Corporate structures
Company profile
Koenig & Bauer is an international system provider with a particular focus on special printing applications, especially in the packaging sector. The business model is based on an integrated approach that covers the entire production cycle. As a pioneer in printing press engineering with over 200 years of experience, Koenig & Bauer enables people all over the world to purchase a variety of products that go far beyond classic printed products. These include packaging for the food, beverage, pharmaceutical, consumer goods and cosmetics industries, as well as banknotes, decorations, laminates plus magazines, books and newspapers.
The wide range of possibilities is also reflected in the flexibility of the substrates that can be used, including paper, cardboard and corrugated board, films, glass, hollow bodies and sheet metal – all these materials can be printed, decorated, finished and post-processed. Analogue, digital and hybrid printing presses, post-print systems and services are used. With myKyana, Koenig & Bauer offers a central customer portal that, as a constantly growing platform, pools data- and AI-based digital products, workflows and services, thus providing access to the digital world of the company. With its pioneering technologies, such as innovative security solutions to prevent counterfeiting and manipulation, Koenig & Bauer connects the analogue printing world with the digital one. This shows that the targeted use of artificial intelligence optimises production processes, enhances efficiency and promotes sustainability. The company therefore has one of the broadest product and solution portfolios in the industry. The comprehensive expertise derived from addressing many sub-markets forms a solid basis for innovation and for new applications – including outside the core markets. Koenig & Bauer holds a leading position in numerous markets worldwide and is the market and technology leader in the growing market of packaging printing and banknote printing. Service business, which is becoming increasingly digital and non-cyclical, is to be expanded and will account for around 30% of Group revenue in the long term.
Global presence and employees
Koenig & Bauer’s global footprint is reflected in the Group export ratio of 87.1% (previous year: 86.9%). Eleven production sites in Europe result in a high level of vertical integration in production, ensuring reliable supplies and production. Numerous sales and service organisations also contribute to the global footprint.
Koenig & Bauer promotes a culture of innovation and has been closely involved in vocational training since its foundation over 200 years ago in order to maintain its technological lead and to address the shortage of skilled workers and the effects of demographic change. With numerous training opportunities at the Koenig & Bauer Academy and the Koenig & Bauer Campus learning management system, the company is continuously developing its employees and also ensuring requirements-oriented succession planning. The Koenig & Bauer Group had 5,612 employees worldwide as of 31 December 2024 (previous year: 5,741).
Under the “Spotlight” focus programme, around 300 full-time positions – mostly in Würzburg – were eliminated in the specific spotlight areas via a guided voluntary programme. The measures included a wide range of instruments, including voluntary termination benefits, a reduction in weekly working times from 40 to 35 hours and voluntary salary waivers. In addition, flexible working time instruments such as a reduction in outstanding vacation entitlement were also applied. As in the previous year, short-time working was used to a minor extent at five (previous year: two) locations due to capacity utilisation factors.
Workforce as of 31 December 2024
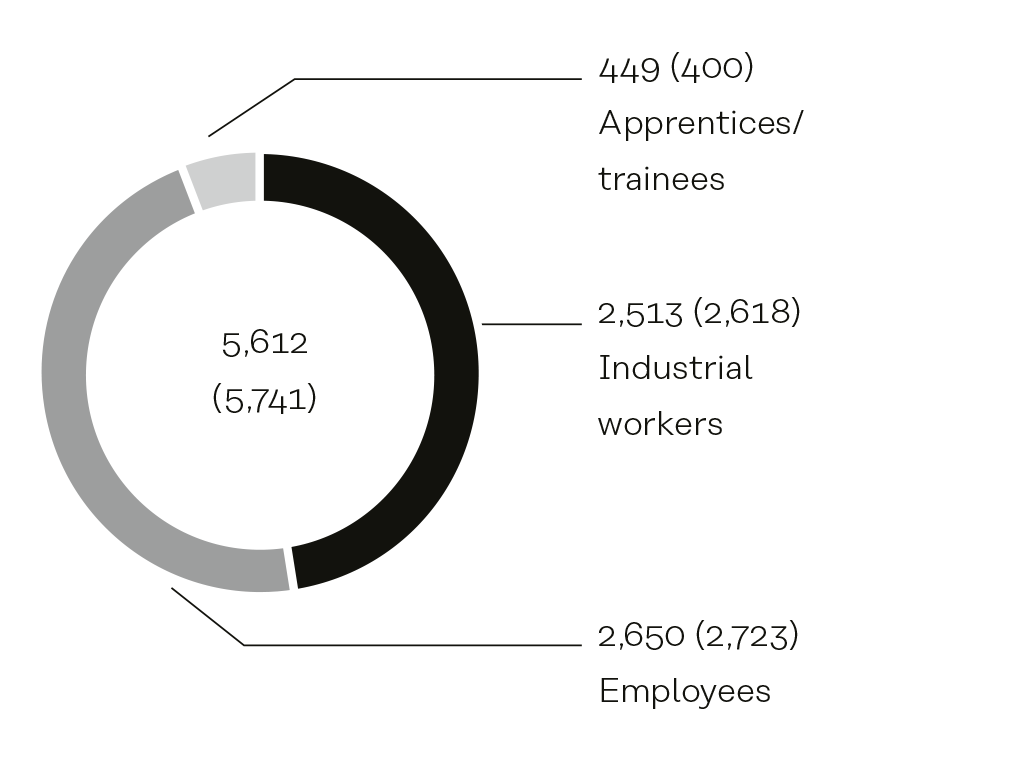
Ahead of the training year starting in September 2024, the company retained its training policy to offer young talents an apprenticeship and, thus, a career perspective. In this way, it is covering its high demand for qualified specialists through in-house training. In 2024, a total of 159 (previous year: 168) apprentices and dual-course students embarked on the first steps of their new careers at the Koenig & Bauer Group. The company has reached its maximum trainee capacity this year. In order to continue providing high-quality training and using its resources efficiently, it has stabilised the number of newly admitted trainees at a comparably high level. In this way, it was possible to fill all advertised apprenticeships again. In addition, the job profiles offered were further diversified to take account of Koenig & Bauer’s future requirements. The largest career groups are mechatronics technicians, industrial mechanics and IT specialists. They already have the promise of a permanent employment contract upon the successful completion of their apprenticeships.
Sustainability
Koenig & Bauer’s “Exceeding Print” strategy comprises three central pillars: sustainability, digitalisation and modularisation. In this way, the company is driving forward the development of the packaging industry and setting an example for sustainable business. The packaging industry faces the challenge of reconciling sustainability and profitability. Regulations such as the EU Packaging & Packaging Waste Regulation (PPWR) call for more recyclability, less plastic and the use of recyclates, while consumers expect sustainable packaging. At the same time, companies are under cost pressure. Koenig & Bauer meets this dichotomy by offering innovative solutions that achieve both ecological requirements and economic goals.
It complies with its statutory reporting obligations by publishing a separate non-financial Group report, which can be found on pages 141 ff. as a separate part of this annual report and contains references to the combined management report. The Corporate Sustainability Reporting Directive (CSRD) had not yet been transposed into German law on the date on which this annual report was prepared (March 2025). This separate non-financial Group report was therefore prepared in accordance with Section 315c in conjunction with Sections 289c to 289e of the German Commercial Code and Article 8 of REGULATION (EU) 2020/852 OF THE EUROPEAN PARLIAMENT AND OF THE COUNCIL of 18 June 2020 on the establishment of a framework to facilitate sustainable investment and amending Regulation (EU) 2019/2088 (hereinafter the “EU Taxonomy Regulation”). No framework was used in the year under review. It can be assumed that disclosures will be made in accordance with the ESRS from 2025 onwards.
