Company profile
For the past 204 years, the Koenig & Bauer Group has been synonymous with innovation and technical progress in the global printing industry and is thus also the world’s oldest printing press manufacturer. Koenig & Bauer’s high-tech presses and systems, which are consistently tailored to meet customer requirements, and its comprehensive range of services enable people all over the world to come into contact with printed, processed and finished products. In addition to various types of packaging for the food, beverage, pharmaceutical and cosmetics industries, this also includes banknotes, decorations and laminates as well as magazines and newspapers. The products are used in packaging, banknote, security, industrial, commercial and publication printing.
Koenig & Bauer addresses these (end) markets through the development, assembly and worldwide distribution of sheetfed and web offset, flexo and digital printing presses, flatbed and rotary die cutters, folding-box gluers and special presses for security, metal decorating, glass/hollow containers and coding. The presses use almost all common printing technologies that apply ink efficiently and precisely to a wide variety of substrates such as paper, cardboard, foil, glass, hollow containers and sheet metal. This makes Koenig & Bauer’s range one of the broadest in the industry. The comprehensive expertise derived from addressing many sub-markets provides a good basis for innovation and for new applications in the growing packaging printing markets. The Koenig & Bauer Group is the global market and technology leader in the growing market for packaging printing and banknote printing. Its services encompass a wide range of customer-oriented offerings from fully automated print workflows to networked printing and constitute an important component of our business model alongside new press business. Koenig & Bauer thus intends to continue expanding its service business, which is less dependent on economic cycles, and is aiming for a long-term share of around 30% of Group revenue. Group revenue came to €1,115.8m in 2021. Worldwide, a total of 5,397 employees at eleven production sites and many sales and service organisations ensure the satisfaction of our customers.
Global presence and employees
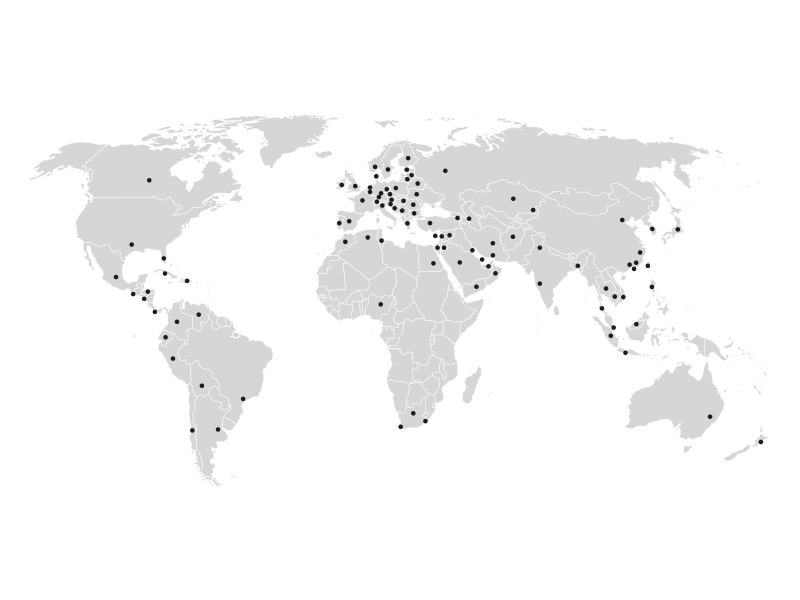
Koenig & Bauer operates eleven manufacturing plants in Europe and many sales and service organisations in almost all parts of the world. The P24x efficiency programme is to optimise the production and assembly plants, including intra-group sharing by means of relocation and realignment, particularly at the Tavazzano site in Italy.
The export ratio widened slightly from 84.6% to 86.2% in the year under review. Over the last few years, we have expanded our sales and service network in the markets of the future, including the emerging markets on the peripheries of Europe and in Asia. A nationwide sales and service system has been established throughout Latin America via our subsidiary Koenig & Bauer LATAM.
The Koenig & Bauer Group employed 5,397 people worldwide at the end of 2021. Compared to the previous year (31 December 2020: 5,593), this was a decline of 196.
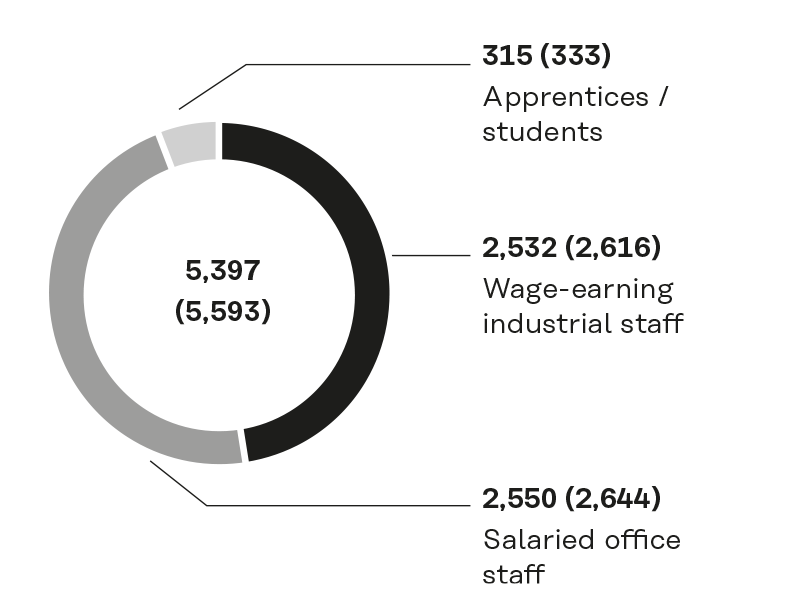
As planned, the effects of the global Covid-19 pandemic led to a staff reduction in 2021 via the P24x efficiency programme. These staff reductions were achieved through socially acceptable measures such as natural fluctuation and by leaving vacant positions unfilled as well as through the use of phased retirement arrangements, transfers and ring exchanges, pension bridge agreements and the adoption of a voluntary leaver programme. Due to the progress made in achieving the personnel targets under P24x, the Management Board decided on 23 June 2021 that there would be no redundancies for operational reasons at the German sites in 2021 and 2022. In addition, use was made – albeit to a lesser extent than in the previous year – of short-time working instruments depending on the capacity utilisation in the individual areas at the German sites. The Koenig & Bauer Group recruited additional staff in key growth areas, including IT and services as well as new applications and products for the expanding packaging market. In connection with the apprenticeship year starting in September 2021, the Koenig & Bauer Group is retaining its training policy despite the difficult global economy in order to create career openings by offering talented young people an apprenticeship. In this way, the Company is covering its high demand for qualified specialists, especially in the technology sector and in mechanical engineering, by means of in-house training. In 2021 a total of 71 apprentices (previous year: 76) and dual-course students embarked on their first steps in their new careers with the Koenig & Bauer Group. They already have the promise of a permanent employment contract upon the successful completion of their apprenticeships.
