in the year under review. Another component of the human resources development portfolio is consulting services for organisational development at the team, departmental and divisional level including corresponding workshops. In addition, professional and personal coaching is available for all target groups in the Company. 47 new employees completed a targeted digital onboarding process to prepare them for their duties at the Company and to familiarise them with its corporate culture. Professional provider management for purchasing and coordination as well as quality assurance for external service providers such as trainers and coaches is a further aspect of human resources development.
The Koenig & Bauer Campus learning management system is a modern platform for in-company training and further education within the Group. All employees worldwide have access to the online catalogue via a personal profile, in which they can view all training courses available to them. In addition to traditional face-to-face training, the catalogue also includes online learning applications in all relevant fields in order to encourage decentralised virtual learning. Each employee can register for the compulsory training courses at their own initiative and apply for the voluntary offerings set out in this catalogue. Line managers can confirm the request for training directly in the system with a click of the mouse. The system documents each employee’s education history, generating reminders of training sessions and instructing line manager to register their employees for training courses. In addition to 876 face-to-face training sessions (2020: 218), 16,860 e-learning sessions, including the 952 GoodHabitz online courses, were held in the year under review. This is a significant increase over the previous year’s figure of 9,714 e-learning sessions. Compliance was a key topic covered by e-learning, with 7,541 online sessions held (2020: 3,920).
At the Würzburg site, the Azubis@work personnel development programme is used to support the training of career-beginners. In four modules spread over the first two years of their apprenticeship, the trainees work on topics such as correspondence, telephone skills, communications and conflict management as well as personality development and team skills. In response to advancing digitalisation, the vocational training centre has developed a media concept for conveying to junior staff the relevant skills on a comprehensive basis. Starting with basic skills such as knowledge of how media offerings and IT systems work and their underlying principles, the media concept focuses on the ability to analyse and critically evaluate data and information together with a detailed consideration of the significance of media and digital technologies for the economy and the career and working world. For the first time, an alumni meeting of Würzburg apprentices was organised in the year under review to give current thirdyear trainees an insight into various career paths.
Occupational health and safety
The health and safety standards at the production plants in Würzburg and Radebeul are certified in accordance with DIN ISO 45001:2018. Various measures are being taken to achieve further improvements in safety and ergonomics. Regular checks and consultations are held to monitor compliance with health and safety regulations and to make recommendations for optimising work processes. By avoiding non-ergonomic movements and heavy lifting, it is possible to minimise illness and accidents. The hazard assessments are updated regularly. Regular instruction and training seek to raise employees’ awareness of any hazards that may arise.
15 accidents per 1 million hours worked with lost working time of one day or more were registered for the core workforce in the year under review at workplaces at the Würzburg and Radebeul plants. The previous year’s figure of 12.3 had particularly been influenced by the greater use of short-time work. Extensive analyses of these incidents are performed as a basis for defining preventive measures for reducing workplace accidents. At the same time, the monthly report on accident frequency rates by business unit and department facilitates the development of targeted responses. Potential hazards are addressed and highlighted in special monthly campaigns.
Workplace health promotion and prevention also enjoy high priority at Koenig & Bauer. The various preventive health programmes are managed and implemented by HR management and by the Koenig & Bauer in-company health insurance fund (Koenig & Bauer BKK), which is operated as an autonomous public-law corporation. Individual counselling and training sessions are used to teach employees health skills and encourage them to work in a health-conscious manner. As in earlier years, courses were held for the apprentices as part of a health promotion programme specifically tailored to their needs. New additions to the Koenig & Bauer BKK programme included yoga courses, which are held both face-to-face and online.
The diverse offers also include occupational health management. As a result of the Covid-19 pandemic, meetings were often held in the form of videoconferencing to avoid direct contact. Regardless of where they live, employees suffering from mental illnesses receive a qualified initial diagnosis within 14 days through the in-company health insurance fund’s ProPsych programme. If the initial diagnosis indicates the need for a medical response, the employee concerned receives psychotherapeutic treatment within a further 14 days. Special behavioural therapy for obesity is also offered under this programme. The aim of the “BGM-innovativ” programme initiated at the Würzburg and Radebeul sites is to provide coordinated care for at-risk and ill employees suffering from musculoskeletal disorders in order to avert illness or to prevent it from becoming chronic, to shorten the duration of the illness and absences and to permanently maintain employability. The new health and fitness app provides members of the Koenig & Bauer health insurance fund with useful tips on healthy eating, living more consciously and moving correctly and effectively.