Further information is available on the company’s website at http://www.sustainability.koenig-bauer.com.
Decentralised organisation with a holding company structure
Group structure (until 31 December 2024)
The Koenig Bauer & Group is composed of Koenig & Bauer AG as the holding company and its subsidiaries. As of 31 December 2024, 37 (previous year: 37) companies were included in the consolidated financial statements in addition to Koenig & Bauer AG. Two companies are accounted for using the equity method (previous year: two companies).
The annual financial statements of Koenig & Bauer AG are prepared in accordance with the provisions of the German Commercial Code (HGB) supplemented by the provisions of the German Stock Corporation Act (AktG) and can be found on page XX ff.
As shown in simplified form in the diagram setting out the 2024 Group structure, the production subsidiaries are allocated to the three segments Sheetfed, Digital & Webfed and Special on the basis of their business activities. The domestic and foreign companies, which mostly offer sales and service functions for several segments, are allocated to the segments in accordance with their activities. Similarly, the business units defined as production service providers (“Industrial”, in the chart showing the Group structure in 2024) are allocated to the three segments on the basis of their activities. Industrial acts as a production service provider within the Group, manufacturing high-precision components for printing presses in conjunction with other companies. It specialises in precision-machined large parts made of cast iron or steel, complex prismatic rotating parts, gears, curves, sheet metal assemblies, rollers and the environmentally friendly coating of rotating parts. In addition, Industrial offers further services such as assembly, engineering and logistics.
New Group structure (in 2025)
In December 2024, the new segmentation was also announced as an element of the optimisation of governance at the Koenig & Bauer Group. This enhancement of the segment structure that was introduced ten years ago is aligned even more closely to current and future customer needs as well as the applicable business model, thereby streamlining the structures and reducing the number of segments in 2025 from three to two: Paper & Packaging Sheetfed Systems (P&P) and Special & New Technologies (S&T). However, the Group will continue to focus on the high-growth packaging market.
With this alignment, Koenig & Bauer AG as a holding company is streamlining its tasks and assigning more operational responsibilities to the two segments. In addition to pursuing the Group’s strategic responsibilities, the holding company will continue to provide shared services, such as IT, human resources, investor relations, communications, central purchasing and financial services, for all Group subsidiaries.
Furthermore, the domestic and foreign sales and service companies as well as “Industrial” as a production service provider are allocated to the two segments on the basis of their activities.
The members of the Executive Board are closely integrated in the strategic management of the segments. Looking forward, this will make it possible to reduce the number of members to just two, namely Chief Executive Officer and Chief Financial Officer. In the course of 2025, further steps to reorganise the Executive Board will be taken incrementally.
The chart shows in simplified form the future group structure, which will be expanded in the S&T segment in the course of the 2025 financial year.
Geschäftstätigkeit in den Segmenten
Three segments (until 31 December 2024)
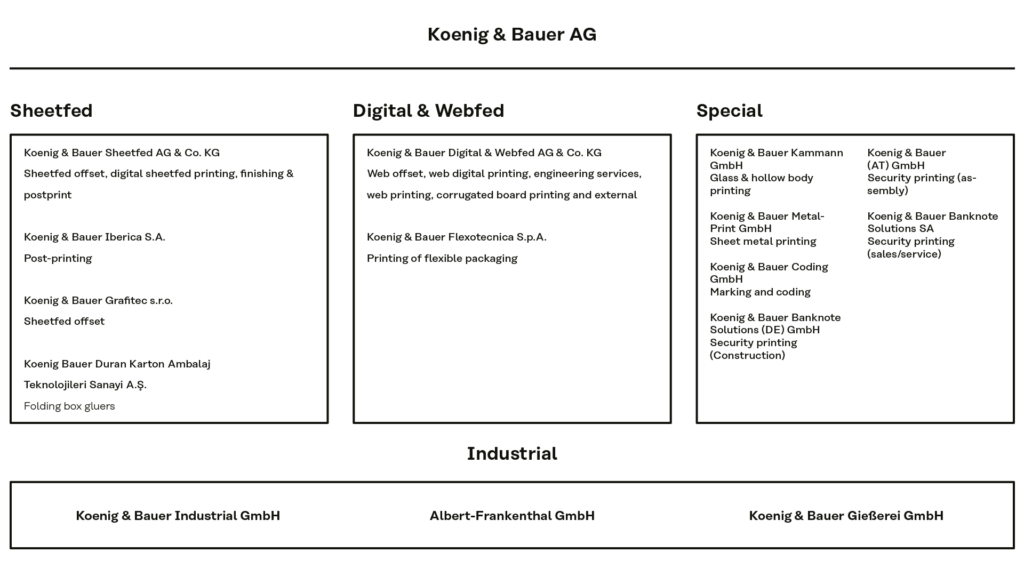
In line with its operating business, the internal reporting structure is divided into the following segments: Sheetfed, Digital & Webfed and Special. These also form the reportable segments in accordance with IFRS. Segment revenue is split into printing presses, services, including spare parts (service) and miscellaneous business. Services include both digital and classic services.
The Sheetfed segment offers a comprehensive range of sheetfed offset presses under the “Rapida” brand – from half to super-large formats – for packaging and commercial printing. In addition to classic sheetfed offset technology, it offers a digital printing solution in the form of the VariJET 106 via the joint venture with Koenig & Bauer Durst. The sheetfed digital printing press can also be equipped with sheetfed offset units and postprint facilities for hybrid production. The segment addresses the growing packaging market with a 360-degree packaging workflow for folding carton production. This covers all main production steps: analogue, digital or hybrid printing and finishing of the sheets, flatbed or rotary punching, folding and gluing of the printed and punched sheets and finished packaging using folding box gluing machines. The range is supplemented by comprehensive service and support with a particular focus on “Technology – Service Select” and “Productivity – Service Complete”. The latter includes, for example, the seamless digital workflow and digital products such as KYANA for process optimisation and VisuEnergy X for sustainable energy management.
The following chart shows the revenue generated from press and service business in the Sheetfed segment. The share of service business widened slightly to 24.3% over the previous year (20.9%) due to the smaller proportion of press business. Efforts are continuing to achieve the Group target of around 30%.
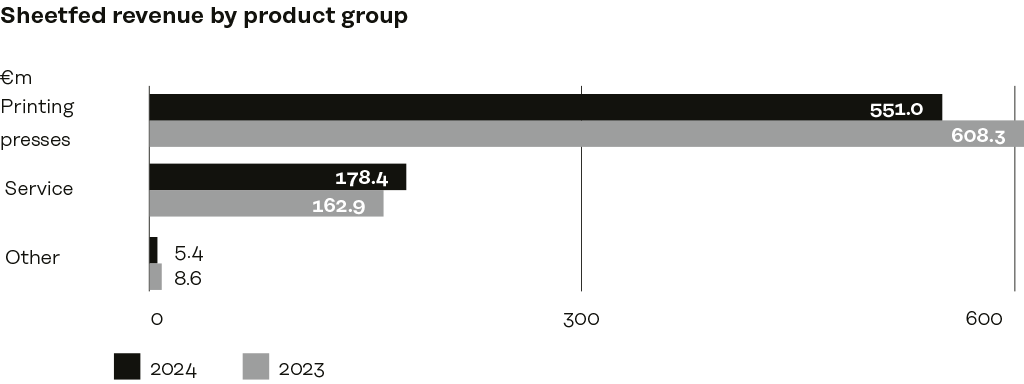
The Digital & Webfed segment offers a broad range of printing presses and systems that cover the letterpress printing (flexo printing), planographic printing (web offset) and digital printing processes.