Sustainability
With its “Exceeding Print” strategy, Koenig & Bauer is driving forward sustainability as the greatest challenge facing the packaging industry in the future, thus systematically expanding its already successful activities in this area, which is of crucial importance for the Group’s future development. The statutory reporting obligations under the CSR Directive Implementation Act (CSR-RUG) are discharged with the publication of the non-financial Group report as a separate part of this annual report with references to the combined management report on pages 135 ff. The non-financial Group report is available on the Company’s website at https://www.koenig-bauer.com/en/investor-relations/financial-reports/.
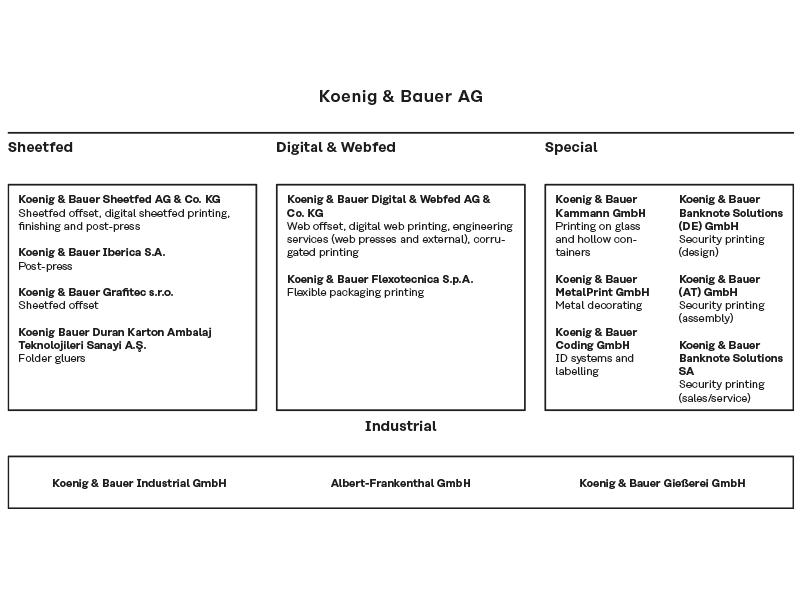
Decentralised organisation with a holding company structure
The Koenig & Bauer Group is composed of Koenig & Bauer AG as the holding company and its subsidiaries. As of 31 December 2021, 38 companies were included in the consolidated financial statements in addition to Koenig & Bauer AG. As shown in simplified form in the diagram, the core subsidiaries are allocated to the three segments Sheetfed, Digital & Webfed and Special on the basis of their business activities. The domestic and foreign sales companies that mostly offer sales and service functions for several segments are allocated to the segments in accordance with their activities. Similarly, the business units defined as production service providers (“Industrial”, see diagram) are allocated to the three segments on the basis of their activities.
Business activities of the segments
The diagram setting out the Group structure also shows the internal reporting structure of the Koenig & Bauer Group in 2021. In line with its operating business, the internal reporting structure is divided into the following segments: Sheetfed, Digital & Webfed and Special. These also form the reportable segments in accordance with IFRS.
The Sheetfed segment, which makes the greatest contribution to revenue, offers a wide range of sheetfed offset presses under the “Rapida” name from half to super-large formats for the packaging and commercial printing market. The presses are individually equipped with a variety of quality measurement and control systems in accordance with customer requirements. In addition, customers can also expand their sheetfed offset press by adding a variety of finishing modules, e.g. to enhance packaging with the addition of a hologram foil. The segment portfolio also includes aggregates for the further processing of printed products such as rotary and flatbed die-cutters as well as folding-box gluers. These are particularly important for the rapidly growing packaging market, as a folding box still has to be die-cut, folded and glued after the printing process.
In conjunction with its joint venture partner Durst, the Koenig & Bauer Group also offers a sheetfed digital press under the VariJET 106 name for the production of personalised, individualised and versioned print products, especially for the folding-carton market. It integrates inkjet technology in the platform of the high-performance Rapida 106 press. The system’s modular design enables digital inkjet printing to be combined with optional printing and inline finishing options used in offset printing. The joint venture with the Durst Group for the development and marketing of single-pass digital printing systems for the folding-carton and corrugated-board industry was established in 2019.
In addition to classic services, a variety of digital services are also offered and are constantly being expanded. This also includes digital workflow and logistics solutions. The Koenig & Bauer Customer Community is increasingly combining numerous digital services for our customers in a user-friendly interface. Looking forward, it will be launched under the name “myKyana” with new branding and an expanded range of functions available to all Koenig & Bauer customers.