Under the motto “Our eventful life – For me. For you. For us.” employees can take part in different activities each quarter, e.g. “Strengthening your immune system in the winter”, “Getting off to a strong start in the spring”, “Simply living in summer” and “Arriving in autumn”. Posters and flyers distributed at the factories were used to draw attention to the changing offers, information on which is published via an app and on the Koenig & Bauer BKK website.
Reflecting the fact that employee health is a top priority for Koenig & Bauer, extensive hygiene and prevention measures were consistently implemented throughout the Covid 19 pandemic. In addition to comprehensive opportunities for tests, a broad-based vaccination campaign was carried out at the Würzburg and Radebeul sites in different waves for first, second and booster vaccinations. Ventilation and filtration were another focus of the package of measures to contain the pandemic.
Social matters
Koenig & Bauer is a pioneer in employee welfare as well as a supporter of social projects. Even before social security was introduced in Germany, the Company had already established the predecessor of an in-company health insurance fund in 1855. Founded in 1873, the fund for disability, widow and orphan benefits continues to exist to this very day. We are committed to our responsibility to society and sponsor social and cultural projects alongside initiatives for preserving and protecting the environment.
Social commitment
At Koenig & Bauer, social and community involvement includes comprehensive sponsoring and donation activities for projects in the fields of culture, social affairs, the environment, science and technology. The Group sponsoring and donations policy governs its basic approach to these matters and defines a consistent process throughout the Group, including approval rules.
Cultural sponsorships support individuals, groups, organisations or events in artistic fields such as music or theatre via the Koenig & Bauer Cultural Foundation. In 2021, the Mozart Festival and Africa Festival in Würzburg were supported.
Via its community sponsoring activities, Koenig & Bauer provides financial resources or donations in kind all over the world to support social projects and the activities of charitable and non-profit organisations and institutions such as foundations or associations. In addition to supporting regional institutions and initiatives, it particularly focused in 2021 on supporting activities in Africa. In Ghana, the Baobab Children Foundation, which has built up a training centre with an integrated school in recent years, is being funded. The aim is to enable young people between the ages of 13 and 18 years to complete vocational training by sitting for a state examination after four years of schooling and one practical year. Fanny Koenig, the wife of the Company’s founder, was a major supporter of social issues at Koenig & Bauer in the mid-19th century. A Fanny Koenig workshop was set up at the Baobab Children Foundation school in memory of the manager. In Würzburg, an inclusion-oriented primary school already bears its name, while our company founder Friedrich Koenig is also the namesake of grammar schools in Würzburg and Suhl. In addition, Koenig & Bauer is supporting the Bakita Girls Community Centre in Tanzania, which is based on a micro- and macro-sustainability model and provides school education for young mothers and orphans in particular by providing additional vocational training resources. The Ubuhle Care & Development Centre near Pretoria in South Africa was able to purchase a school bus thanks to a donation received from Koenig & Bauer. In addition to its broad-based community activities, the Company also provides Christmas donations for social projects in lieu of gifts for customers. In addition to supporting the Bakita Girls Community Centre in Tanzania, the bulk of the 2021 Christmas donation went to three social projects and institutions in Würzburg. One part of the donation was given to the Antonia Werr House, which offers comprehensive living and support services for women in crisis situations, for purchases of interior furnishings. Support association “Bahnhofsmission” also received a donation for the “Encourager” project, which seeks to train volunteers in psychosocial counselling work. The joint fundraising campaign of employees and companies for the Würzburg Advent charity run supports the activities to promote school and club sports in the Mwanza region in Tanzania. Koenig & Bauer MetalPrint organises an annual fundraising campaign in the form of an employee raffle, with the proceeds going to a children’s and young people’s hospice in Stuttgart, with the Company doubling the amount donated.
In environmental sponsoring, the activities of non-profit and non-commercial organisations in the field of ecology are supported through monetary and non-monetary donations. Koenig & Bauer is supporting a rainforest project in Ghana as part of the Baobab Project. The preservation of the rainforest benefits the agricultural training project via a more stable local climate, serving as a mosaic stone in global climate action. Industry awards sponsored by Koenig & Bauer, such as the Print & Media Award for the most environmentally oriented company of the year, acknowledge printing companies’ ecological commitment.