In addition to web offset presses for newspaper, heatset and publication printing, the range also includes digital web presses. One example is the RotaJET platform, which is the world’s only industrial digital printing press. In addition to the packaging and commercial printing submarkets, it also addresses industrial printing, specifically decorative and beverage carton printing. Fitted with flexo systems and painting options, the RotaJET enables hybrid production processes. The web digital printing activities are supplemented with the HP PageWide T1190 and T700 printing systems for pre-printing corrugated-board cover layers and the HP PageWide T500 for monochrome letterpress printing, which are assembled in conjunction with HP.
The range also includes CI flexographic printing presses in various performance classes, which permit a modular structure with up to ten printing units and optional inline finishing units. Suitable for printing plastic films, paper and laminates, they are primarily used in the production of flexible packaging, especially for the food industry.
Various automation modules aligned to the individual needs of the web presses – for example, integrated paper logistics and tailor-made workflow solutions – are available.
Following the acquisition of Celmacch Group S.r.l. in 2022 in combination with Celmacch’s proprietary highboard corrugated board system and chroma product range, Koenig & Bauer addresses all price and performance classes for corrugated board direct printing. In collaboration with the Koenig & Bauer Durst joint venture, the range is supplemented with a post-print digital printing solution.
In addition to the range of presses, the segment offers comprehensive services such as upgrades and retrofits as well as remote monitoring using digital tools, tailor-made training and individual service contracts.
The following chart shows the revenue generated in press and service business in the Digital & Webfed segment. As in the previous year, 40.7% of the segment’s revenue was accounted for by services, with newsprint presses exhibiting a downward trend.
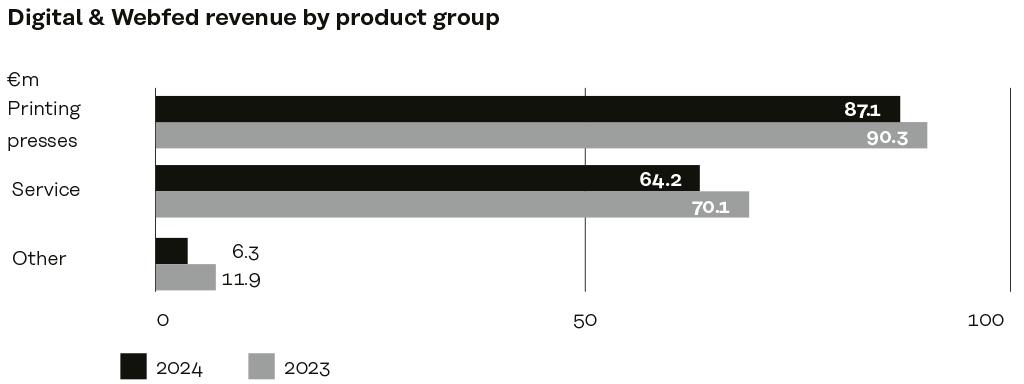
The Special segment comprises the activities pursued by Banknote Solutions (banknote and security printing), Kammann (direct decoration of hollow bodies), MetalPrint (metal packaging) and Coding (marking solutions for all industries).
Banknote Solutions develops specialised presses for banknote and security printing. The range of services also includes expertise in banknote and security design, the related design software, prepress solutions and security elements. These products and services are used by central banks and private printers to produce banknotes. The range is supplemented by innovative security and authentication solutions, such as the ValiCash™ smartphone app for verifying banknotes, and by quality control systems for electrode foils in battery cell production.
Kammann supplies printing systems for the direct decoration of glass or plastic hollow containers. The following decoration methods are used: digital printing, screen printing, hot stamping and labelling. Hybrid solutions permit these processes to be combined in a single press, thus offering a high degree of flexibility in the design of the printed image and enabling special effects and unique designs for individual packaging solutions. Directly decorated glass containers are mainly used for cosmetics, perfume and spirits products in the premium segment.
MetalPrint provides end-to-end printing and painting lines in a wide variety of configurations. The range thus includes both offset and digital sheet metal printing presses, varnishing machinery and various drying systems with integrated exhaust air purification. To decorate a 3-piece can – which is mainly used for food – complete production lines that print, paint and dry tinplate sheets are utilised. With the recent introduction of digital printing solutions – METJET ONE in partnership with Neos and MetJET PRO in conjunction with DURST – MetalPrint is expanding the scope for individualisation and flexibility in production.
Coding complements the Special segment’s portfolio by offering labelling solutions for a wide range of industries, from pharmaceutical and cosmetics to automotive and electronics. Variable data, logos and barcodes are printed, marked and coded on different substrates on a just-in-time basis. Production reliability and speed in conjunction with an excellent typeface are of crucial importance in order, for example, to apply the best-before date or batch traceability information accurately. Manipulation-proof labelling and seamless product traceability are becoming increasingly important.
The following chart shows the revenue generated in press and service business in the Special segment. Whereas new press revenue declined slightly, the share of service business widened marginally as in the previous year. It stood at 37.1%, up from 33.4% in the previous year.
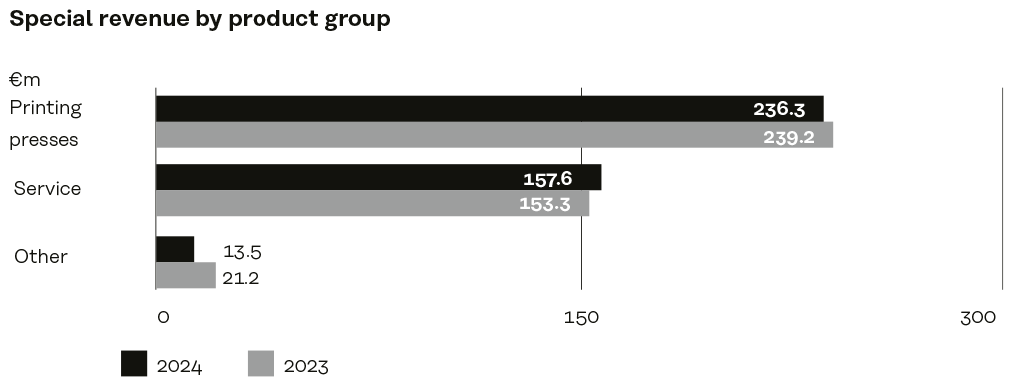
Two segments (in 2025)
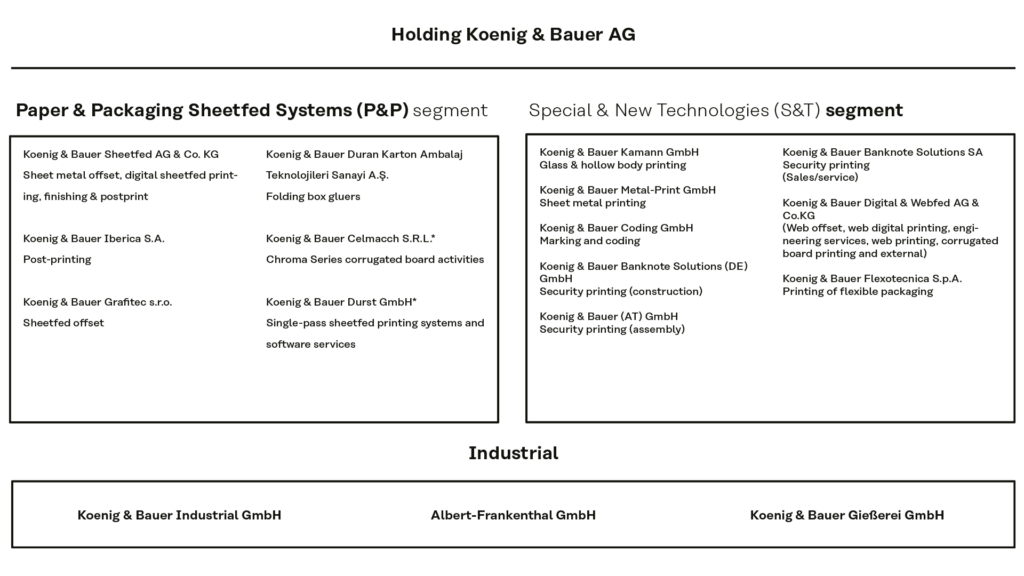
All the previous Sheetfed activities will be consolidated within the new Paper & Packaging Sheetfed Systems (P&P) segment. This also includes the activities of the Koenig & Bauer Durst joint venture. As well as this, the corrugated cardboard activities for the Chroma series bundled under the Celmacch joint venture, which were previously assigned to the Digital & Webfed segment, will be allocated to this segment due to the close technological and customer overlap between folding box and corrugated cardboard producers. In addition to commercial printing solutions, the P&P segment will be focusing on end-to-end solutions for the high-growth folding box and corrugated cardboard box markets, addressing all aspects such as the preprint stage with an integrated digital workflow and postprint processing.