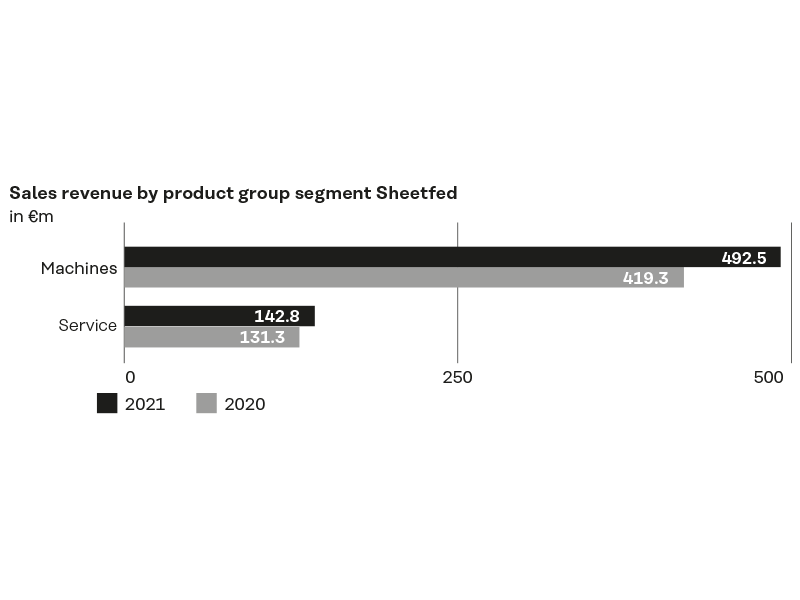
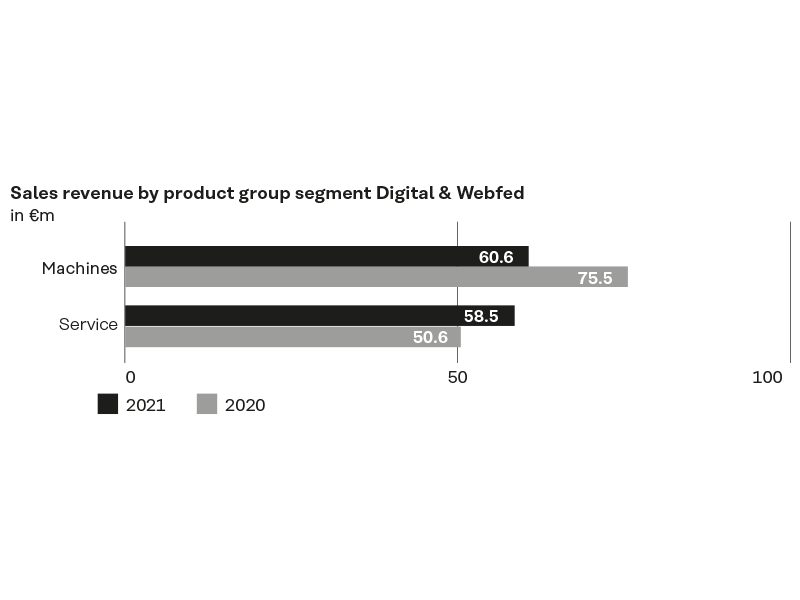
The Digital & Webfed segment offers a variety of new presses that address the three printing processes: letterpress (flexographic printing), gravure and flat printing (offset printing).
In addition to web offset presses, which are mainly used in newspaper, commercial and publication printing, web presses for digital printing are also offered (RotaJET platform). They address commercial printing as well as decorative and beverage carton printing in the industrial printing market. The RotaJET is able to print on a wide variety of different substrates, from thin printing paper to solid cardboard. This includes packaging, decorations, posters, leaflets, folding boxes, books and coffee bags. Since 2014, HP has been partnering with Koenig & Bauer to develop the world’s widest digital printing press. The HP PageWide T1190 for pre-printing corrugated-board cover layers is also targeted at the packaging market and complements Koenig & Bauer’s web digital printing activities. Customer requirements for individualised and personalised packaging as well as swift time-to-market productions necessitate shorter turnaround times and smaller print runs while at the same time calling for high quality requirements. The combination of analogue (flexographic) and digital printing allows small, medium or large runs to be completed. In addition to the web presses, integrated paper logistics are available. This is because automation, an integrated workflow and process optimisation are crucial elements of the “total cost of process” approach.
The segment offers the CorruFLEX for direct (sheetfed) corrugated printing and post-print. In addition to direct printing, the CorruCUT (with rotary die-cutters) enables inline production of rotary die-cut boxes from corrugated-board sheets. The CorruJET complements direct corrugated-board printing by offering a digital printing solution for the production of personalised, individualised and versioned corrugated-board print products in conjunction with Durst. The Corru family also addresses the packaging printing market.
The segment offers various flexoprinting presses that are used for producing flexible packaging, especially in the food sector. At the customer’s request, the presses can be equipped with a variety of inline integrations. The paper logistics referred to above are also used for the film reels. The second pillar of the Digital & Webfed segment is a broad range of services that includes both traditional and digital services.
Just under 50% of the segment’s revenue is accounted for by spare parts and services, with newsprint presses exhibiting a downward trend. Revenue from sales of new offset newsprint presses contributed 6.0% to segment revenue (31 December 2020: 19.2%) and 0.7% to Group revenue (31 December 2020: 2.4%).
The Special segment addresses the market for banknote and security printing via the Banknote Solutions business unit as well as three other interesting submarkets within the packaging printing market.
In addition to special presses for banknote and security printing, Banknote Solutions also holds expertise in banknote and security design and production and offers sophisticated electronic quality control systems. The comprehensive range of services from conventional technical service to the webshop round off the banknote and security printing range.
Kammann supplies printing systems for the direct decoration of hollow bodies made of glass, plastic or metal. Directly decorated glass containers are mainly used for cosmetics, perfume and spirits products in the premium segment. In addition to the predominant screen printing process, hot stamping, digital printing and many other decoration processes can be optionally integrated in the precise and flexible transport systems. Here, too, the digital printing process enables customised, personalised and versioned
printed products for glass/hollow-body direct printing. Worldwide service and support is offered through an international service network.