Koenig & Bauer supports science and technology with financial and non-financial support. It has established an endowed professorship at the Ostwestfalen-Lippe University of Applied Sciences with the aim of promoting development and research in the field of document authentication and classification. The Dr Hans and Benno Bolza Foundation awards prizes for outstanding scientific work in the fields of mechanical and electrical engineering offering sustainable solutions and practical relevance to printing press engineering and technology. The foundations are named after the two great-grandchildren of the Company’s founder, the industrial pioneer Friedrich Koenig.
With their extensive voluntary activities at the Chambers of Industry and Commerce and the Chambers of Crafts, as honorary judges at the labour and social courts, in emergency-assistance organisations such as the Federal Agency for Technical Relief, the fire brigade and the rescue service, as well as in city and municipal councils, the executives and employees make a great contribution to the community. In many cases, employees are given time off to engage in the wide range of voluntary activities undertaken by Koenig & Bauer.
As a globally active printing press manufacturer, Koenig & Bauer has always stood for cosmopolitanism and tolerance. At its Radebeul site it supports the association “Business for a Cosmopolitan Saxony” by taking specific measures to assist and promote the integration of newcomers and immigrants in the local economy. Refugees who have fled their country for political or religious reasons are completing vocational training at Koenig & Bauer or have started work directly and are now part of the regular workforce.
High product quality for greater on-site and process safety in printing operations
Koenig & Bauer attaches great importance to the quality of its products and services. Reflecting this, the quality management system aims at achieving ongoing compliance with the highest quality standards in the production and assembly of the Company’s bespoke, innovative and complex products. The quality management systems at the major production plants in Radebeul and Würzburg, at the Sheetfed business unit in Radebeul, at the Security business unit at the three sites in Würzburg, Lausanne and Mödling and at the Coding business unit in Veitshöchheim are certified in accordance with DIN EN ISO 9001:2015. Product development focuses on work and process safety, reliability and user-friendliness.
Commitment to human rights and high labour standards
In its role as an employer as well as a supplier and buyer of products and services, Koenig & Bauer is committed to protecting human rights and views this as a core element of responsible corporate governance. The United Nations Framework on Business and Human Rights (“Protect, Respect and Remedy”) offers a guideline for corporate policy. With the incorporation of a duty to observe human rights in the terms and conditions of purchase and the systematic observance of these requirements in all material business activities, the Company makes sure that its business partners acknowledge and respect human rights in the same way that it does. Further measures are being implemented under the Supply Chain Due Diligence Act, which comes into force on 1 January 2023. The purchasing conditions impose on external business partners a duty to respect employee rights and to observe labour law. The code of conduct for suppliers included in the terms and conditions of purchase also stipulates the observance of statutory and contractual quality and safety standards as well as environmental requirements particularly in connection with the use and processing of hazardous substances. Suppliers particularly undertake to refrain from using child labour and to avoid any form of discrimination. In addition to the main business processes, the selection of and cooperation with relevant business partners are also subject to initial and ongoing review. As part of the digitalised compliance check, business partners express their commitment to the code of business conduct and receive compulsory training on Koenig & Bauer’s compliance standards.
The Group provides good working conditions for employees offering high standards of occupational health and safety. Koenig & Bauer makes sure to offer all employees equal opportunities. We want to additionally consolidate equal opportunities as the basis for personnel decisions in the Group. Respectful and responsible interaction with each other and the prevention of all forms of discrimination are an integral part of our corporate culture. We want to ensure discrimination-free workplaces for employees regardless of gender, age, disability, religion, origin or sexual orientation and promote inclusiveness. People with restricted mobility also have a place in Koenig & Bauer’s regular workforce.
Combatting corruption and bribery
Responsible and transparent corporate governance oriented to long-term value creation has high priority at Koenig & Bauer. We regard integrity and compliance as indispensable in business transactions and pursue a zero-tolerance policy. The Group-wide compliance management system (CMS) creates the basis for ensuring that business practices satisfy the highest compliance and integrity standards. The contents and activities of the compliance organisation are reviewed on the basis of a compliance plan adopted in consultation with the Management Board and the Supervisory Board’s Audit Committee at the beginning of each year.