Looking forward, the Special & New Technologies (S&T) segment will consolidate the previous activities of the Special segment (special presses for banknote and security printing, systems for industrial marking and coding and special systems for metal and glass/hollow container direct printing), as well as the remaining activities of the former Digital & Webfed segment. This includes web-based printing processes such as the “RotaJET” web digital printing presses and the systems developed in partnership with HP for preprinting corrugated-board liners and letterpress printing, CI flexo printing presses and web offset presses. The future S&T segment will also include the new autonomous Vision & Protection (inspection systems and product safety) and Kyana (former Digital Unit), as well as the joint venture established between Koenig & Bauer and PowerCo SE for the development of dry coating for battery cell production. The former Digital & Webfed segment will be reported on separately for a certain period in the interests of greater transparency.
Leitung und Kontrolle
Management and governance
Koenig & Bauer AG is a public limited company (“Aktiengesellschaft”) under German law with a dual management structure. Its Executive Board consisted of four members as of 31 December 2024:
• Dr Andreas Pleßke
(Chief Executive Officer; appointed until 31 December 2025)
• Dr Stephen Kimmich
(Deputy Chief Executive Officer, Chief Financial Officer and Segment Chief Executive Officer Special*; appointed until 31 March 2026)
• Christoph Müller
(responsible for the Digital & Webfed segment, appointed until 30 June 2026)
• Ralf Sammeck
(responsible for the Sheetfed segment, appointed until 30 June 2025)
The restructuring of Koenig & Bauer AG has resulted in changes to central responsibilities for operations as well as cross-sectional functions. Consequently, the previous role of a central Group COO will no longer be required. For this reason, a mutual agreement was reached between the company and Michael Ulverich, Chief Operation Officer – Production, Purchasing and & Logistics, under which he left the company as a member of the Executive Board effective 30 November 2024.
This change means that there is one business allocation plan up to 30 November 2024 and another one from 1 December 2024. The two business allocation plans presented show the allocation of responsibilities to the Executive Board areas and segments as well as the distribution of functional responsibilities.
Since 1 December 2024, further functions and areas of responsibility have been assigned to the first management level below the Executive Board and are supervised by the latter, which holds overall responsibility. Christian Steinmaßl joined the first management level below the Executive Board on 1 December 2024 and reports to the Executive Board. He is responsible for Industrial and Foundry, Group strategic purchasing, operational purchasing and scheduling, quality management and the Vision & Protection and Digital Unit.
As part of the strategic realignment of the Group and the planned transition to a new generation, Christoph Müller resigned on 10 March 2025 from his position on the Executive Board with effect from 31 March 2025. He will continue to assist Koenig & Bauer as an executive advisor.
From that date, Christian Steinmaßl will be responsible for Digital & Webfed within the new Special & New Technologies segment in addition to his previous responsibilities.
Goals and strategy
“Exceeding Print” corporate strategy
In December 2021, Koenig & Bauer adopted the “Exceeding Print” strategy, thus defining its medium-term strategic thrust. Reflecting the motto “Strengthen strengths”, the strategy focuses on the company’s proven core skills, expanding them systematically and innovatively in the interests of greater sustainability, digitalisation and modularity. Over the past three years, Koenig & Bauer has made significant progress in these key areas and thus positioned itself for the future. The presentation of new presses and digital solutions at drupa – the world’s leading trade fair for printing technology – highlighted the successes achieved.
Now the focus is on successfully establishing these innovations on the market with a systematic go-to-market approach and intensified sales activities. This development process underlines Koenig & Bauer’s transition into an agile technology group that is actively shaping the transformation of the printing and packaging industry and paving the way for future success.
… for more sustainability – bringing solutions to market in a targeted manner
Sustainability is one of the greatest challenges of our time and at the same time a significant opportunity. The packaging and printing industry must find a way that combines both ecological responsibility and business success, especially in the face of mounting cost pressure. Recent legislative changes, such as the new EU Packaging & Packaging Waste Regulation (PPWR), are forcing the industry to make profound changes. The purpose of this legislation is to reduce the amount of packaging waste, to encourage reuse and recycling and to harmonise packaging standards in the EU. In addition, the European product passport will be introduced and is to provide detailed information on the composition and disposal of products to ensure transparency and a functioning circular economy. These developments are closely linked to digitalisation, which is opening up new opportunities for tracking and optimising products and processes. In addition to the company’s own sustainability goals, regulatory framework conditions – particularly the European Green Deal – are key drivers of this development. Koenig & Bauer is meeting this dichotomy with innovative solutions that combine answers to ecological and business requirements. It is committed to the development and implementation of resource-saving technologies that promote energy efficiency, reduced consumption of materials and a circular economy. These technologies specifically support customers in implementing their own sustainability strategies. One example of this is VisuEnergy X, an energy management system that enables real-time monitoring of energy consumption, identifies potential savings and supports more resource-efficient production. In addition, the latest HighEcon and EcoTNV systems from Koenig & Bauer MetalPrint significantly help to reduce energy consumption. They cut gas consumption by up to 70% compared to older installations.
The presentation of the Green Dot Award by Koenig & Bauer to its customers forms an integral part of the sustainability strategy, highlighting the company’s commitment to environmentally conscious innovations in the printing industry. With the award, which was presented for the second time at drupa 2024, Koenig & Bauer is honouring the best practices by its customers that demonstrate the compatibility of environmental responsibility and business success. The award-winning best practices show that environmental awareness and business success go hand in hand: technologies that reduce the consumption of waste, energy and ink not only increase environmental friendliness but also boost the efficiency of production processes.
With its systematic go-to-market approach, Koenig & Bauer is ensuring that these innovative sustainability solutions are established on the market and driving sustainable change in the printing and packaging industry.
… for more digitalisation – bringing solutions to market in a targeted manner
The digital transformation of the printing industry is progressing – and
Koenig & Bauer is actively involved in shaping it. For the company, digitalisation encompasses not only digital printing presses but also digital products, workflow solutions, business models and processes as well as the targeted expansion of internal digitalisation.