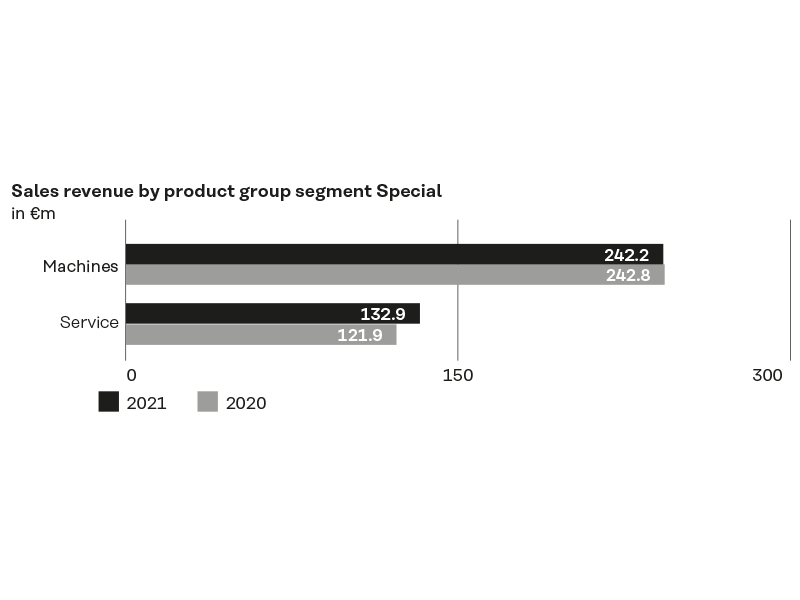
and service business in the Special segment
MetalPrint offers end-to-end systems for the decoration of 2- and 3-piece cans. To decorate a 3-piece can – which is mainly used for food – complete production lines that print, paint and dry tinplate sheets are utilised. The range includes multicolour presses and coaters in combination with thermal sheet dryers or UV drying systems, as well as customised sheet handling systems and energy-efficient exhaust air purification technology. Metal sheets are not used to decorate 2-piece cans for beverages. Instead, cups or bowls are printed directly, painted and then dried with CS MetalCan. Comprehensive services, from technical support to individual training, complete the range of services offered by MetalPrint.
Coding supplements the segment portfolio with solutions for all industries from pharmaceuticals and cosmetics to floristry: variable data, logos and barcodes are printed, marked and coded on different substrates on a just-in-time basis. Production reliability and speed with a typeface of excellent print quality is crucial for the food and beverage industry in order to apply the legally required best-before date or batch traceability data accurately. In the pharmaceutical and cosmetics industries in particular, manipulation-proof labelling and seamless product traceability are playing an increasingly important role. The comprehensive service portfolio ranges from service and maintenance contracts to “Visual ServiceSupport”.
Industrial is an internal and external production service provider, manufacturing high-precision components for printing presses and external customers in the mechanical and plant engineering sector in conjunction with other companies. It specialises in precision-machined large parts made of cast iron or steel, complex prismatic and rotating parts, gears, curves, sheet metal assemblies, rollers and the environmentally friendly coating of rotating parts. In addition, Industrial offers further services such as assembly, engineering and logistics.
Management and control
Koenig & Bauer AG is a public limited company (“Aktiengesellschaft”) under German law with a dual management structure. Its Management Board is composed of five members:
- Dr Andreas Pleßke, (Chief Executive Officer and Director for the Special
segment), - Dr Stephen Kimmich (Chief Financial Officer),
- Christoph Müller (Director for the Digital & Webfed segment),
- Ralf Sammeck (Director for the Sheetfed segment and Chief Digital
Officer) and - Michael Ulverich (Chief Operation Officer – Production, Purchasing &
Logistics).
The business allocation plan shows the breakdown of the Management Board duties as well as the distribution of functional responsibilities as of 31 December 2021.
Business distribution plan of the Koenig & Bauer AG Management Board – valid from 1 January 2021
Chief Executive Officer – Dr Andreas Pleßke | Management Board – Dr Stephen Kimmich | Management Board – Christoph Müller | Management Board – Ralf Sammeck | Management Board – Michael Ulverich |
The Chief Executive Officer represents the Management Board and the management in relations with the Supervisory Board and its committees. He is responsible for: | ||||
• Strategic Group development • Segment responsibility for “Special” • Public relations • Group human resources • Compliance & audit • Legal and insurance • Marketing • Corporate responsibility (ESG) | • Finances, accounting, income taxes • Information technology (IT) • Investments • Investor relations • Group controlling & consolidation • Operational corporate planning • M&A processes* | • Segment responsibility for “Digital & Webfed” • Management of Koenig & Bauer Digital & Webfed • Group-wide service coordination | • Segment responsibility for “Sheetfed” • Management of Koenig & Bauer Sheetfed • Group-wide sales coordination • Group-wide coordination of the digital transformation • Brand ownership management* • Group key account management* | • Responsibility for “Industrial” & Foundry • Group-wide strategic purchasing • Operational purchasing and disposition (holding company, D&W, Industrial, Banknote Solutions, Sheetfed) • Intellectual property • Corporate technical standards • Machine platform concept* |
Koenig & Bauer AG’s Supervisory Board consisted of twelve members as of 31 December. Under the German Stock Corporation Act (AktG), the Supervisory Board is responsible for appointing or dismissing the members of the Management Board, monitoring and advising the Management Board, adopting the annual financial statements, approving the consolidated financial statements and approving or advising on important aspects of corporate planning and decisions. The Supervisory Board report on page 7 and the corporate governance declaration provide details on how the Management Board and the Supervisory Board work together and on corporate governance at Koenig & Bauer AG.
Goals and strategy
P24x efficiency programme achieving steady progress in 2021 fully in line with the implementation plan
In order to strengthen our position as one of leading suppliers for the printing industry and to increase operating profitability, the efficiency programme “Performance 2024”, which has been in place since 2019, was further developed and extended in 2020 in response to the impact of the Covid-19 pandemic and renamed “Performance 2024 extended” (P24x).
In addition to increasing efficiency, the programme also aims to scale the Group. The primary aim of the four-year programme is to strengthen longterm competitiveness, with a focus on the growth market of packaging. A variety of initiatives are being taken to enhance the range of printing presses in line with market needs, digitalise processes and reduce production costs.