The CMS focuses on preventing any violations of laws, standards or internal guidelines. A regular compliance risk analysis forms the basis for the organisation and processes. In addition to monitoring changes in the law and reported compliance risks, one component of the risk assessment entails the continuous sharing of information on the internal processes of the Koenig & Bauer Group companies. For this purpose, a compliance team has been set up and is composed of representatives from information technology, human resources, accounting, taxes, data protection as well as the local compliance officers. In 2021, all subsidiaries additionally submitted for the first time a standardised report on their compliance situation as part of the fixed agenda of the meetings of the relevant supervisory bodies (e.g. boards, shareholder assemblies, supervisory boards, governance bodies). Comprehensive guidelines have been issued and the necessary processes established on the basis of the results of the risk analysis to ensure compliance and integrity in all business activities. Any changes that are identified in the risk situation or requirements are addressed by duly modifying the internal guidelines. The corporate compliance manual issued across the entire Group combines our business code of conduct, compliance rules and the main Group policies in a single document. The latest version of the policies can be viewed in the policies portal on the Koenig & Bauer intranet. Reflecting the far-reaching adjustments to the policies, we are currently in the process of creating a new, updated compliance manual. The CMS attaches great importance to combating corruption and bribery. This also reflects Koenig & Bauer’s broad-based commitment to promoting fair competition.
The comprehensive compliance and integrity standards can only be fully effective if employees are aware of them and adhere to them. For this purpose, 13 online training sessions on the main aspects of compliance and the code of conduct are currently available throughout the Group. Available in several languages, they are mandatory for every new employee. The use of an IT process with the Koenig & Bauer Campus training management system, which is based on SuccessFactors, automatically ensures that training is held in cycles determined by risk criteria applicable to the employee’s specific position. Compliance with this requirement is monitored through regular reminders and escalation processes. Following the initial implementation of online training at the Koenig & Bauer Campus at the end of 2017, almost 24,000 compliance training courses had been completed by the end of 2021, including over 16,500 that were directly related to anti-corruption precautions. The Koenig & Bauer Campus has since been rolled out across all 50 relevant subsidiaries, meaning that almost all employees in Europe, Asia, North and South America can attend compliance training via the Koenig & Bauer Campus. The training courses are made available via the Koenig & Bauer intranet to local branches that are not linked to the Campus system. The local compliance officers were responsible for monitoring the completion of training. Due to the Covid-19 pandemic, only a small number of face-to-face training sessions were held in 2021. However, relevant and updated compliance information was communicated via the Intranet, the compliance officers at the subsidiaries or individual messages.
The preventive CMS measures are complemented by a regular review of their effectiveness to identify potential for improvement. In particular, internal and external compliance assessments are carried out periodically at Koenig & Bauer AG and its subsidiaries for this purpose. The established, internal whistle-blower system is currently being replaced by a new online platform that will continue to ensure that potential compliance violations can be reported anonymously by employees and additionally also by third parties in contrast to the previous system. Under the Group policy, all suspicions are followed up consistently and, if necessary, disciplinary or legal action taken. This applies equally to reports by the media or authorities of any violations by Koenig & Bauer companies. In such cases, cooperation is sought to clarify the circumstances. Koenig & Bauer complies in full with any notification or cooperation duties.
Koenig & Bauer is also committed to fighting corruption and encouraging compliance beyond its own business activities. Since its foundation in 2013, the Banknote Ethics Initiative (BnEI) has established a strict code to prevent and combat corruption and anti-trust violations in the field of banknote printing and trading. The principles espoused are not only recognised among the members of the BnEI but are also adopted by a significant proportion of central banks and banknote printers worldwide and form part of their procurement processes. As a founding member of the BnEI, Koenig & Bauer Banknote Solutions has agreed to be bound by strict rules of conduct and transparency, compliance with which is verified as part of regular recertification based on an audit programme developed by the BnEI. This accreditation was successfully renewed in 2020.
The promotion of ethical behaviour, transparency and compliance forms the focus of our activities, particularly in the security and banknote printing industry. With the KBA-NotaSys Integrity Fund, which was founded in 2017, Koenig & Bauer finances international projects to enhance compliance processes and culture. By the end of 2021 a total of 42 projects initiated by universities, associations and institutions in Europe, South America and Africa had been funded. The project initiators include Transparency International, the German Institute for Compliance (DICO), the German Institute for Efficiency Testing (DIEP) and various Swiss and German universities. The results of the projects were published and presented to interested groups and also discussed at the meetings of the project managers organised by the Fund. Total funding of EUR 5 million was allocated.
Further details of the compliance management system can be found in the compliance section of Koenig & Bauer’s website.
The ongoing analysis of possible compliance risks is a decisive prerequisite for the Company’s ability to continue meeting the high standards of rule-compliant business conduct and integrity in the future. The analyses conducted in the individual business units in 2021 did not indicate any new compliance risks, nor were any suspected compliance violations confirmed.