At drupa 2024, Koenig & Bauer presented a series of digital innovations aimed at boosting efficiency, productivity and sustainability in the printing process. The solutions presented included Kyana, the company’s digital intelligence, which organised the live shows as a virtual co-host. The myKyana portal, the central platform of Koenig & Bauer’s digital product world, illustrated the transformative power of digitalisation for the printing industry.
Two other digital innovations – ValiPACK and FOLLOW – were also unveiled at drupa. ValiPACK is a brand security solution that offers protection against product counterfeiting by combining microstructures, special printing inks and digital watermarks, which can be verified via a smartphone app. FOLLOW is a connected packaging solution that transforms packaging into end-to-end, multimedia communication channels. In addition, FOLLOW permits the integration of information on ingredients, recyclability or product origin and thus meets future regulations such as the European product passport. This functionality highlights Koenig & Bauer’s strategy of developing sustainable packaging solutions that meet the future requirements of a transparent and responsible value chain.
Koenig & Bauer optimises its internal processes with digital solutions such as Google Workspace for mobile work and SAP S/4HANA for more efficient processes. In addition, it uses Gemini AI to improve knowledge management, for example, by providing employees quickly with information from internal databases. Multilingual communication is also facilitated, as documents can be translated into different languages. AI also contributes to process optimisation by analysing large amounts of data and rendering internal processes more efficient. The company attaches maximum importance to the protection of sensitive data. Strict privacy policies are in place to ensure that all data is kept confidential and used only for authorised purposes.
With its systematic go-to-market approach, Koenig & Bauer is ensuring that these digital innovations are introduced into the market in a targeted manner – and thus helping to boost the efficiency and competitiveness of the industry.
… for more modularity – bringing solutions to market in a targeted manner
The growing individualisation and complexity of the printing industry requires a new balance between standardisation and flexibility. Koenig & Bauer is stepping up to this challenge by pursuing a consistent modularisation strategy. The goal is to enable faster innovation cycles, more efficient production processes and greater adaptability through modular machine platforms.
At drupa 2024, the progress made in this area was presented – particularly at TechDay 2024, which was dedicated to knowledge transfer and the shared development of innovative solutions. One example of the modularisation strategy is the “Digital Twin” pilot project presented by Koenig & Bauer in collaboration with Siemens. Using the sheet feeder of a Rapida 106 as an example, it demonstrated how a standardised and modular automation platform can accelerate press development and commissioning in addition to optimising service and after-sales processes. The partnership with Siemens is also underpinning the further development of digital solutions. State-of-the-art technology allows detailed machine and condition data to be collected and analysed, providing the basis for innovative applications in predictive maintenance, performance optimisation and virtual product configuration.
As well as this, the modularisation strategy is being supported by the establishment of the Group Sales unit. In this way, synergistic benefits arising from cross-segment sales are being used to optimise cross-selling. The Group’s key account management acts as a trusted advisor, while brand ownership management promotes dialogue with international manufacturers and packaging suppliers on new printing and packaging technologies.
With its systematic go-to-market approach, Koenig & Bauer is launching these modular concepts on the market in a targeted manner. They enable customers to structure their production processes flexibly and individually, while at the same time benefiting from standardised components. The modularisation strategy thus helps to achieve increased efficiency, shorter development times and long-term competitiveness.
“Spotlight” on sustainable earnings growth
Koenig & Bauer is in the “go-to-market” phase with its “Exceeding Print” corporate strategy. However, external and internal factors have led to heightened complexity and rising costs. In order to lead the company strengthened out of this challenging market phase, which is characterised by delayed, inflation-induced increases in personnel and material costs, the Executive Board initiated the “Spotlight” focus programme at the end of 2023.
In February 2024, the programme was announced with the aim of prioritising initiatives and business models that boost earnings and financial strength, while deprioritising initiatives that do not directly impact earnings. Accordingly, the Group-wide project portfolio was to be scaled back to focus on critical modernisation, digitalisation and quality-cost and growth projects and initiatives. There was a particular need for action in the Digital & Webfed and Special segments to harness the strong potential for improving earnings. To this end, Koenig & Bauer worked on the “D&W 2.0” optimisation and earnings-enhancement project as well as the “BNSx” excellence project under “Spotlight”.
As the name suggests, the programme focuses on selected “spotlights” and, as announced, was scaled and detailed after drupa on the basis of real effects. It primarily entails measures to improve costs at the holding company and in the Digital & Webfed segment in Würzburg as well as in the Special segment at various locations. In line with the forecast issued at the beginning of the programme, all measures were identified, implemented and finalised in 2024 for the most part. The non-operating extraordinary items required for this mainly relate to adjustments to property, plant and equipment and personnel costs and amounted to €50.4m, thus slightly exceeding the upper end of the target corridor of €30 – 45m, and were recognised in the Group’s profit and loss. They are placing a burden on Group EBIT while simultaneously laying the foundations for profitable growth in future years. In total, around 300 full-time equivalents, the majority in Würzburg, were eliminated in the relevant spotlight areas via a guided voluntary program. This had a positive effect on EBIT in 2024, which was mainly attributable to personnel-related measures. This effect exceeded the expected upper edge of €20m and also contributed to the achievement of the updated annual forecast for 2024. In the course of the final implementation of all measures under the “Spotlight” focus programme, further expenses in the low single-digit million euro range are expected in the first half of 2025 to complete the project and underpin the Group’s sustainable earnings growth. The company expects gross savings of €40 – 50m in 2025 and €60 – 70m in 2026.
The “spotlights” break down as follows as of 31 December 2024:
In order to focus on important areas, the Group project portfolio was scaled back. This took different forms, mainly in the Special segment. During the ongoing implementation of the “Spotlight” programme, Koenig & Bauer MetalPrint GmbH identified additional need for action and further potential. In the “Metal 2.0” project, the Executive Board decided to discontinue the CS-MetalCan project for 2-piece beverage can printing in addition to the personnel and material costs adjustments already agreed. This caused the above-mentioned difference of €5.4m. Looking forward, MetalPrint will focus on the growth field of digital printing in addition to maintaining its market-leading position in offset printing presses and coating lines for the metal printing market. In the Digital & Webfed segment, on the other hand, the focus was on reducing complexity. Looking forward, individual variants, modules, additional functions or features will no longer be offered, especially in the flexo sector. Priority is to be given to modernisation, digitisation, quality projects and growth initiatives. By re-prioritising Group-wide projects and initiatives, further effects were achieved, resulting from savings in external services, for example. Internal resources that were freed up were allocated to projects and initiatives that are critical for operations and have an impact on earnings.
The “D&W 2.0” optimisation and earnings-enhancement project under the leadership of Dr Andreas Pleßke includes organisational, operational and structural measures to safeguard earnings opportunities and reduce costs in the growth markets for flexible packaging, digital printing and corrugated board. The organisational measures have been largely implemented: with effect from 1 June 2024, Philipp Zimmermann assumed the management of Koenig & Bauer Digital & Webfed AG & Co. KG from Christoph Müller, who, as the Executive Board member responsible for Digital & Webfed, will concentrate on sales, service and strategic partnerships to a greater extent. This step also laid the foundations for the ongoing transition to a new generation. Another major operational focus is on eliminating trailing and start-up costs for new product launches in the digital and corrugated board sector as well as streamlining and reconfiguring value-adding and non-value-adding structures and processes in the segment. The overall objective of the structural measures implemented is to overcome the loss situation in the segment by taking internal measures more independently of market expectations and revenue performance over a very manageable period.