Specifically, the programme provides for the following measures:
- A change in the supply chain organisation by adapting Group-wide structures, harmonising procurement and production processes and adopting innovative approaches to parts and component optimisation.
- Adjustment of cost and personnel structures and improvement of productivity by streamlining and standardising processes.
- Increased development and design effectiveness and efficiency through product, process and organisational optimisation such as design-to-cost projects.
- Continuation and acceleration of the development of new products for packaging in sheetfed and web printing with analogue and digital printing technology, hollow-body printing, finishing as well as solutions for banknote production.
- Reduced administrative expenses through the further bundling of tasks as shared services, adjustments to sales and service structures.
- Optimisation of production and assembly plants, including intra-group sharing, relocation and realignment of production and assembly.
Assuming that all innovation processes as well as process and product developments are continued and stepped up, this should yield savings that will increase annually to reach over €100m by 2024. Koenig & Bauer is aiming for the adoption of the defined measures to have a positive impact in 2021, with more than 30% of the planned savings to be achieved. At around €46m, they were significantly higher than in the previous year. The implementation of the measures planned for 2021 should ensure that more than 60% of the total cost savings take effect in 2022. Following the completion of the measures planned for 2022 under the efficiency programme, a good 90% of the total targeted savings should be noticeable in 2023.
Provisions were recognised in 2020 for the short-term and medium term non-recurring costs of €57.6m for the personnel measures required for this, with a corresponding effect on earnings. Due to the progress made in achieving the personnel targets under P24x, no redundancies for operational reasons are necessary at the German sites in 2021 and 2022. The resultant reduction of around €23m net in the expenses required for this was made possible only through the constructive and cooperative collaboration with the employee representatives, with whom modern and socially acceptable measures to reduce job numbers were agreed upon.
“Exceeding Print” corporate strategy
The resolute continuation of the P24x initiatives will be gradually transferred to the new Group strategy adopted at the beginning of December. Koenig & Bauer has pooled its corporate goals in “Exceeding Print” by focusing on its existing strengths of sustainability, modularity and digitalisation. Based on the global megatrends and intense discussions with customers and experts, the Company has defined its strategic direction for the coming years. Megatrends play a crucial role in corporate strategic planning. They describe complex, long-term processes of transformation with enormous dimensions and effects on the economy and society. Their impact is not isolated. Rather, they influence and strengthen each other mutually. This is also reflected in the path that Koenig & Bauer has already adopted, leading to greater digitalisation and modularity and resulting in more economic success in its core markets, especially packaging printing, as printing processes will require less material and energy, thus becoming more sustainable. The way in which Koenig & Bauer is driving forward its transformation from a traditional mechanical engineering company into an agile technology group is addressed in the three strategic areas of action.
Koenig & Bauer is becoming MORE SUSTAINABLE:
Sustainability is one of the greatest worldwide challenges of our times. It is with this in mind that Koenig & Bauer is designing its products and processes to make them ready for the future. In addition to the European Green Deal, the main drivers are the Company’s own sustainability goals. Along with its responsibility towards its customers and employees, as a member of the UN Global Compact, the world’s largest sustainability initiative, the Group aims to increase even further its efforts to deliver its ecological, social and community responsibilities. It is aiming to reduce the carbon emissions of its own production plants by 75% by 2025 and to be completely carbon-neutral from 2030 onwards. To support its customers in reducing their ecological footprint, the Company is pursuing the following goals:
- Accelerate the portfolio of solutions for a circular economy through
products, substrates and process expertise - Create new innovations to replace non-ecological packaging and reduce
waste - Enable customers to reduce energy and resource requirements
The Company wants to achieve these goals jointly with others; for example as a member of the 4evergreen alliance network, in which Koenig & Bauer can look for suitable solutions at an early stage with producers of paper, cardboard and folding cartons, brand owners, suppliers of technology and materials as well as the waste collection, sorting and recycling industry. Working with ClimatePartner, Koenig & Bauer supports carbon offsets by promoting certified climate protection projects. In addition, it is a partner in industry association VDMA’s “BlueCompetence” sustainability initiative and is the first printing press manufacturer to join the “Healthy Printing” network.
For Koenig & Bauer, sustainability also means championing social responsibility, diversity and anti-discrimination. Greater diversity with regard to gender, age and international background also forms part of the Company’s strategic orientation as a social goal. One priority is the promotion of women, for example through mentoring and career programmes, and extensive measures for achieving a viable work-life balance, as well as antidiscrimination and anti-racism initiatives. Koenig & Bauer assumed social responsibility very early on. For more than 150 years, it has been running its own vocational school, which to this very day guides potential career-beginners and guarantees them a permanent employment contract upon the successful completion of their apprenticeships. As well as this, the Company has had its own in-company health insurance fund since 1855.
Koenig & Bauer is becoming MORE DIGITAL:
In addition to digital printing presses, this also means digital business models and processes for the Company and also involves stepping up the digital transformation within the Koenig & Bauer organisation. Alongside hardware, digital services are becoming increasingly important for networking presses, for collecting and analysing data and for managing processes efficiently. Koenig & Bauer is developing digital services on the basis of highly scalable cloud platforms, making them available to customers via a collaboration portal. The analysis of printing press data forms the basis for evaluating performance, setting benchmarks and defining industrial analytics scenarios. In combination with machine learning, Koenig & Bauer can detect potential disruptions in processes at a much earlier stage and more reliably, triggering service and maintenance on a fully automated basis. This can reduce unplanned downtimes and modify service intervals appropriately.
In addition, Koenig & Bauer’s high-performance digital presses for packaging printing offer new business models for short printing runs, addressing rapidly changing requirements, security elements, track-and-trace solutions as well as personalisation and individualisation. The focus is on the entire value chain to enhance cost optimisation and sustainability. Simple human-machine interfaces help to make operation more intuitive for customers. Koenig & Bauer is responding to the trend towards hybrid printing processes for paper, cardboard, corrugated board and foil by combining analogue and digital printing and finishing technologies. This is widening the range of substrates that can be used for printing. With its forays into the food and beverage carboard industry, Koenig & Bauer will be able to print full-colour digital prints on cardboard packaging.