In the “BNSx” efficiency and earnings enhancement project, overseen by Dr Stephen Kimmich, the focus is on implementing profitability- and earnings-enhancing packages of measures to ensure that the Special segment can sustainably return to its original above-average performance. Therefore, the personnel measures also include MetalPrint and Coding in addition to Banknote Solutions. Following the completion of major R&D projects, the “BNSx” project is to optimise the operational value-creation structures at the site in Mödling (Austria), as well as the overall responsibility of the business unit in Lausanne (Switzerland) and various support and specialist functions in Würzburg. In addition, further targeted measures are being adopted to accelerate the successful market launch of the technologies developed in the Special segment over the past five years and to scale these accordingly.
At Koenig & Bauer AG as the holding company, inflation-induced increases in personnel and material costs were addressed with a package of efficiency measures. The rightsizing of the segments carried out as part of “Spotlight”, particularly in the Digital & Webfed segment, required an adjustment to the size and structure of the holding company. In connection with the reorganisation of the Koenig & Bauer Group, which was announced on 28 November 2024, the number of segments was reduced to two. Consequently, Koenig & Bauer AG as the holding company is streamlining its tasks and assigning more operational responsibilities to the two segments. In addition to pursuing the Group’s strategic responsibilities, the holding company will continue to provide shared services for all Group subsidiaries, including IT, HR, IR, communications, central purchasing and financial services. The members of the Executive Board are closely integrated in the strategic management of the segments. Looking forward, this will make it possible to reduce the number of members to just two, namely Chief Executive Officer and Chief Financial Officer. In the course of 2025, further steps to reorganise the Executive Board will be taken incrementally.
Markets addressed and growth opportunities
With its range of products and services, Koenig & Bauer addresses the sub-markets of packaging, banknote, security, industrial, commercial and publication printing and seeks to make proactive use of market opportunities. Each of these markets offers different growth opportunities, which are described below.
Future opportunities in packaging printing
The Koenig & Bauer Group’s focus is on structural and sustained growth in packaging printing. In terms of substrate, cartons (corrugated cardboard boxes, folding boxes and packaging cartons for liquids) are the largest group of packaging materials, followed by flexible packaging, hollow plastic bodies, metal and glass packaging. The company offers products and solutions for all these sub-markets. Several factors are driving growth in packaging printing every year. The most fundamental factor is the steady growth in the world population and, in particular, the increasing number of people who have a medium annual income. Accordingly, the growth in packaging printing correlates with the growth in global gross domestic product (GDP). In addition to rising global consumption, packaging consumption is benefiting from the boom in e-commerce, smaller sizes due to a greater number of one-person households and heightened regulatory requirements. New online markets for food, beverages, pharmaceuticals, cosmetics and fast-moving consumer goods, as well as the trend towards quick commerce, the next stage of e-commerce, are additionally spurring packaging consumption. What is clear, however, is that e-commerce has emerged as the permanent winner of the Covid-19 crisis. On average, global packaging printing is growing at an annual rate of around 4% according to various industry studies, with higher growth rates being registered for flexible packing and boxes. For Koenig & Bauer, the packaging printing markets for food, beverages and pharmaceuticals are particularly attractive as they are less cyclical. Alongside the rising demands of consumer goods producers with respect to product protection, quality, flexibility, cost efficiency and delivery periods, trends in favour of more complex, elegant and colourful packaging will additionally spur capital spending by packaging printers. Packaging is increasingly becoming a brand ambassador, an element supporting sales and an integral part of the product experience, underpinned by brand producers’ omnichannel strategies. Unboxing is a core element of the shopping and brand experience. This trend has also been spurred by the pandemic and is continuing unabated. As it is done at home, all customer contact arises in printed form during the “unboxing” stage. This means that flyers, brochures and other printed products are enclosed in the corrugated cardboard box. In addition, more and more exclusive department stores are sending products ordered online in corrugated cardboard boxes that are printed in several colours on the inside.
Growth opportunities through digital printing and in industrial printing
Analogue technologies such as flexo, gravure, offset and screen printing currently still dominate the global packaging printing sector. According to a recent study by Smithers, the proportion of digital printing accounts for around 4% of total global printing output in terms of quantity and around 18% in terms of value. This is set to increase to around 25% by 2034, while it will widen to only around 7% in terms of quantities. Compared to the previous Smithers study, the proportion of digital printing will therefore continue to increase slightly over the next few years. The greatest changes are expected in the area of packaging. Although digital printing is more expensive compared to analogue processes, it has some important advantages for customers as it permits individual, personalised and versioned printing, even in small print runs. Moreover, it reduces customers’ operating expenses by eliminating the need for expensive storage of the sheets, e.g. in the case of printed sheets. As well as this, a skilled printer is not required to operate a digital printing press, something which not only saves costs but also offers a clear road forward given the current shortage of skilled labour. In addition, makeready times and waste materials are eliminated. For reasons of cost, productivity and quality, digital processes such as inkjet printing will only be successful in industrially oriented packaging printing for applications that are economically viable for customers. Technically and economically solid digital printing offers good market opportunities for business models specialising in short runs, greater personalisation and versioning, greater format flexibility and short time-to-market periods alongside other advantages. This calls for strong customer orientation, operational flexibility and quality standards. Following the latest RotaJET orders, Koenig & Bauer sees great potential for this sophisticated, high-quality digital printing solution, because digital web printing opens up entirely new possibilities in the customisation of products, i.e. very small print runs, through to disruptive approaches by changing value chains. It can be assumed that gravure and flexo presses in particular will be replaced by high-performance digital presses for industrial applications over the next few years. Digital printing technology not only simplifies the complexity of design handling but also shortens the time from design to print and offers greater flexibility in order placement and customisation of products. This is an advantage in the light of the trend towards shorter runs, more individualised products and fast time-to-market production. Decors for furniture and flooring are printed products that are becoming more and more sophisticated and creative and are also being replaced increasingly quickly in everyday use. Digital printing is spurring the trend towards individuality and design change as it permits swift production even in very small printruns. In addition, manufacturers are able to test new ideas on the market at low cost and with minimum effort. With digital preprint and direct printing on corrugated board, products can not only be placed in the market safely using water-based, food-certified ink jet ink, for example, but also communicate product information to the end consumer and attract their attention by means of seasonal corrugated-cardboard displays at the point of sale (POS), for example. Packaging is thus increasingly taking on the function of a marketing and sales tool. The multitude of new products and the trends towards versioning and personalisation together with ever shorter marketing cycles are ushering in a change in production requirements for liquid packaging (beverage cartons) and, in the future, also film packaging. As a general principle, improved total cost of ownership is the main driver for the shift from analogue to digital production.
Global demand for banknotes creating stability in security printing
Thanks to its good project situation, very low cyclical exposure and very high barriers to market entry, Koenig & Bauer expects business in security printing presses to remain stable in the long term. Cash remains an indispensable and secure means of payment, especially in the second and third world. In view of the highly intense competition, the newly developed, innovative security features are a decisive differentiator and a unique selling point. Despite the increased use of digital payment methods, global banknote production continues to grow at a moderate rate. Growing prosperity and rising population numbers in emerging markets with their high cash ratios as well as widespread scepticism towards electronic payments mean that there will be no reversal in this trend in the market in the medium term, although developments in some countries will vary. Alongside intensive work on new products and security features, service business for the large installed base is being systematically expanded and will make a good contribution to Group earnings in the medium to long term. With packaging printing contributing a larger share of Group revenue, the influence of volatile security printing business will recede.
Stable conditions in the media-related printing segments
Koenig & Bauer anticipates stable business in sheetfed offset presses for commercial printing.
The global book market is proving to be flat to slightly expansionary. Industrial digital printing has also arrived in the publishing industry. For example, the Italian company Grafica Veneta, a company in the field of letterpress printing, has chosen its American location for a second RotaJET single-pass digital printing press. This means that even smaller runs can be printed more efficiently and in top quality. This allows a swift response to changing market requirements. The configuration of the entire system makes it possible to print and bind a book in less than one minute from the raw paper roll to the ready-to-ship pallet. This revolutionary feature in book printing has the potential to create a new business model in the industry. Web offset presses for newspaper and commercial printing are expected to decline in tandem with lower service business due to further press shutdowns and printshop closures.
Expansion of service with a focus on digitalisation
The Koenig & Bauer Group is more than just a producer of printing and postprint systems. The company sees itself as a provider of end-to-end solutions that help its customers achieve market success. Our services include inspection, maintenance and calibration as well as retrofits/upgrades and service contracts. In addition, spare parts, consumables and accessories for the presses can be ordered online via webshops. Training and consulting services are also provided because innovative presses together with qualified personnel and the identification of potential for improvement in the printshop workflow are crucial for achieving greater productivity and quality along the entire production process. Workflows in the printing industry are becoming increasingly digital and networked. Ever smaller print runs have to be produced in ever shorter times in a high quality and at a competitive price – in this respect, a large, globally and locally positioned, established, yet flexible company such as Koenig & Bauer is able to set itself apart from the competition. For this reason, the Koenig & Bauer Group offers integrated workflow solutions to boost productivity and competitiveness.
Remote diagnosis tools have been part of Koenig & Bauer’s control centre technology since 1995. Digitalisation is creating increasingly effective services in this area. “Visual ServiceSupport” gives users and hotline technicians a tool allowing them to see exactly what printers or service technicians see when they are standing in front of the press. They can view processes and sequences in the form of moving images and thus gain a quick and comprehensive overview of the state of the press. This facilitates communications, obviates the need for extensive descriptions and reduces the risk of misunderstandings compared with a conventional telephone conversation. “Visual ServiceSupport” thus helps to increase the first-time-fix rate in service cases. The augmented reality data glasses allow remote maintenance technicians to view exactly what the customer’s technicians also see. In this way, Koenig & Bauer saves its customers a lot of money and effort.
Koenig & Bauer’s integrated workflow solutions are based on the principle of the “networked print factory”, in which products, presses and tools constantly share information via RFID chips and sensors. The presses self-configure, switch between different jobs fully automatically and support the operators in their work. This requires tight integration of all business processes with production and the measurement and control systems fitted to the presses. It is achieved by linking data from sales, order preparation, planning, production, controlling, logistics and also web-to-print systems. Information from all process steps along the value chain is available enterprise-wide and in real time. This gives management a 360-degree view of the company. The demonstration centre for digital networking solutions in Radebeul has various workflow solutions on display. As different presses and programmes are used in each individual case, the optimum workflow cannot be bought off the peg, which is why Koenig & Bauer advises its customers individually.
With “Predictive Maintenance & Services”, the company offers its customers a pre-emptive service for its presses and systems up to 28 days in advance to identify faults before they occur and cause unplanned downtimes. This uses the sensor data and performance data of the presses installed and networked in the market to identify and proactively prevent a potential malfunction before it occurs using complex algorithms and artificial intelligence methods.
The “myKyana” digital customer portal offers customers access to all digital products and services from Koenig & Bauer. It gives customers access to service management, the performance data of their presses and an overview of the main key performance indicators (KPIs) of the press – at any time and from anywhere. The automated predictive maintenance service cases and the information provided by the service engineers assist in converting unplanned machine downtimes into planned ones. This enables customers to become faster, better and more efficient – with the goal of achieving almost 100% productivity.
Markets outside the printing industry
Koenig & Bauer has also discovered new markets for itself outside the classic markets of the printing industry. Examples include the partnerships with Volkswagen subsidiary PowerCo SE and Mitsubishi Electric in response to the expected increase in demand for lithium-ion batteries due to the growing popularity of electric vehicles. According to calculations by the Boston Consulting Group, supplies of lithium-ion batteries will need to increase tenfold by 2030 to meet market demand.
Partnerships and cooperations
Koenig & Bauer specifically uses partnerships and cooperations to promote innovation and growth, including outside the established markets. By working together, synergies can be harnessed and the defined goals achieved more quickly and more efficiently. The examples listed here – in the areas of machinery, consumables, digitalisation, new business and sustainability – provide an insight into the diversity of Koenig & Bauer’s partnerships and collaborations. This list is not exhaustive.
Partnerships and cooperations in digital printing: Since 2014, Koenig & Bauer has had a partnership with HP to develop the world’s widest digital printing press. The long-standing partnership strengthens
Koenig & Bauer’s position in web digital printing and entails the joint production of the HP PageWide T1190 and T700 systems for pre-printing corrugated-board cover layers and the HP PageWide T500 for monochrome letterpress printing. Established in 2019, the joint venture with the Durst Group develops and markets digital printing systems and addresses digital direct printing on corrugated cardboard with the CorruJET and the DELTA SPC 130 and digital folding box printing with the VariJET 106. It has also been offering a digital printing press for metal decoration in the form of the MetJET ONE (multi-pass) since 2024. Also since 2024, the company has had a partnership with Neos for a single-pass digital printing press, the MetJET PRO.
After being strengthened in 2023, the partnership with Sealed Air Corporation (SEE) for RotaJET aims to connect the physical packaging of digital printing more closely with the digital world. Under the strategic partnership, the two companies’ hardware and software components are undergoing joint further development.
Partnership with Celmacch in the corrugated board market: Since 2022,
Koenig & Bauer Celmacch has been selling a comprehensive range of products in all price and performance classes for the corrugated board market with the Chroma range.
Koenig & Bauer places store by long-term partnerships in consumables. The partnership with ACTEGA (postprint technologies) was extended by three years in 2024, while System Brunner has been contributing its core colour management skills to Koenig & Bauer’s sheetfed offset technology for over ten years.
In digitalisation, Koenig & Bauer relies on a strong partner network to drive forward the transformation of the printing industry. The collaboration with Google Cloud (since 2023) enables the efficient management and processing of the enormous amounts of data that are generated in modern print production. With its focus on the manufacturing industry and dedicated industry solutions, Google Cloud supports the digital transformation of the printing and packaging world. Koenig & Bauer has been working with CoCoCo since 2024 to reduce the complexity of print production. The partnership aims to simplify the integration of different presses and software modules and thus enhance the efficiency of printing processes. An open and networked production environment that does not confine customers to a single OEM is the purpose of the partnership with Tessitura (since 2024). The integration of Koenig & Bauer’s myKyana portal achieves a high degree of flexibility, efficiency and transparency in production processes. The partnership with HYBRID Software (since 2023), a provider of software solutions for labelling and packaging, enables Koenig & Bauer to offer PrintFusion, an exclusive product for the packaging workflow on Rapida sheetfed offset presses, to optimise the entire production process. As well as this, Koenig & Bauer cooperates with the University of Applied Sciences Würzburg-Schweinfurt and the Steinbeis Research Centre Design & Systems.