The digital transformation within the Koenig & Bauer organisation is also helping us to turn “big data” into “smart data” internally and to make use of the opportunities arising from this. Group-wide networking with Google Workspace permits mobile work across different time zones, the advantages of which became particularly evident during the pandemic. Koenig & Bauer relies on SAP S/4 HANA for efficient corporate processes. This system is already in use and is being gradually rolled out across the remaining core companies.
Koenig & Bauer is becoming MORE MODULAR:
In order to offer its customers a broad range of products and solutions, Koenig & Bauer is working on a modular platform for the further development and production of its printing and finishing presses as it masters all industrial printing processes on almost all substrates in its core markets. Modularisation and standardisation offer not only flexibility and efficiency benefits but also cost-saving potential through the systematic shared use of common parts, systems, modules and platforms. This can be explained in very simplified terms by taking the modular sheet construction kit as an example. In sheet-fed printing presses, the sheets for printing are transported from a sheet feeder via the printing units to a sheet delivery unit and then deposited on a stack. Printing presses in the Sheetfed and Special segments have a sheet feeder with a very similar function. One of the purposes of the sheet construction kit is, for example, to achieve the greatest possible standardisation in the feeder model at a wide variety of different levels, such as the aggregate, individual assemblies, components and individual parts. On the one hand, this increases the number of shared parts, generating volume and scale effects that can also have a positive impact on procurement and production. At the same time, the availability of spare parts can also be increased and inventory management simplified. On the other hand, it is possible to optimise product development and design processes and assembly. From the customer’s point of view, a modular platform for future generations of printing presses means that new technologies reach the market more quickly, press operation is more consistent across the board and more uniform maintenance activities can be adopted. At the same time, there are more opportunities for innovation and individualisation, allowing bespoke solutions to be developed.
However, the “Exceeding Print” strategy goes one step further: in order to master the unique complexity of the Koenig & Bauer range, we are also working on Group-wide sales activities in addition to the modular printing press platform. With the establishment of the Group Sales division, Koenig & Bauer has been able to take a further step towards harnessing the synergistic benefits of cross-segment sales and optimising cross-selling on the basis of a shared service promise. In addition to Group key account management as a trusted advisor for comprehensive customer support across Koenig & Bauer’s range, brand ownership management is an essential part of these activities as a basis for entering into a dialogue with international manufacturers and their packaging suppliers about possible printing and packaging technologies and trends.
Markets addressed and growth opportunities
With our range of products and services we address the sub-markets of packaging, banknote, security, industrial, commercial and publication printing and seek to make proactive use of the market opportunities currently arising. Each of these markets offers different growth opportunities, which we describe below.
Future opportunities in packaging printing and industrial printing
The Koenig & Bauer Group’s focus is on structural and sustained growth in packaging printing, which is expanding in tandem with the growth in global gross domestic product (GDP) and the world’s population. Within this market, there are attractive niches on which we are also focusing. In addition to rising global consumption, packaging consumption is benefiting from the boom in e-commerce, smaller sizes due to a greater number of one-person households and heightened regulatory requirements. New online food markets and the trend towards quick commerce, the next stage of e-commerce, are additionally spurring packaging consumption. The restrictions resulting from the Covid-19 pandemic have accelerated some of these trends. What is clear, however, is that e-commerce has emerged as the permanent winner of the coronavirus crisis. On average, global packaging printing is growing at a rate of around 4% p.a. according to various industry studies, with higher growth rates being registered for corrugated-board packaging. For Koenig & Bauer the packaging printing markets for food, beverages and pharmaceuticals are particularly attractive due to their lower cyclical sensitivity. Alongside the rising demands of consumer goods producers with respect to quality, flexibility, cost efficiency and delivery periods, trends in favour of more complex, elegant and colourful packaging will additionally spur capital spending by packaging printers. Packaging is increasingly becoming a brand ambassador and an integral part of the product experience. Unboxing is a core element of the shopping and brand experience, This trend has also been spurred by the pandemic and is continuing. In view of the amount of time spent at home, all customer contact arises in printed form during the “unboxing” stage. This means that flyers, brochures and other printed products are enclosed in the corrugated cardboard box. In addition, more and more exclusive department stores are sending products ordered online in corrugated cardboard boxes that are printed in several colours on the inside.
Growth opportunities through digital printing and in industrial printing
Analogue technologies such as flexo, gravure, offset and screen printing dominate global packaging printing. For reasons of cost, productivity and quality, digital processes such as inkjet printing will only be successful in industrially oriented packaging printing for applications that are economically viable for customers. Technically and economically solid digital printing offers good market opportunities for business models specialising in short runs, greater personalisation and versioning, greater format flexibility, quick time-to-market production and other advantages.
Following the latest RotaJET orders, Koenig & Bauer sees great potential for the sophisticated, high-quality digital printing solution, because digital web printing opens up entirely new possibilities in the customisation of products, i.e. very small print runs, through to disruptive approaches by changing value chains. We assume that gravure and flexo presses in particular will be replaced by high-performance digital presses for industrial applications over the next few years. Digital printing technology not only simplifies the complexity of design handling but also shortens the time from design to print and offers greater flexibility in order placement and customisation of products. This is an advantage in the light of the trend towards shorter runs, more individualised products and fast time-to-market production. Decors for furniture and flooring are printed products that are becoming more and more sophisticated and creative and are also being replaced increasingly quickly in everyday use. Digital printing is spurring the trend towards individuality and design change as it permits swift production even in very small printruns. In addition, manufacturers are able to test new ideas on the market at low cost and with minimum effort. With digital preprint and direct printing on corrugated board, products can not only be placed in the market safely using water-based, food-certified ink jet ink, for example, but also communicate product information to the end consumer and attract their attention by means of seasonal corrugated-cardboard displays at the point of sale (POS), for example. Packaging is thus increasingly taking on the function of a marketing and sales tool. The multitude of new products and the trends towards versioning and personalisation together with ever shorter marketing cycles are ushering in a change in production requirements for liquid packaging (beverage cartons) and, in the future, also film packaging. As a general principle, improved total cost of ownership is the main driver for the shift from analogue to digital production.