Koenig & Bauer is opening up new business areas through strategic partnerships that go beyond the traditional printing business. Launched in 2023, the partnership with Volkswagen subsidiary PowerCo SE aims to develop a system for the solvent-free dry coating of electrodes, with a proof of concept expected by mid-2025. In the field of industrial image processing, the strategic partnership with Mitsubishi Electric, which was established in 2024, combines both companies’ strengths to offer standardised, high-quality components for image processing in electrode production. The jointly developed inspection module Qi<+>PRO enables in-line inspection of battery films and other web goods. The 2024 partnership with Graphic Security Systems Corporation (GSSC) links GSSC’s steganographic technologies with Koenig & Bauer’s printing presses and quality control capabilities to develop innovative solutions to combat counterfeiting.
Koenig & Bauer is committed to sustainability in the printing industry and beyond. The company is a partner in VDMA’s Blue Competence sustainability initiative and a member of the Healthy Printing Initiative, the 4evergreen alliance, the Holy Grail 2.0 project and the R-Cycle community. These activities underscore Koenig & Bauer’s commitment to promoting the circular economy and reducing the environmental footprint of the printing industry. In addition, it is committed to social responsibility, one example of this being the partnership with Aflatoun International to promote financial knowledge.
Planning, control and monitoring
Comprehensive set of tools for efficient Group planning and control
The established business management system with differentiated cost accounting provides management with a swift and meaningful set of figures for operational controlling, monitoring and strategic planning and management of the Group and the segments. In addition to central Group controlling for the overarching Group and segment management, the autonomously operating business units have access to controlling resources. The results of the annual strategy process culminate in high-level business planning and are presented in detail in the ensuing integrated budget planning phase. The planning horizon for high-level business planning and budget planning is five years. The budgets for the Group and the segments are based on detailed income statements, balance sheets and cash flow statements for all consolidated Group companies, which are prepared on a monthly basis in the first budget year. Forecasts for the current year are updated on the basis of the reported figures at the same time as the semi-annual and quarterly (Q1 and Q3) financial statements are prepared and also shortly before the end of the year. Scenario analyses simulate different market and cost parameters on a case-by-case basis. Monthly reporting tracks the current business and earnings situation as well as trends in net working capital and is discussed in the monthly earnings meetings. Service reporting permits coordination of the service activities. Roll-over liquidity previews with cash management provide an accurate view of the financial situation. A 24-month liquidity budget is prepared for this purpose. Regular reviews by Group management with the responsible segment managers addressing the economic and financial situation, current trends and forecasts supplement deviation analyses performed by controlling. Measures are defined in the event of any negative deviation in the interests of a swift and targeted response. Systematic implementation of the measures is tracked by close monitoring. Opportunities and risks are detected at an early stage by means of an established budget, forecast and reporting process. A risk early detection system has been established to monitor developments and to identify possible threats to the company’s going-concern status. The necessary decisions can be made at an early stage on the basis of this comprehensive assessment of Group and segment performance.
In the Koenig & Bauer Group, sales and operating EBIT (earnings before interest and taxes, EBIT) are the main financial performance indicators across all segments. In 2024, operating EBIT was introduced as the main financial performance indicator in addition to revenue to support the implementation of the “Spotlight” focus programme and to allow for non-operating extraordinary items arising from the restructuring measures. Operating EBIT therefore replaces EBIT as the main financial performance indicator as of 2024. Operating EBIT is defined as earnings before income taxes, interest income and expenses and other financial income, adjusted for non-operating items. EBIT is adjusted to eliminate the following items:
- Expenses / income from Group portfolio measures (acquisitions, disposals, adjustments and other portfolio-related measures, including changes in goodwill)
- Expenses / income from restructuring projects
- Expenses / income from consolidation changes during the year
- Expenses / income due to the first-time application of Group guidelines with regard to personnel adjustments – expenses for pension plans
In addition, the operating EBIT margin also counts as a financial performance indicator. It is defined as operating EBIT divided by revenue. Since 2024, Koenig & Bauer has been using the operating EBIT margin instead of the EBIT margin as a financial performance indicator.
In addition to these main financial performance indicators, the Executive Board receives reports on order intake, order backlog and service business indicators. Changes in capital employed are monitored on the basis of the cash conversion cycle. The ratio of inventories, prepayments made for inventories and trade receivables less trade payables and customer prepayments to revenue is calculated to determine this indicator. In addition to financial indicators, the Executive Board also tracks non-financial performance indicators, particularly quality assurance costs and staff development. Target agreements providing for variable remuneration components tied to Group, segment and/or personal goals for the year for all executives and non-pay-scale employees heighten motivation and commitment towards the achievement of the company’s goals.
Research and development
Koenig & Bauer again focused on digitalisation, workflow and sustainability solutions in its research and development activities in 2024. The results were presented at drupa 2024, which was held under the motto “Think digital” and “Be sustainable”, in the form of numerous innovations. Group research and development expenses equalled 4.3% of revenue in 2024 (previous year: 4.3%). As well as this, development costs equivalent to 1.1% of revenue were capitalised (previous year: 1.3%).
The Digital Unit presented the results of its research and development work at drupa 2024. This included myKyana, the central gateway to Koenig & Bauer’s digital product world. This platform comprises features such as Kyana Connect for data integration, Kyana Data for production analysis and Kyana Assist, an AI-powered customer service to help customers increase efficiency, profitability and sustainability. In addition, FOLLOW, a connected packaging solution, was unveiled. It transforms packaging into end-to-end, multimedia communication channels with augmented reality features and gamification elements. As well as this, it is geared to future requirements such as the digital product passport and thus helps to improve sustainability and traceability.
At drupa 2024, Vision & Protection presented the results of its research and development activities in the field of security and authentication solutions. These solutions complement the established approach to product protection by adding complex and secret features and additional, traceable and cryptographically secured levels of protection. Technologies such as Daktylo, Ovjera and Stegano demonstrated the effectiveness of these new protection mechanisms against counterfeiting, with a particular focus on material-saving and, thus, sustainable approaches.
The Sheetfed segment demonstrated the technical innovations derived from its research and development work concerning the end-to-end packaging workflow – from prepress to printing and from punching to folding-box bonding. All the equipment presented at drupa – including the Rapida 106 X, the VariJET 106, the CutPRO X 106 rotary die-cutter, the CutPRO Q 106 SB flat-bed die-cutter and the Omega Alius 90 folding-box gluer – features the latest technological developments. PrintFusion, a control system for Rapida machines developed in collaboration with Hybrid Software, highlights the segment’s innovativeness along the entire value chain in the packaging workflow.
At drupa, Koenig & Bauer MetalPrint presented the results of the expansion of its digital printing expertise in the sheet metal printing market. These include the MetJET ONE developed with our partner Durst and the MetJET PRO announced with Neos, which set new standards in productivity.
In addition, the “Hydrogen-heated dryer” development project achieved the first positive results. Conventional printing and painting lines use gas-powered dryers to dry paints. By replacing gas with green hydrogen, carbon emissions during production can be significantly reduced, paying off in the more energy-intensive area of metal printing in particular.
In the field of digital web printing, the Digital & Webfed segment has developed the HP PageWide T500 for single-colour letterpress in conjunction with HP. The further development of the RotaJET is continuing to concentrate on printing films with water-based inks. At drupa, an AI-generated decor was also presented for the first time and printed on the RotaJET.
Strategic partnerships, such as those with Volkswagen subsidiary PowerCo SE and Mitsubishi Electric, enable Koenig & Bauer to apply established know-how in new areas of research and development. The results of these partnerships and further information on strategic alliances are described in detail in the chapter “Partnerships and cooperations” on page 32.