Service business in security printing creates stability
Thanks to its good project situation, Koenig & Bauer expects business in security printing presses to remain stable. In view of the highly intense competition, the newly developed, innovative security features are a decisive differentiator and a unique selling point. Despite the increased use of digital payment methods and the Covid-19 pandemic, global banknote production continues to grow at a moderate rate. Growing prosperity and rising population numbers in emerging markets with their high cash ratios as well as widespread scepticism towards electronic payments mean that there will be no reversal in this trend in the market in the medium term, although developments in some countries will vary. Alongside intensive work on new products and security features, service business for the large installed base is being systematically expanded and will make a good contribution to Group earnings in the medium to long term. With packaging printing contributing a larger share of Group revenue, the influence of volatile security printing business will recede.
Muted conditions in the media-related print sectors
Koenig & Bauer anticipates stable business in sheetfed offset presses for commercial printing. The global book market is proving to be flat to slightly expansionary. Web offset presses for newspaper and commercial printing are expected to decline in tandem with lower service business due to a further increase in press shutdowns and printshop closures.
Expansion of service with a focus on digitalisation
The Koenig & Bauer Group is more than just a producer of printing and postprint systems. We define ourselves as a provider of end-to-end solutions that help our customers to achieve success on the market. Our services include inspection, maintenance and calibration as well as retrofits/upgrades and service contracts. We also offer spare parts, consumables and accessories for the presses, which can be ordered online via webshops. Training and consulting services are also provided because innovative presses together with qualified personnel and the identification of potential for improvement in the printshop workflow are crucial for achieving greater productivity and quality along the entire production process. Workflows in the printing industry are becoming increasingly digital and networked. Ever smaller print runs have to be produced in ever shorter times in a high quality and at competitive prices. For this reason, the Koenig & Bauer Group offers integrated workflow solutions to boost productivity and competitiveness.
Remote diagnosis tools have been part of our control centre technology since 1995. Digitalisation is creating increasingly effective services in this area. “Visual ServiceSupport” gives users and hotline technicians a tool allowing them to see exactly what printers or service technicians see when they are standing in front of the press. They can view processes and sequences in the form of moving images and thus gain a quick and comprehensive overview of the state of the press. This facilitates communications, obviates the need for extensive descriptions and reduces the risk of misunderstandings compared with a conventional telephone conversation. “Visual ServiceSupport” thus helps to increase the first-time-fix rate in service cases.
Our integrated workflow solutions are based on the principle of the “networked print factory”, where products, presses and tools constantly share information via RFID chips and sensors. The presses self-configure, switch between different jobs fully automatically and support the operators in their work. This requires tight integration of all business processes with production and the measurement and control systems fitted to the presses. It is achieved by linking data from sales, order preparation, planning, production, controlling, logistics and even web-to-print systems. Information from all process steps along the value chain is available enterprise-wide and in real time. This gives management a 360-degree view of the Company. Our demonstration centre for digital networking solutions in Radebeul shows various workflow solutions. As different presses and programmes are used in each individual case, the optimum workflow cannot be bought off the peg, which is why Koenig & Bauer advises its customers individually.
With “Predictive Maintenance”, we offer our customers a pre-emptive service for our presses and systems to identify faults before they occur and cause unplanned downtimes. We use the sensor data and performance data of the presses installed and networked in the market to identify and proactively prevent a potential malfunction before it occurs using complex algorithms and artificial intelligence methods.
Our digital customer portal, the “Customer Community”, offers our Rapida customers a growing number of digital services combined in a user-friendly and device-agnostic user interface. Via this platform, customers also have access to performance data on their presses via dynamic or performance reports, which offer an overview of the key performance indicators (KPIs) of the press. This gives them access to information at any time and from any location, while at the same time providing them with individual support. The automatically filed predictive maintenance service cases and the information provided to customers in this context by our service engineers allow us to turn unplanned downtimes into planned ones, thus increasing press availability and, not least of all, our customers’ productivity.
“Managed Services” is a virtual assistant supporting customers in the marking and coding segment. The Kyana dashboard provides an overview of the integrated systems, thus making monitoring and central control of networked production facilities easier and safer. At the same time, Kyana provides real-time data around the clock and enables optimum remote service. The Kyana chatbot answers questions about the alphaJET inkjet printer at any time.
Koenig & Bauer is consistently expanding the Customer Community to make it the central platform for service management, customer communications and also for the monetisation of digital services and products. Looking forward, the Customer Community will be launched under the name “myKyana” with new branding and an expanded range of functions available to all Koenig & Bauer customers.
Planning, control and monitoring
Comprehensive set of tools for efficient Group planning and control
The established business management system with differentiated cost accounting provides management with a swift, valid and meaningful set of figures for operational controlling, efficient monitoring and strategic planning and management of the Group and the segments. In addition to central Group controlling for overarching Group and segment management, the individual business units have access to controlling resources.
The results of the annual strategy process culminate in high-level business planning and are presented in detail in the ensuing integrated budget planning phase. The planning horizon for high-level business planning and budget planning is five years. P24x is also embedded in high-level business planning – the content of the programme is controlled in the corresponding workstreams and steering committees as well as a corresponding tool at the system level. The budgets prepared by the Group and the segments are based on detailed income statements, balance sheets and cash flow statements for all consolidated Group companies compiled on a monthly basis in the first two years. Forecasts for the current year are updated on the basis of the reported figures at the same time as the semi-annual and quarterly (Q1 and Q3) financial statements are prepared and also shortly before the end of the year. Scenario analyses simulate different market and cost parameters on a case-by-case basis.
Detailed monthly reporting tracks the current business and earnings situation as well as trends in net working capital and is discussed in the monthly earnings meetings. Service reporting permits efficient coordination of the service activities. Roll-over liquidity previews with cash management provide an accurate view of the financial situation. A 24-month liquidity budget has been prepared since January 2021. Regular reviews by Group management with the responsible segment managers addressing the economic and financial situation, current trends and forecasts supplement ongoing deviation analyses performed by controlling. Measures are defined in the event of any negative deviation in the interests of a swift and targeted response. Systematic implementation of the measures is tracked by close monitoring. Opportunities and risks are detected at an early stage by means of a rollover budget, forecast and reporting process. A risk early detection system has been established to monitor developments and to identify possible threats to the Company’s going-concern status. Any necessary decisions can be made at an early stage on the basis of this comprehensive assessment of Group and segment performance.
The Koenig & Bauer Group tracks revenue and the EBIT margin calculated in accordance with the International Financial Reporting Standards (IFRS) in the version endorsed by the EU on a cross-segment basis as its main target-achievement and management indicators. In addition to these two main financial performance indicators, the Management Board additionally receives reports on order intake, order backlog and service business indicators. Changes in capital employed are monitored on the basis of the cash conversion cycle. To determine this indicator, the ratio of inventories, advance payments for inventories and trade receivables less trade payables and customer prepayments to revenue is calculated. In addition to financial indicators, the Management Board also tracks non-financial performance indicators, particularly quality assurance costs and staff development.
Target agreements providing for variable remuneration components tied to Group, segment and/or personal goals for the year for all executives and non-pay-scale employees heighten motivation and commitment towards the achievement of the Company’s goals.
Research and development
Koenig & Bauer focuses on workflow and digitalisation solutions
Alongside new product developments and enhancements with a focus on packaging and industrial printing, new customer-oriented digital services form the main thrust of Koenig & Bauer’s research and development activities. By offering customised and integrated solutions, we want to improve our customers’ competitiveness by means of improved quality and productivity as well as greater transparency. Group research and development expenses equalled 4.2% of revenue in 2021 (previous year: 3.8%). As well as this, development costs equivalent to 0.5% of revenue were capitalised (2020: 1.1%). Looking forward, the Koenig & Bauer Group’s research and development expenditure will not be curtailed despite the challenging business environment.
In addition to the design-based revisions to press performance, our new and further developments in the Sheetfed segment focused on different formats and efforts to ready the new products for series production together with press design. The new products primarily aim to increase productivity, e.g. with respect to printing plate logistics, which results in improved quality and efficiency, especially for customers with frequent print job changes. In addition, there were further developments in the range of printing substrates. In sheetfed digital printing, further enhancements were made to the VariJET106 together with our partner Durst and unveiled in autumn 2021. In the postpress segment, which includes rotary and flatbed die-cutters as well as folding-box gluers, the new Ipress 145 K PRO large-format press generation was presented alongside other product developments.
In the Digital & Webfed segment, the focus was on product enhancements and particularly also the new pre-toolable rotary press for CorruCUT. This development makes it possible to pre-fit the punching cylinder not in use during production, thus reducing downtimes and boosting productivity. In the area of digital web printing, investments were made in the further development of software, ink and the range of substrates for printing with the RotaJET press. This latter aspect should also be seen in the light of the ability of the press to print on different substrates – from beverage packaging to decors such as laminates and thin paper – and these each have unique requirements or properties.
In the Special segment, Group subsidiary MetalPrint launched MetalStar 4, a new generation of sheet metal printing presses. In addition to the new Laika series, Banknote Solutions also developed two smartphone apps in the year under review. ValiCash™ performs a check based primarily on a structural analysis of intaglio printing and the specific optical features of high-security printing in general by taking a simple photo of the banknote. This technology will particularly help to promote intaglio printing as an essential process in the banknote industry and for other high-security printed products. This verification technology can also be applied to other products such as tax stamps or birth certificates. Smill™ allows users to store digital content on a physical banknote. Both apps help to promote the use of cash, make it safer and easier to handle, add further functions and open up a pipeline of different business models in different markets. For the first time, Group subsidiary Kammann successfully launched a method known as “Digital Printed Relief” for producing embossed structures on glass by means of digital printing in the production environment. This gives customers greater flexibility in decorating products and lowering their costs as dedicated glass shapes are no longer needed. In developing the new alphaJET5 X inkjet printer, Group subsidiary Coding has focused on a new design and operating concept. The printer can now be operated intuitively like a smartphone via wipe gestures, while the system’s extensive connectivity opens up a full range of possibilities for managed services and predictive maintenance.
The connected customer
Using modern technologies such as artificial intelligence with learning algorithms and the Industrial Internet of Things (IoT), Koenig & Bauer is developing the “Connected Customer”. The purpose of predictive maintenance is to detect faults before they cause a press to stop, to minimise downtimes and to convert unplanned downtimes into planned ones. To enable predictive maintenance of printing presses, large amounts of data are collected using artificial intelligence and evaluated at high speed and with a high degree of precision. With the end-to-end IoT-based service process, potential faults and their causes are automatically analysed in the presses before they occur. The results of this analysis are available to all service system operatives including the service technician on site. In addition to this information on the current service case, technicians can also access the full press and service history via the field service app on their mobile device. In this way, service managers plan remote maintenance, required service deployments and downtimes in a customer-friendly and cost-effective manner during production-free times. Further modules to expand the customer community were developed in the year under review. Using Performance Analytics Plus, for example, customers will receive a modern business intelligence tool and instrument that ensures high transparency in the customer’s value chain and supports him in boosting efficiency and effectiveness by means of overall equipment efficiency dashboards and highly customisable diagrams.
Quality management
We want to strengthen customer satisfaction and increase customer loyalty with our standards of quality. Accordingly, we are focusing on optimising all relevant internal processes to offer our customers the best possible quality in our products and services. Quality management covers the entire process chain from product development to after-sales service. We systematically and consistently protect our high quality standards by means of clear rules for contracts, comprehensive control, acceptance and testing processes for the purchase of components, in the production and assembly phase and in the launch of new innovations. Overall, we have achieved further progress in lowering our quality costs but see further considerable potential for reinforcing our quality leadership.